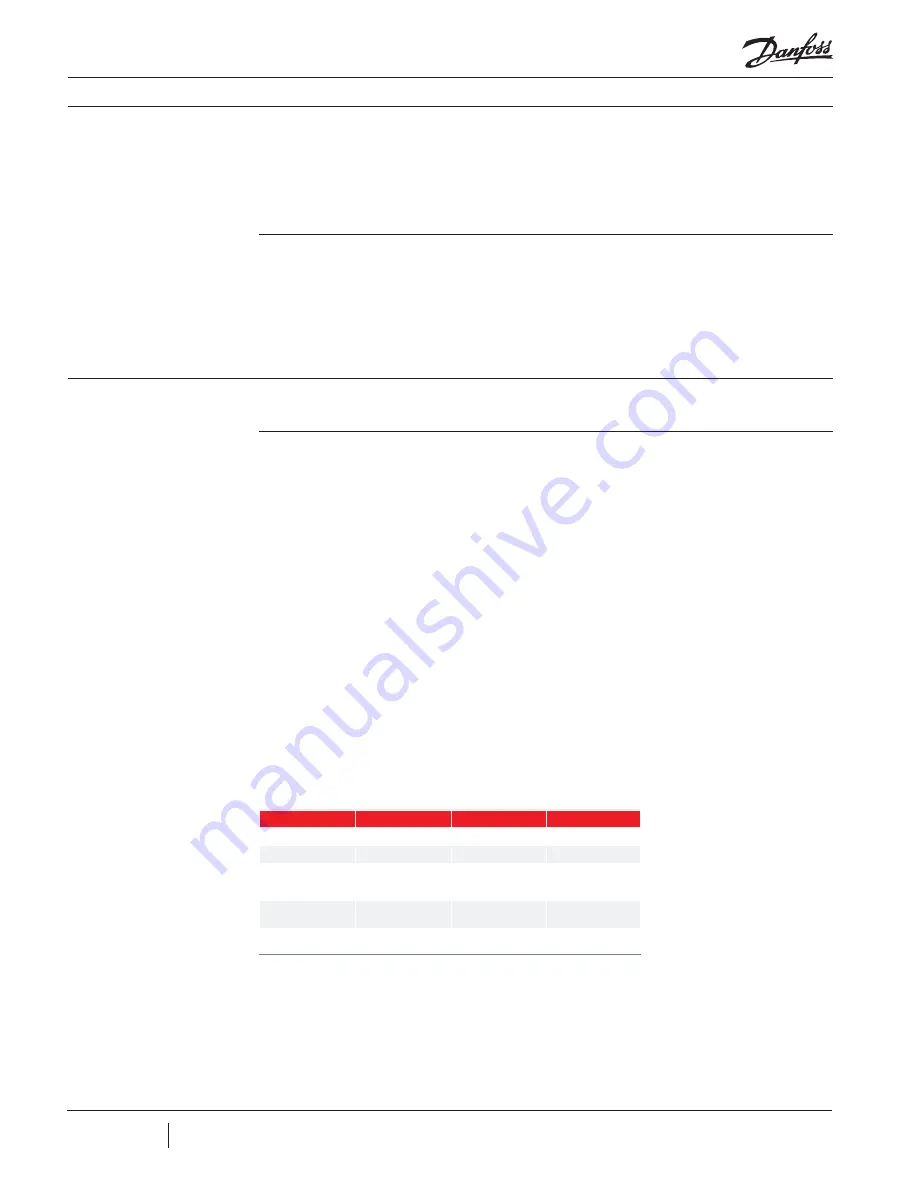
Page
36
of
73
M-AI-VT-001-EN Rev.C.1
M-AI-VT-001-EN Rev.C.1
Refrigerant Piping Design
Refrigerant Cooling
Cold Plate Tube
General Requirements
Piping Design Guidelines
The Drive Module is equipped with refrigerant
cooling to aid and compliment the cooling air
fans. Most of the time, the air cooled heat sink
manages the cooling. Refrigerant cooling will
only operate under high ambient temperatures
and/or high compressor load. A separate liquid
refrigerant supply must be provided to the
module; the line must be sized and routed
to ensure that a full liquid seal is available at
all times.
The Drive Module is shipped with two copper
tubes on the top side for cold plate refrigerant
inlet and outlet purposes.
• The tube inlet must be fitted with the
provided orifice.
• The pressure control valve must be installed and
wired to the cooling plate outlet connection.
• The outlet connection must be piped to system
low side.
• The refrigerant inlet and outlet size is 10 mm
(3/8") and are located on the top of the drive
module.
Take all necessary precautions to prevent liquid
flood-back to the compressor during ON and
OFF cycles, particularly in multiple compressor
installations. This includes, but is not limited
to, the inclusion of a liquid line solenoid valve,
piping, evaporator and condenser arranged in a
manner that prevents free drainage of liquid to
compressor.
In accordance with refrigeration industry best
practices, the refrigeration piping system must
be clean and free of all debris; particles can
damage the compressor.
Each compressor MUST be fitted with its own
positive sealing discharge line check valve.
This valve MUST be selected as a minimum
pressure drop at full capacity and low ‘crack open’
pressure. It is recommended that the valve be
located after the properly designed discharge
cone adaptor, preferably close to the condenser
in the packaged system.
1. Installation of staging valves are recommended
on each compressor discharge line in the
multiple compressor systems to assist the lag
compressor startup.
2. It is recommended that a Load Balancing
Valve (LBV) be installed to support unloaded
operation and lag compressor start-up in
multiple compressor systems.
3. During the compressor staging process, to get
the lag compressor online, the system pressure
ratio should be below a maximum level of 2.0.
4. Recommended minimum pipe sizes are
provided in the following table:
In order to maintain maximum efficiency,
properly taper trumpets with smooth transitions
must be used to connect the compressor flanges
to the pipework. The discharge line exit transition
should not be at an angle greater than eight
degrees inclusive.
This section provides basic guidelines and
requirements for piping design the systems
equipped with VTT compressors. Follow the
refrigeration schematics for piping layouts.
Table 16
Recommended Minimum
Pipe Sizes
Pipe Line
VTT880
VTT1000
VTT1200
Suction
152 mm (6")
152 mm (6")
152 mm (6")
Discharge
102 mm (4")
127 mm (5")
127 mm (5")
Motor Cooling
Outlet
29 mm (1 1/8")
29 mm (1 1/8")
29 mm (1 1/8")
Drive Cooling
Outlet
22mm (7/8”)
22mm (7/8”)
22mm (7/8”)
Economizer
41 mm (1 5/8")
41 mm (1 5/8")
41 mm (1 5/8")