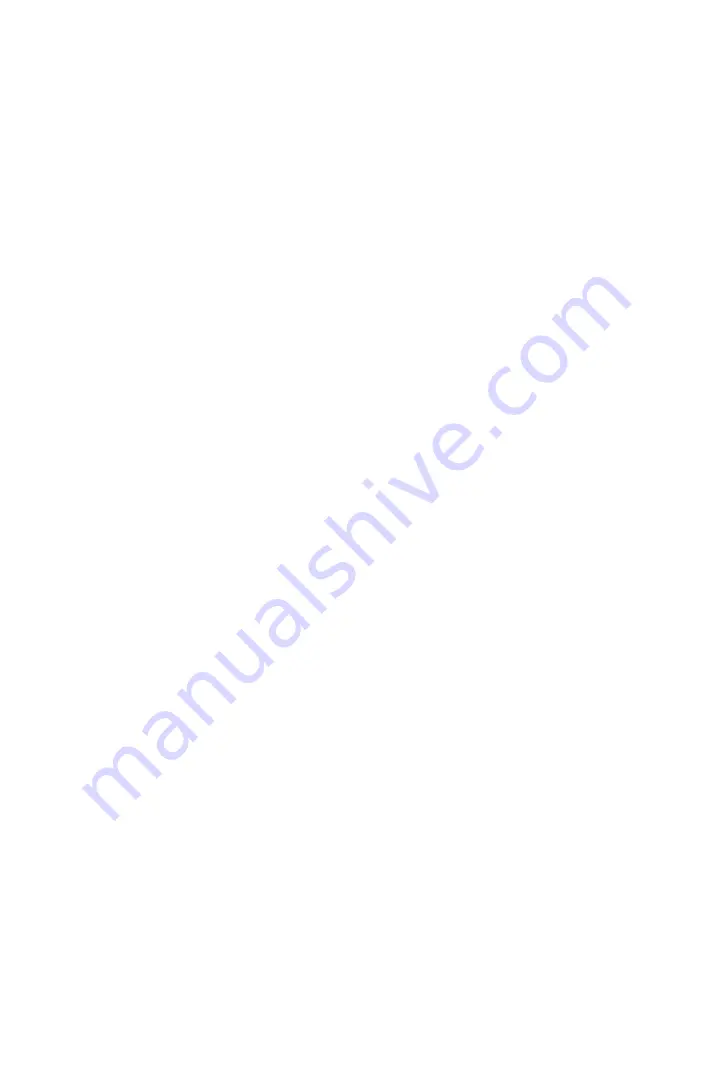
35
• Sharpener is located under outside light or overhead light
• Fiber optic lens or cable has been damaged
• Shank is larger than body of drill and correct diameter has not been manually input
Example:
Step drill
Auto diameter detect will not detect correct diameter:
• Diameter detection rod is bent or loose
• Diameter detection rod has been improperly installed.
• Incorrect diameter calibration
•
Shank of drill may be larger/smaller than actually body of drill
•
Drill flutes are worn or damaged
• MTO #1 button excessively worn or carbide disc has fallen off
Auto web detection does not display correct web thickness:
• Fiber optic sensor lens is dirty
• Fiber optic sensor is not calibrated correctly
• Fiber optic sensor is bad
• Old software installed
• 15% error margin allowed
Cutting edge is not positioned correctly at 12:00 after edge detection:
• Chip on cutting edge
• Burr on cutting edge
•
The fiber optic sensor has detected the split line as cutting edge
• Drill has a hook in the cutting edge – use the Advance Screen to compensate.
• Changing from extreme point angles
Example:
Converting a 180° drill into a 118° point angle
• Material build up on cutting edge
• A value was left in the Advance Screen
• Drill may have hooked cutting edge
Drill incorrectly split:
• Check offsets on the split point offset page
• Wheel calibration is off
• Check wheel edge offset on wheel offset page
• Did not align correctly
• Web thickness is wrong
Material take off varies:
• Check wheel face offset on wheel offset page
• Wheel calibration is off
• Spindle cartridge loose
Drill not touching hone brush:
• Check offsets on the Hone offset page
• Honing brush calibration is off
Содержание XPS-16+
Страница 1: ...Operating Instructions XPS 16 CNC Drill Grinder and Sharpener ...
Страница 2: ......
Страница 40: ...37 Notes ...
Страница 41: ...38 ...