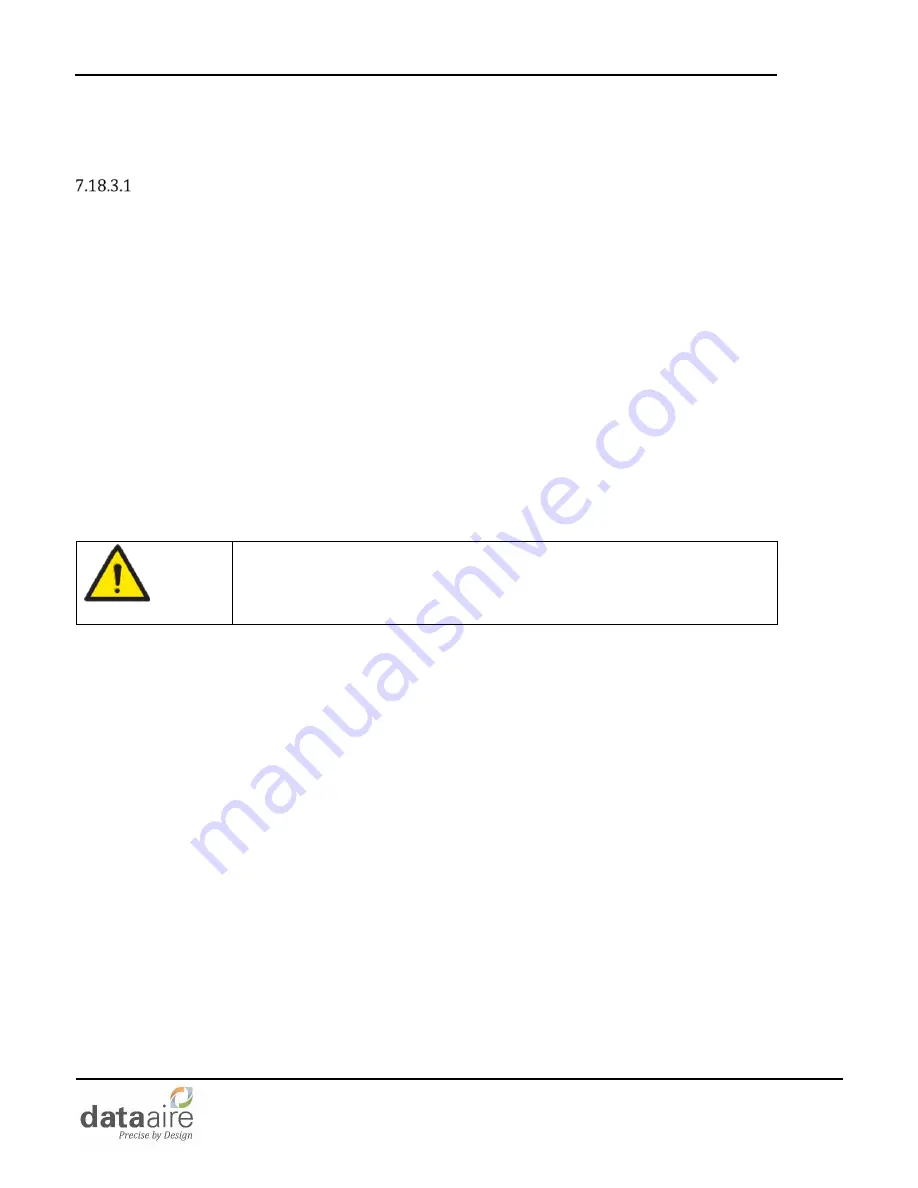
Installation, Operation and Maintenance Manual
Page
64
of
100
Check the color code of the moisture indicator on the sight glass. A positive indication means the filter-drier should
be replaced. If the drier is frosted or if there is a perceptible temperature change between the liquid line entering
and leaving the drier, an excessive pressure drop in the drier is indicated, and the drier should be replaced.
Refrigerant Filter Drier Replacement
1.
Disconnect all remote electric power sources to the unit.
2.
Remove all compressor and fan motor fuses for safety reasons. Remember to replace after finish with
change out.
3.
Use lock-out tag-out protection.
4.
Wear protective goggles and wear required. System contains oil and refrigerant under pressure.
5.
Remove and reclaim all refrigerant per your local codes.
6.
Check the replacement refrigerant filter drier is the same manufacture, model or part number and
configuration as the original part.
7.
Disconnect the refrigerant lines by heating the joint areas slowly and uniformly until braze material softens
and the tube can be pulled out of fittings. Use a damp cloth covering the filter drier as a precaution will
prevent overheating the valve body
8.
Deburr and clean connection lines as needed.
9.
Braze the replacement refrigerant filter drier in the same location and configuration as the original part
with Sil-Fos or equivalent silver copper phosphorus composition brazing material. No soldering allowed.
NOTICE
. The area should be vented thoroughly to prevent formation of
dangerous fumes which could result from the refrigerant in the presence of an
open flame.
10.
Use a damp cloth covering the refrigerant filter drier as a precaution will prevent overheating the refrigerant
filter drier.
11.
Braze replacement refrigerant filter drier to the connecting lines.
12.
Direct the flame away from the refrigerant filter drier body and avoid excessive heat on the body of the
drier.
13.
Evacuate and charge the system with the specified quantity of refrigerant
14.
Adjust refrigerant level as needed.
15.
Check compressor suction and discharge pressure.
16.
Check sub cooling and super heat values.
7.18.4
Thermostatic Expansion Valve (TXV) Replacement
1.
Check the replacement thermostatic expansion valve is the same manufacture, model or part number and
configuration as the original part.
2.
Disconnect the refrigerant lines by heating the joint areas slowly and uniformly until braze material softens
and the tube can be pulled out of fittings. Use a damp cloth covering the thermostatic expansion valve as a
precaution will prevent overheating the valve body.
3.
Deburr and clean connection lines as needed.
4.
Install the replacement thermostatic expansion valve in the same location and configuration as the original
valve.
5.
The equalizer must be in the install in the same orientation and location as the original.