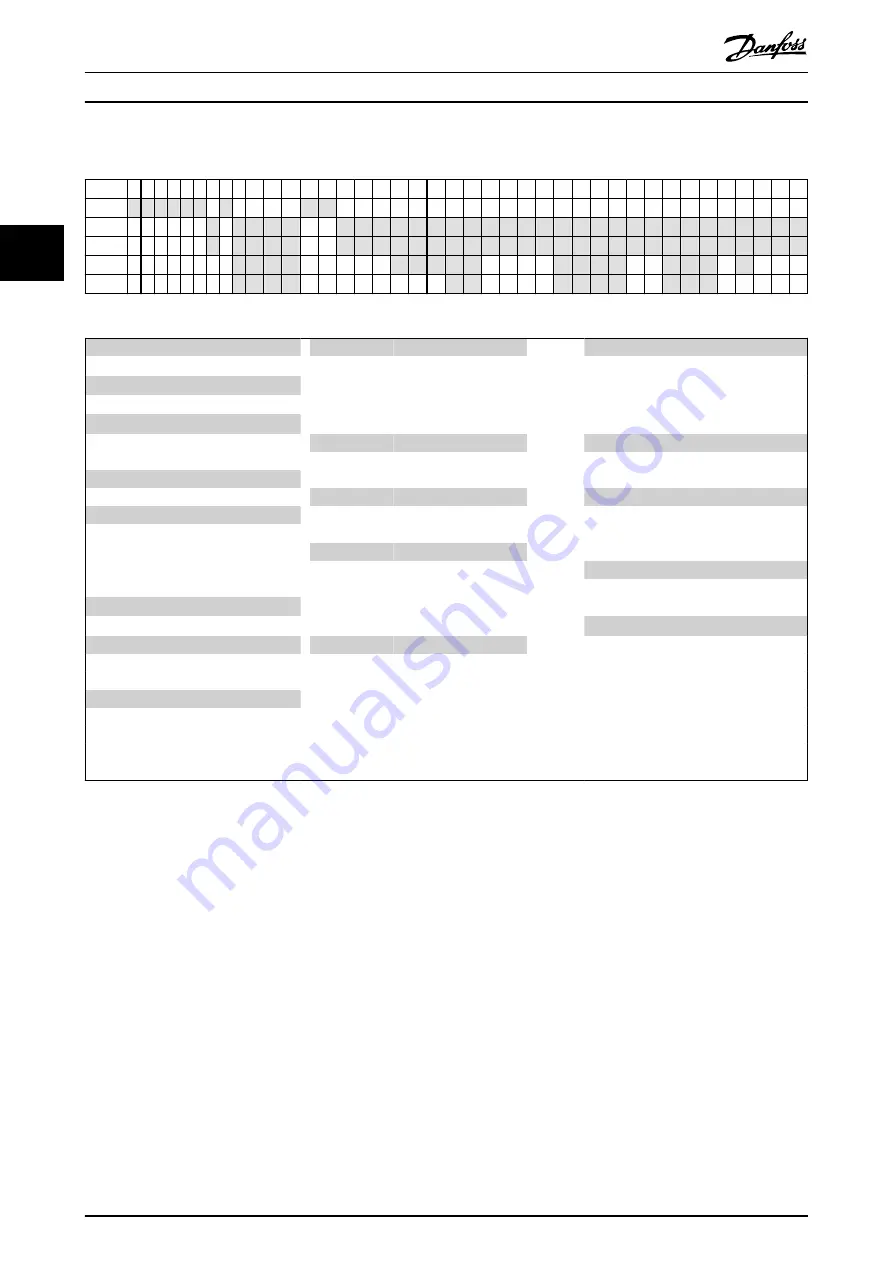
3.2.1 Servo Drive Types
Pos.
1 2 3 4 5 6 7 8 9 10 11 12 13 14 15 16 17 18 19 20 21 22 23 24 25 26 27 28 29 30 31 32 33 34 35 36 37 38 39 40
Fixed
I S D 5 1 0 T
D 6
Variant
A 0 1 C 5
E 5 4 F R X P L S X X T F 0 7 6 S X N 4 6 X S X S X
S 0 2 C 1
E 6 7 F S 1 E C S C O F F 0 8 4 C 0 N 4 0 B K S C X
0 2 C 9
F M 1 P N
F 1 0 8
N 2 9 C
0 3 C 8
E N
F 1 3 8
N 2 4
Table 3.2 Type Code
[01–03] Product group
[21–22]
Bus system
[33–35]
Motor speed
ISD
VLT
®
Integrated Servo Drive
PL
Ethernet POWERLINK
®
N46
Rated speed 4600 RPM
[04–06] Product variant
EC
EtherCAT
®
N40
Rated speed 4000 RPM
510
ISD
®
510
PN
PROFINET
®
1)
N29
Rated speed 2900 RPM
[07]
Hardware configuration
EN
Ethernet/IP
™
1)
N24
Rated speed 2400 RPM
A
Advanced
[23–25]
Firmware
[36]
Mechanical brake
S
Standard
SXX
Standard
X
Without brake
[08]
Drive torque
SC0
Customized version
B
With brake
T
Torque
[26]
Safety
[37]
Motor shaft
[09–12] Torque
T
Safe Torque Off (STO)
S
Standard smooth shaft
01C5
1.5 Nm
F
Functional safety
1)
K
Standard fitted key
1)
02C1
2.1 Nm
[27–30]
Flange size
C
Customized
02C9
2.9 Nm
F076
76 mm
[38]
Motor sealing
03C8
3.8 Nm
F084
84 mm
X
Without sealing
[13–14] DC voltage
F108
108 mm
1)
S
With sealing
D6
600 V DC-link voltage
F138
138 mm
1)
[39–40]
Surface coating
[15–17] Drive enclosure
[31–32]
Flange type
SX
Standard
E54
IP54
SX
Standard
CX
Customized
E67
IP67 (shaft IP65)
C0
Customized version
[18–20] Drive feedback
FRX
Resolver
FS1
Single-turn feedback
FM1
Multi-turn feedback
Table 3.3 Legend to Type code
1) In preparation
3.2.2 Motor Components
3.2.2.1 Shaft
The shaft transfers the motor force (torque) to the machine
coupled to the shaft.
The shaft material is C45+C or equivalent according to
EN 10277-2.
The ISD 510 servo drives can be sealed by a shaft seal
(optional) to achieve IP65 on the A-side of the motor (see
chapter 11.1.5 General Specifications and Environmental
Conditions
for further information).
3.2.2.2 Brake (Optional)
The optional mechanical holding brake is designed as a
single-disc brake. The emergency stop function can be
initiated at most once every 3 minutes and up to 2000
times in total, depending on the load.
The effective holding torque is:
•
Size 1: 2.5 Nm
•
Size 2: 5.3 Nm
The brake operates as a holding brake according to the
fail-safe principle
closed when no current
. It is powered
from the 24–48 V DC auxiliary supply. This enables low-
backlash load holding when no current is present.
Electrical data: Power consumption:
•
Size 1: 1.5 W
•
Size 2: 1.8 W
System Description
VLT
®
Integrated Servo Drive ISD
®
510 System
14
Danfoss A/S © 12/2015 All rights reserved.
MG75K102
3
3
Содержание VLT Integrated Servo Drive ISD 510 System
Страница 2: ......
Страница 101: ...Index Operating Instructions MG75K102 Danfoss A S 12 2015 All rights reserved 99...