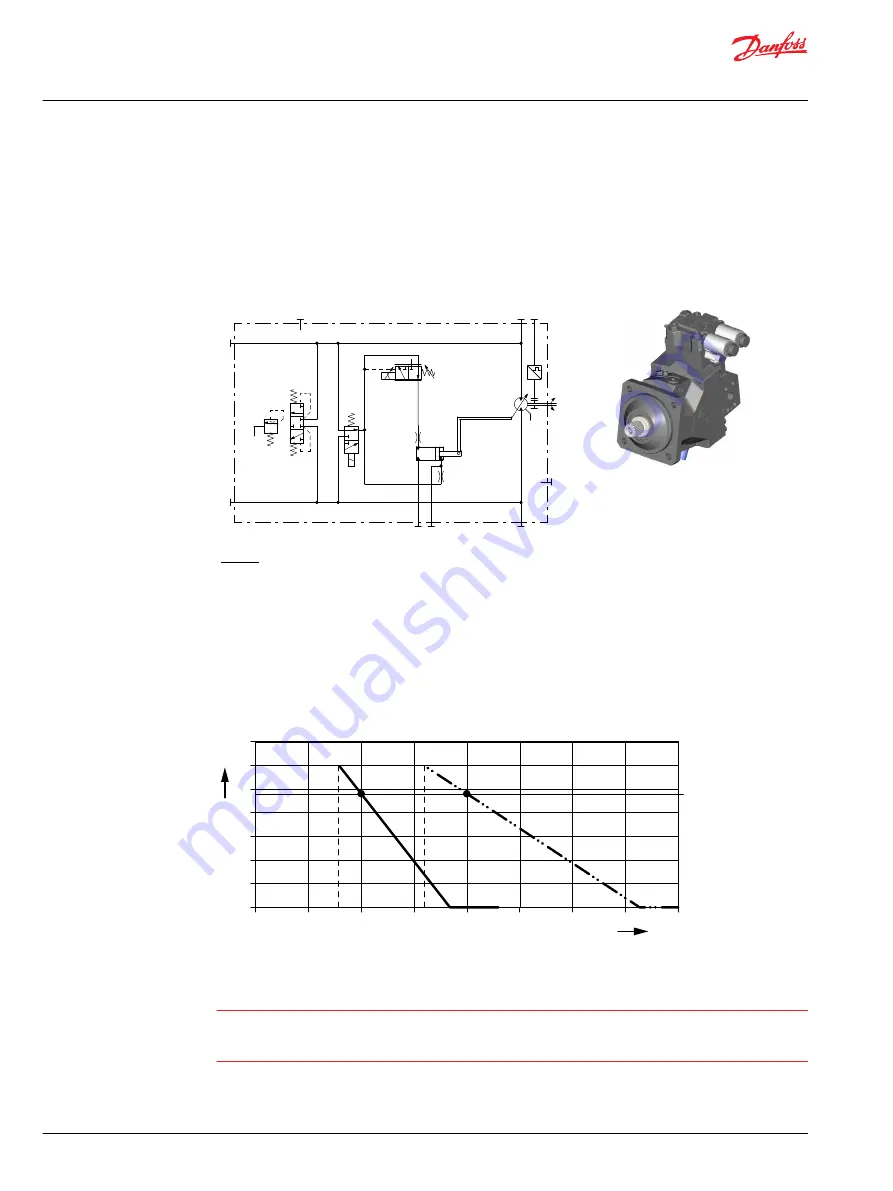
Options P1D1, P2D2 – electric two-position control with PCOR and electric BPD
P1 – electric prop. 12 V / de-energized = min. displacement with electric prop. PCOR 12 V
D1 – with electric propor. PCOR / with electric BPD 12 V, de-energized BPD = PCOR active at port A
P2 – electric prop. 24 V / de-energized = min. displacement with electric prop. PCOR 24 V
D2 – with electric propor. PCOR / with electric BPD 24 V, de-energized BPD = PCOR active at port A
Hydraulic schematic
A
B
n
min
max
C5
C6
M4
MB
M5
P003436
L1
L1
N
MA
Where:
A, B
Main pressure lines
L1, L2
Drain lines
M4, M5
Gauge port servo pressure
MA, MB
Gauge port system pressure
N
Speed sensor (optional)
Options P1D1, P2D2
Solenoid C6
De-energized = min. displacement
Full-energized = max. displacement
PCOR pressure (bar) versus Input command (mA)
0
50
100
150
200
250
240*
300
350
0
200
400
600
800
1000
1200
1400
1600
P003 485
ba
r
P1
P2
mA
Maximum PCOR setting = 300 bar [4351 psi], * Production test setting = 240 bar
C
Caution
If the signal to the PPCOR is lost or drops below the range shown in the chart, the PCOR setting will
potentially increase to pressure levels above the recommended application limits or the regulated
pressure control of the pump, and in effect, disable the PCOR function.
The PCOR pressure level can be proportionally changed with the input current to the solenoid.
For formulas to calculate pressure level dependent on input current please see
electric two-position control with PCOR
Technical Information
H1 Bent Axis Variable Displacement Motors, Size 060/080/110/160/210/250
Controls – nomenclature, description
64 |
©
Danfoss | December 2016
11037153 | BC00000043en-US1103