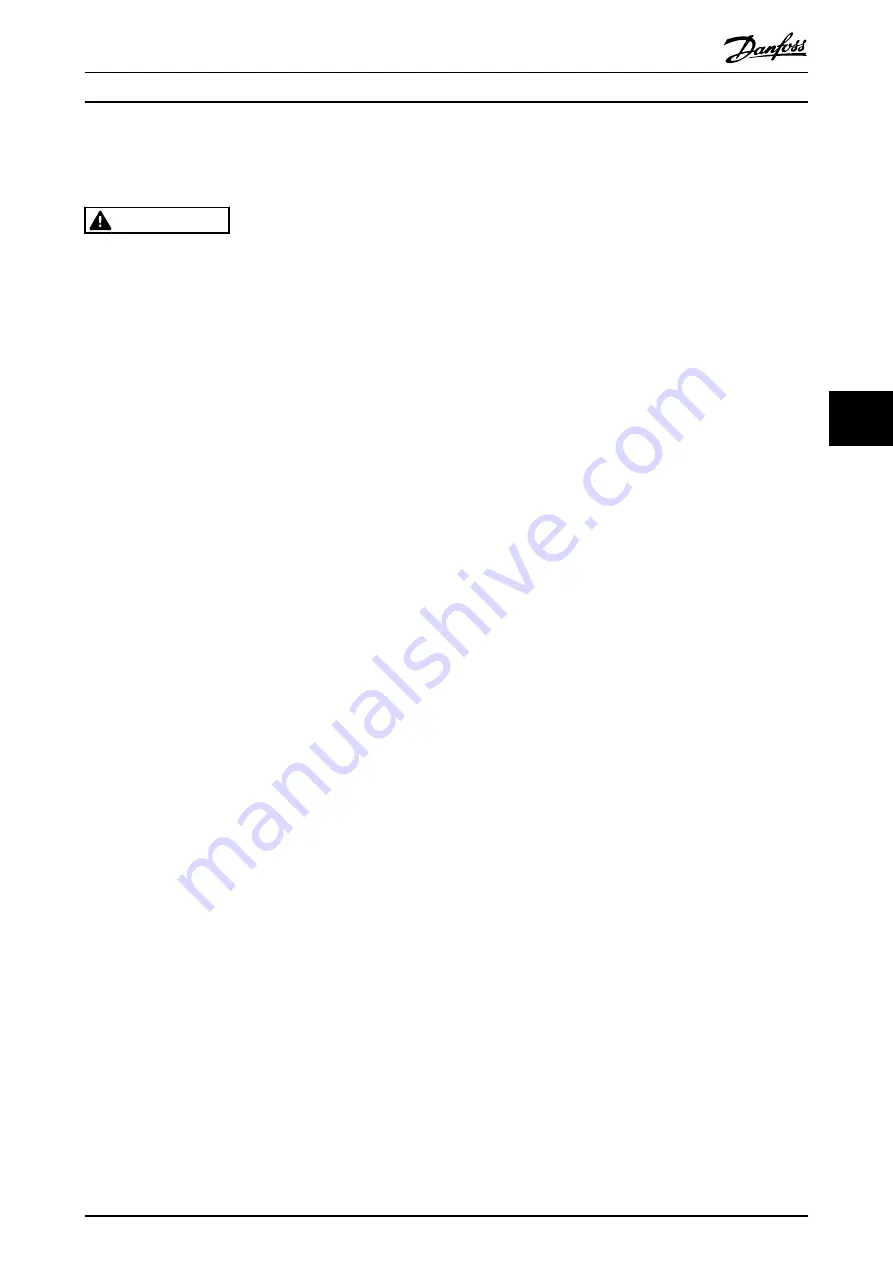
6 Commissioning
WARNING
UNINTENDED START
A servomotor that is connected to the electrical supply
network can start running at any time. This may be caused
by an external switch, a CAN bus command, a reference
signal, or clearing an error condition. Servomotors and all
connected devices must be in good operating condition. A
deficient operating condition may lead to death, serious
injury, damage to equipment or other material damage
when the device is connected to the electrical supply
network. Take suitable measures to prevent unintended
starts.
6.1 Switching on the Servomotors
The components of the servo system must be cabled
before power is applied to the servomotors.
This cabling provides the supply voltage as well as the
communication signals for the system. This is a
fundamental requirement for operation of the servomotors.
Carefully read the
VLT
®
ISD 410 Design Guide, MG75I
and
the operating instructions for the other ISD components
for detailed information.
The information listed below is solely intended as a brief
summary.
6.2 Connecting the Components
1.
Connect the mains supply line to the power
supply module and the control terminal strip of
the power supply module in accordance with the
wiring diagram in the
VLT
®
ISD 410 Design Guide,
MG75I
.
2.
Connect the DC supply from the power supply
module to the connection box and activate the
safety circuit.
3.
Connect the feed cable from the connection box
to the first servomotor by connecting the cable
leads on the connection box and the servomotor
using the threaded connectors.
4.
Using the loop cables intended for this purpose,
connect the other servomotors in the group.
5.
Fit a CAN terminating resistor on the last
servomotor.
6.
Connect the CAN bus to the connection box.
7.
Connect the encoder box (if present) to the CAN
network.
6.3 Functional Operation Test (before initial
power-up or operation)
Always check the following items before initial commis-
sioning, before commencing operation after extended
downtime, or before commencing operation after motor
overhaul:
•
Are all threaded connectors of mechanical and
electrical components firmly tightened?
•
Is the free circulation of cooling air (inlet and
outlet) assured?
•
Are the devices for protection against
overheating (temperature sensor monitoring)
operational?
•
Are the electrical connections OK?
•
Is contact protection in place for rotating parts
and surfaces that can become hot?
NOTE
The power-off brake may not be misused as a working
brake!
6.4 Parameter Configuration
The servomotors are controlled via the CAN interface.
The master software for this purpose is the CoDeSys
development system from 3S-Smart Software Solutions
GmbH.
Parameter setting can also be carried out via the ISD
Toolbox software.
See the
VLT
®
ISD 410 Design Guide, MG75I
for additional
information.
6.5 Test Run
After connecting the servomotors, always perform a test
run and ensure that the rotation directions have been
programmed properly.
Commissioning
VLT
®
ISD 410 Servomotor Operating Instructions
MG75D102 - VLT
®
is a registered Danfoss trademark
25
6
6