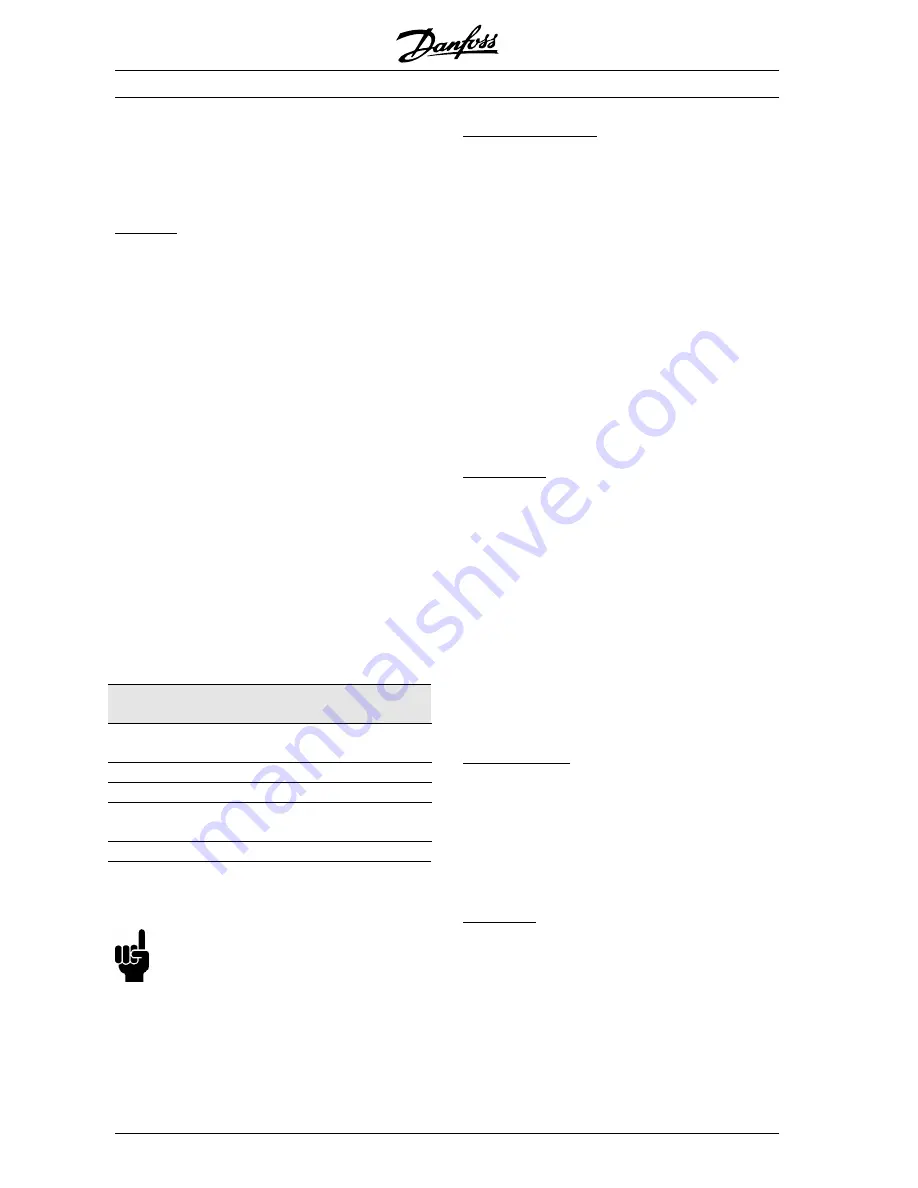
VLT
®
FCD Series
Parameters 414/415
Minimum/Maximum feedback
must also be preset to a value in the process unit
corresponding to the minimum and maximum scaling
values for signals that are connected to the terminal.
Reference
In parameter 205
Maximum reference, Ref
MAX
it is
possible to preset a maximum reference that scales
the sum of all references, i.e. the resulting reference.
The minimum reference in parameter 204 is an ex-
pression of the minimum value that the resulting
reference can assume.
All references will be added together and the sum
will be the reference against which regulation will
take place. It is possible to limit the reference range
to a range that is smaller than the feedback range.
This can be an advantage if you want to avoid an
unintentional change to an external reference mak-
ing the sum of the references move too far away
from the optimal reference. The reference range
cannot exceed the feedback range.
If preset references are desired, they are preset in
parameters 215 to 218
Preset reference
. See
description
Reference Function
and
Handling of Ref-
erences
.
If a current signal is used as the feedback signal, it
will only be possible to use voltage as an analogue
reference. Use the overview below to determine
which terminal is to be used and which parameters
are to be programmed.
Reference
type
Terminal
Parameters
Pulse
29, 33
305, 307, 327,
328
Voltage
53
308, 309, 310
Current
60
314, 315, 316
Preset
references
215-218
Bus reference
68+69
Note that the bus reference can only be preset via
serial communication.
NB!:
It is best to preset terminals
that are not being used to
No function
[0].
Differentiator gain limit
If very rapid variations occur in an application in ei-
ther the reference signal or the feedback signal, the
deviation between the reference/setpoint and the
process’s actual mode will change quickly. The dif-
ferentiator can then become too dominant. This is
because it is reacting to the deviation between the
reference and the process’s actual mode, and the
quicker the variance changes the more powerful the
differentiator’s frequency contribution becomes. The
differentiator’s frequency contribution can therefore
be limited in such a way that both a reasonable
differentiation time for slow changes and an appro-
priate frequency contribution for quick changes can
be preset. This is done using the speed regulation in
parameter 420
Speed PID Differentiator gain limit
and Process regulation in parameter 443
Process
PID Differentiator gain limit
.
Lowpass filter
If there is a lot of noise in the feedback signal, these
can be dampened using an integratedlowpass filter.
A suitable lowpass filter time constant is preset.
If the lowpass filter is preset to 0.1 s, the cut-off fre-
quency will be 10 RAD/sec, corresponding to (10 / 2
x
) = 1.6 Hz. This will mean that all currents/volt-
ages that vary by more than 1.6 oscillations per
second will be dampened. In other words, there will
only be regulation on the basis of a feedback signal
that varies by a frequency of less than 1.6 Hz. The
appropriate time constant is selected in Speed Reg-
ulation in parameter 421
Speed PID lowpass filter
time
and in Process Regulation in parameter 444
Process PID lowpass filter time
.
Inverse regulation
Normal regulation means that the motor speed is in-
creased when the reference/setpoint is greater than
the feedback signal. If it is necessary to run inverse
regulation, in which the speed is reduced when the
reference/setpoint is greater than the feedback sig-
nal, parameter 437
PID normal/inverted control
must
be programmed at
Inverted
.
Anti Windup
In the factory the process regulator is preset with an
active anti windup function. This function means that
when either a frequency limit, a current limit or a
voltage limit is reached, the integrator is initialised at
a frequency corresponding to the present output fre-
quency. This is a means of avoiding the integration of
a variance between the reference and the process’s
actual mode that cannot be deregulated by means of
a change of speed. This function can be deselected
in parameter 438
Process PID anti windup
.
✭
= factory setting. () = display text [] = value for use in communication via serial communication port
MG.04.A1.02 - VLT is a registered Danfoss trade mark
86