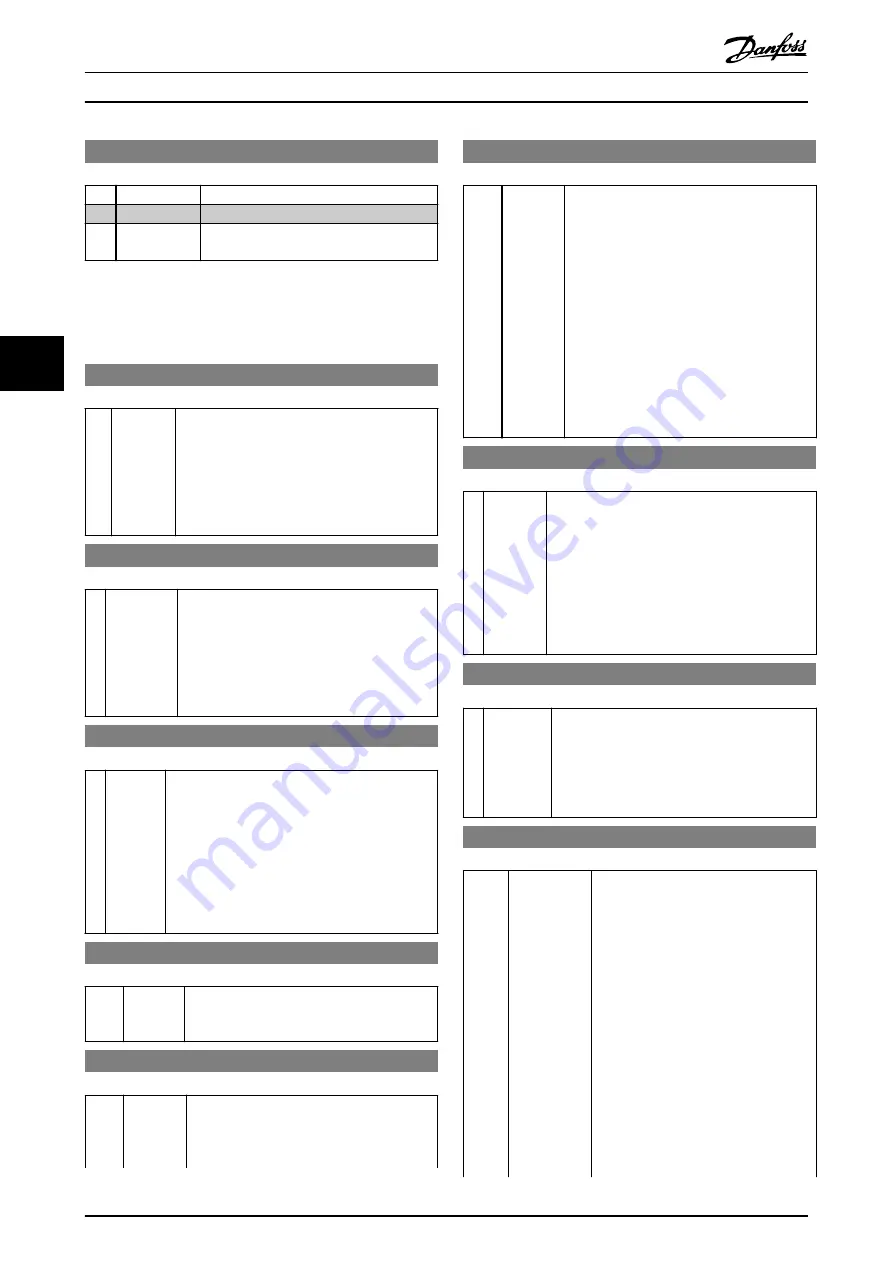
32-52 Source Master
Option:
Function:
[1]
*
Encoder 1 X56 Source master is encoder 1 on X56.
[2]
Encoder 2 X55 Source master is encoder 2 on X55.
[3]
Motor Control This source master can be an internal 24 V
encoder, encoder option, or resolver option.
5.6.4 32-6* and 32-7*, PID-Controller
Parameters
The 32-6* and 32-7* parameters optimise the controller.
32-60 Proportional Factor
Range:
Function:
30
*
[0–
100000]
The proportional factor indicates the linear
correction factor with which the deviation
between the current set and actual position is
evaluated and a corresponding correction of the
motor speed is made. The greater the value, the
stiffer the motor behaviour becomes. There is a
tendency to overswing if the value is too high.
32-61 Derivative Value for PID Control
Range:
Function:
0
*
[0–100000] The derivative value is the correction factor with
which the changing speed of a motor position
error is evaluated. The derivative value works
against the tendency to overswing due to a
high P-share and dampens the system.
However, if the derivative value selected is too
large, this leads to unstable motor behaviour.
32-62 Integral Factor
Range:
Function:
0
*
[0–
100000]
The integral factor is the weighting factor with
which, at time n, the sum of all motor position
errors are evaluated. The integral factor of the PID
filter causes a corresponding corrective motor
torque, which increases over time. Through the
integral share, a static position error is reduced to
0, even if a constant load is affecting the motor.
However, an integral factor, which is too large
leads to unstable motor behaviour.
32-63 Limit Value for Integral Sum
Range:
Function:
1000
*
[0–1000] 0 = integral off.
Limits the integral sum to avoid instability and
PID wind-up in case of feedback error.
32-64 PID Bandwidth
Range:
Function:
1000
*
[0–1000
[1/10%]]
0 = PID off.
The value 1000 means that the PID filter can
output the full command value. For a
Bandwidth of 500, only 50% of the set value is
32-64 PID Bandwidth
Range:
Function:
output. Thus, values less than 1000 limit the
P-share accordingly.
The bandwidth, in which the PID controller
should function, can be limited. For example,
to avoid the build-up of vibration for a
system, which could be jeopardised by
vibration. However, it is then necessary to
enter considerably higher values for the
parameters
32-65 Velocity Feed-Forward
and
32-66 Acceleration Feed-Forward
to achieve the
corresponding control. A system adjusted in
such a manner is not as dynamic as it could
be, but is considerably more stable and
experiences less uncontrolled vibration.
32-65 Velocity Feed-Forward
Range:
Function:
0
*
[0–
100000]
When a control has a limited bandwidth, a base
velocity must be set. This rules out that the
control entirely prevents the motor from running
due to the limit set. This parameter indicates the
value with which the velocity forward feed is
completed. When working with a normal PID
algorithm, the velocity feed-forward must always
be the same as the derivative factor to achieve
typical dampening derivative.
32-66 Acceleration Feed-Forward
Range:
Function:
0
*
[0–
100000]
Set the base acceleration whenever the
bandwidth is limited. This prevents the control
from not accelerating at all due to the limit set.
This parameter indicates the value with which
the acceleration forward feed is completed. For a
normal PID algorithm, this value is equal to 0.
32-67 Maximum Tolerated Position Error
Range:
Function:
20000
*
[1 to
1073741823
qc]
Defines the tolerance allowed between
the current actual position and the
calculated command position. If the
defined value is exceeded, the position
control is turned off and a position error
is triggered. The position error does not
affect the positioning accuracy. It
determines how precisely the theoret-
ically calculated path of motion must be
followed, without an error being
triggered.
However, to avoid frequent errors, the
value must be bigger than the capability
of the axis, to follow the position
generated by the trajectory generator. As
a guideline, it is wise to set the
quadruple of encoder counts per
Commissioning
Operating Instructions
34
Danfoss A/S © 04/2014 All rights reserved.
MG33R302
5
5
Содержание MCO 351
Страница 2: ......
Страница 57: ...Index Operating Instructions MG33R302 Danfoss A S 04 2014 All rights reserved 55...