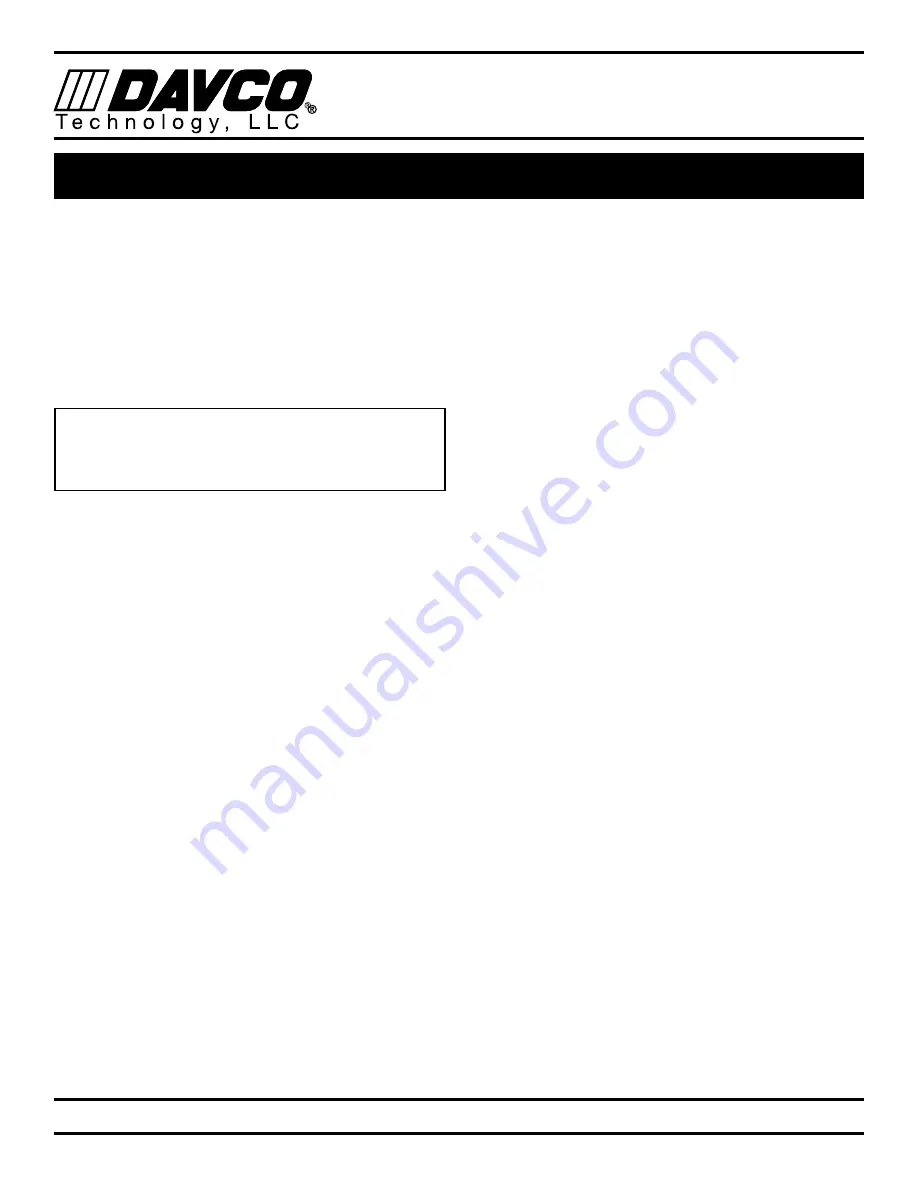
FUEL PRO
®
483
TECHNICAL MANUAL
T e c h n o l o g y , L L C
14
DAVCO Technology, LLC P. O. Box 487 Saline, MI 48176 800-328-2611 www.davco.com F1305 REV F
Every Fuel Pro 483 is factory tested for leaks and is marked
with a traceable number to show that it has passed produc-
tion testing .
Most field issues associated with leaks are related to loose
fittings . These leaks are easily eliminated by checking and
torquing the fuel fittings in the area of the leak . Some fit-
tings may also require the application of liquid Teflon sealer .
NOTE: All suction side fuel filters experience bubbles . It is
normal to see champagne size bubbles in the Fuel Pro 483
at the fuel outlet or at the lift pump .
IN ORDER TO RETURN A FUEL PRO 483 FOR EVALU-
ATION, THE FOLLOWING PROCEDURES/TESTS NEED
TO BE COMPLETED BEFORE REQUESTING A DAVCO
RGA (RETURN GOODS AUTHORIZATION) .
I . Air Leak: Air bubbles will be visible in the clear cover
of the Fuel Pro 483 if the leak originates from the fuel
tank up to the fuel filter . The following is a quick test to
isolate the air leak source .
A . Bubbles Visible: Remove the Fuel Pro 483 inlet
hose .
i . Install a jumper hose from the Fuel Pro 483
to the fuel tank (through the fill cap) or to a
container of fuel .
ii . Start the engine . If this eliminates the air
bubbles, the air source is at the fuel tank
fittings or hose connections .
1 . Tighten all fittings and connectors
2 . Retest
iii . If air bubbles persist, the air source is on the
Fuel Pro 483 side of the system:
1 . Tighten all fittings on the Fuel Pro 483 .
2 . Hand tighten the top collar .
3 . If the drain valve is suspected, install a
plug in place of the drain valve (for test
purposes only) .
iv . If air bubbles continue to persist, test as
follows:
1 . Remove the Fuel Pro 483 from the
chassis .
2 . Plug fuel outlet port . Do not remove
filter, cover/collar, vent cap, drain valve
and/or check valve . If the Fuel Pro 483
is equipped with a preheater, do not
remove the preheater .
3 . Apply 15 PSI of air pressure at the fuel
inlet . Immerse the Fuel Pro 483 in a
tank of water and look for air bubbles .
4 . Correct the source of the air leak and
retest .
B . Bubbles Not Visible: If there are symptoms of
sucking air (indicated by engine loping/rough run-
ning performance/power loss, etc .) and there are
no bubbles in the clear cover, the air leak is either
at the Fuel Pro 483 outlet fitting, vent cap o-ring,
the lift pump inlet connection, or the fuel hose/
connections to the lift pump . Inspect and tighten
fittings as needed .
II . Excessive Restriction: If the fuel level is at the top of
the filter, replace the fuel filter . The Fuel Pro 483 will not
cause excess system restriction if the fuel level is below
the top of the filter . The only exception is if the grom-
met is not installed in the bottom of the filter element .
III . Loss of Prime: When air is introduced into the fuel
system, (i .e . draining water from the Fuel Pro 483 or
when replacing the fuel filter) a check valve is needed
to keep the fuel system primed from the Fuel Pro 483
back to the fuel tank . A check valve is standard with all
Fuel Pro 483s .
C . To test for proper check valve operation, remove
the fuel inlet hose and open the vent cap . Fuel
should not flow out of the Fuel Pro 483, although a
slight seepage of fuel is normal .
D . If fuel drains back to the fuel tank, remove the
check valve assembly at the fuel inlet fitting . Disas-
semble the check valve assembly . Clean and in-
spect . Replace the assembly if any cuts, grooves or
nicks are evident in the ball or body seat . Reinstall
the check valve assembly .
DIAGNOSTIC PROCEDURES
Содержание FUEL PRO 483
Страница 21: ......