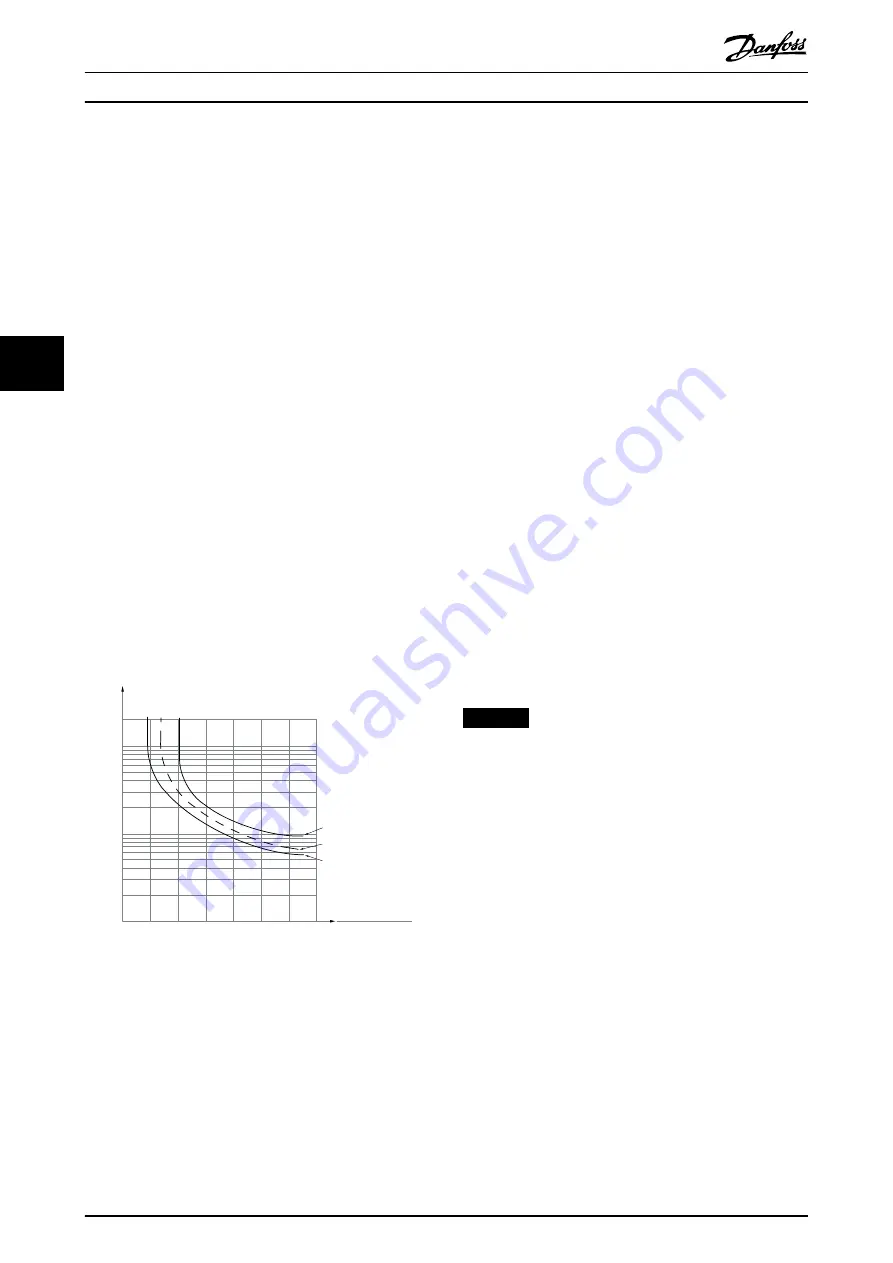
by comparing the 2 signals to optimize system
performance.
5.2.3 Motor Thermal Protection
Motor thermal protection can be provided via:
•
Direct temperature sensing using a
-
PTC- or KTY sensor in the motor
windings and connected on a standard
AI or DI.
-
PT100 or PT1000 in the motor windings
and motor bearings, connected on VLT
®
Sensor Input Card MCB 114.
-
PTC Thermistor input on VLT
®
PTC
Thermistor Card MCB 112 (ATEX
approved).
•
Mechanical thermal switch (Klixon type) on a DI.
•
Built-in electronic thermal relay (ETR).
ETR calculates motor temperature by measuring current,
frequency, and operating time. The drive shows the
thermal load on the motor in percentage and can issue a
warning at a programmable overload setpoint.
Programmable options at the overload allow the drive to
stop the motor, reduce output, or ignore the condition.
Even at low speeds, the drive meets I2t Class 20 electronic
motor overload standards.
1.2
1.0
1.4
30
10
20
100
60
40
50
1.8
1.6
2.0
2000
500
200
400
300
1000
600
t [s]
175ZA052.12
fOUT = 2 x f M,N
fOUT = 0.2 x f M,N
fOUT = 1 x f M,N(par. 1-23)
I
MN
(par. 1-24)
I
M
Illustration 5.1 ETR Characteristics
The X-axis shows the ratio between I
motor
and I
motor
nominal. The Y-axis shows the time in seconds before the
ETR cuts off and trips the drive. The curves show the
characteristic nominal speed, at twice the nominal speed
and at 0.2 x the nominal speed.
At lower speed, the ETR cuts off at lower heat due to less
cooling of the motor. In that way, the motor is protected
from being overheated even at low speed. The ETR feature
calculates the motor temperature based on actual current
and speed. The calculated temperature is visible as a
readout parameter in
parameter 16-18 Motor Thermal
.
A special version of the ETR is also available for EX-e
motors in ATEX areas. This function makes it possible to
enter a specific curve to protect the Ex-e motor. See the
programming guide
for set-up instructions.
5.2.4 Motor Thermal Protection for Ex-e
Motors
The drive is equipped with an ATEX ETR thermal
monitoring function for operation of Ex-e motors according
to EN-60079-7. When combined with an ATEX approved
PTC monitoring device such as the VLT
®
PTC Thermistor
Card MCB 112 option or an external device, the installation
does not require an individual approval from an
approbated organization.
The ATEX ETR thermal monitoring function enables use of
an Ex-e motor instead of a more expensive, larger, and
heavier Ex-d motor. The function ensures that the drive
limits motor current to prevent overheating.
Requirements related to the Ex-e motor
•
Ensure that the Ex-e motor is approved for
operation in hazardous zones (ATEX zone 1/21,
ATEX zone 2/22) with drives. The motor must be
certified for the specific hazardous zone.
•
Install the Ex-e motor in zone 1/21 or 2/22 of the
hazardous zone, according to motor approval.
NOTICE
Install the drive outside the hazardous zone.
•
Ensure that the Ex-e motor is equipped with an
ATEX-approved motor overload protection device.
This device monitors the temperature in the
motor windings. If there is a critical temperature
level or a malfunction, the device switches off the
motor.
-
The VLT
®
PTC Thermistor Card MCB 112
option provides ATEX-approved
monitoring of motor temperature. It is a
prerequisite that the drive is equipped
with 3–6 PTC thermistors in series
according to DIN 44081 or 44082.
-
Alternatively, an external ATEX-approved
PTC protection device can be used.
•
Sine-wave filter is required when
-
Long cables (voltage peaks) or increased
mains voltage produce voltages
Product Features
VLT® AutomationDrive FC 302
20
Danfoss A/S © 01/2018 All rights reserved.
MG38C202
5
5
Содержание VLT AutomationDrive FC 302
Страница 2: ......
Страница 211: ...Index Design Guide MG38C202 Danfoss A S 01 2018 All rights reserved 209...