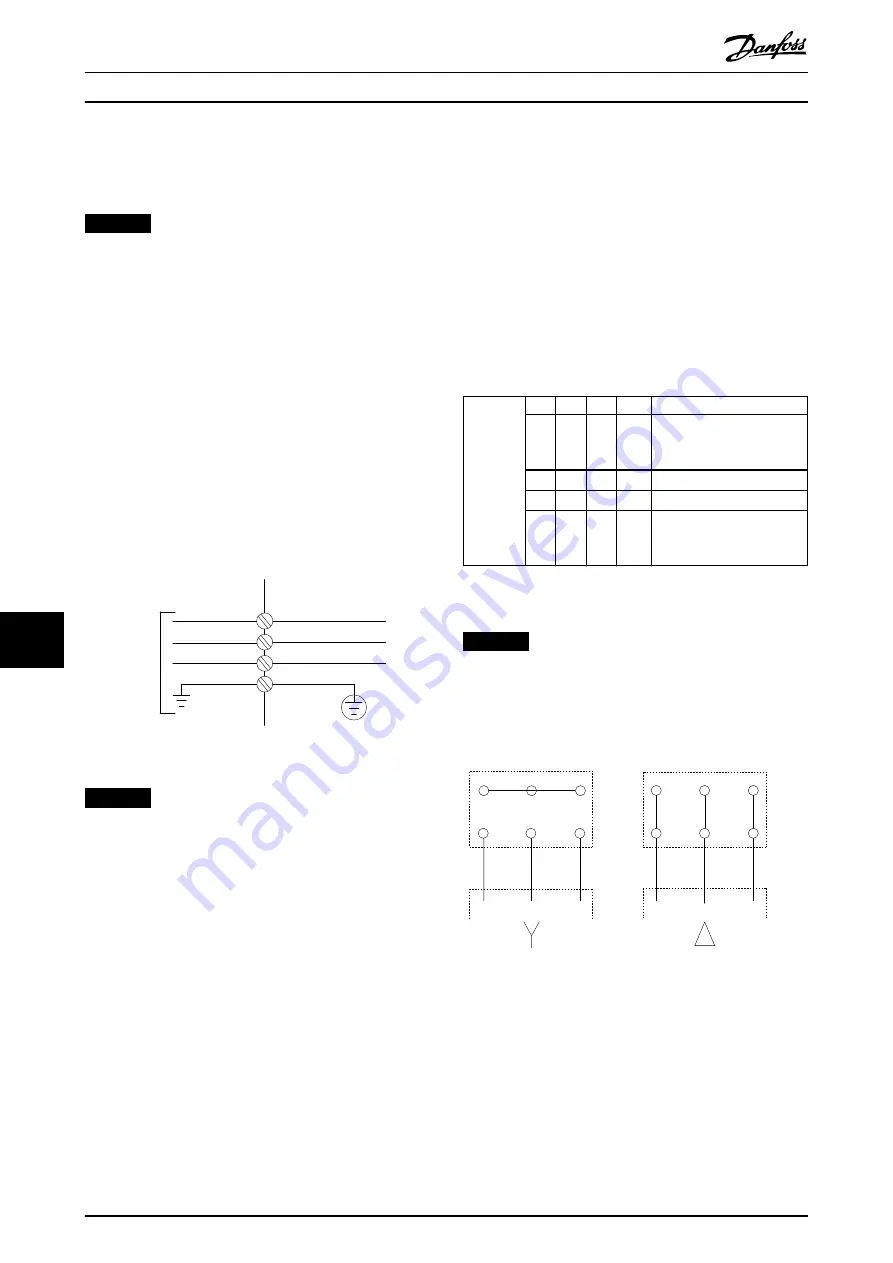
10.3 Connections
10.3.1 Power Connections
NOTICE
All cabling must comply with national and local
regulations on cable cross-sections and ambient
temperature. UL applications require 75
°
C (167
°
F)
copper conductors. Non-UL applications can use 75
°
C
(167
°
F) and 90
°
C (194
°
F) copper conductors.
The power cable connections are located as shown in
. See
for correct
dimensioning of motor cable cross-section and length.
For protection of the drive, use the recommended fuses
unless the unit has built-in fuses. Recommended fuses are
listed in
chapter 10.5 Fuses and Circuit Breakers
. Ensure that
proper fusing complies with local regulations.
The connection of mains is fitted to the mains switch if
included.
3 Phase
power
input
130BA026.10
91 (L1)
92 (L2)
93 (L3)
95 PE
Illustration 10.2 Power Cable Connections
NOTICE
The motor cable must be shielded/armored. If an
unshielded/unarmored cable is used, some EMC
requirements are not complied with. Use a shielded/
armored motor cable to comply with EMC emission
specifications. For more information, see
chapter 10.15 EMC-compliant Installation
.
Shielding of cables
Avoid installation with twisted shield ends (pigtails). They
spoil the shielding effect at higher frequencies. If it is
necessary to break the shield to install a motor isolator or
contactor, continue the shield at the lowest possible HF
impedance.
Connect the motor cable shield to both the decoupling
plate of the drive and the metal housing of the motor.
Make the shield connections with the largest possible
surface area (cable clamp) by using the installation devices
within the drive.
Cable length and cross-section
The drive has been EMC tested with a given length of
cable. Keep the motor cable as short as possible to reduce
the noise level and leakage currents.
Switching frequency
When drives are used together with sine-wave filters to
reduce the acoustic noise from a motor, the switching
frequency must be set according to the instructions in
parameter 14-01 Switching Frequency
.
Terminal
96
97
98
99
Description
U
V
W
PE
1)
Motor voltage 0–100% of
mains voltage. 3 wires out
of motor.
U1
V1
W1
PE
1)
Delta-connected.
W2
U2
V2
PE
1)
6 wires out of motor.
U1
V1
W1
PE
1)
Star-connected U2, V2, W2
U2, V2, and W2 to be
interconnected separately.
Table 10.1 Motor Cable Connection
1) Protected ground connection
NOTICE
In motors without phase insulation, paper, or other
insulation reinforcement suitable for operation with
voltage supply, use a sine-wave filter on the output of
the drive.
U
1
V
1
W
1
175ZA114.11
96
97
98
96
97
98
FC
FC
Motor
Motor
U
2
V
2
W
2
U
1
V
1
W
1
U
2
V
2
W
2
Illustration 10.3 Motor Cable Connection
Electrical Installation Con...
VLT® AutomationDrive FC 302
146
Danfoss A/S © 01/2018 All rights reserved.
MG38C202
10
10
Содержание VLT AutomationDrive FC 302
Страница 2: ......
Страница 211: ...Index Design Guide MG38C202 Danfoss A S 01 2018 All rights reserved 209...