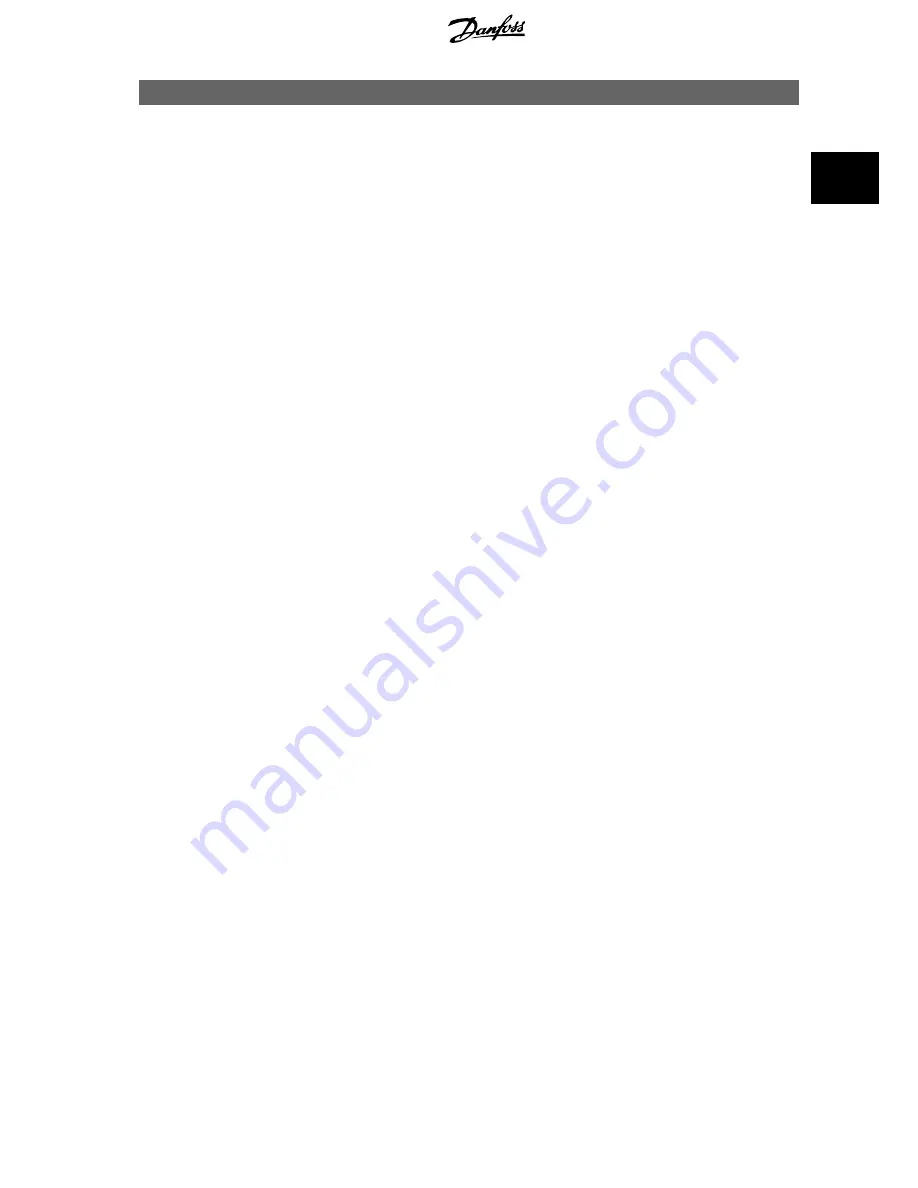
2. Introduction
2.1.1. About this Manual
First time users can obtain the most essential information for quick installation and set-up in these chapters:
Introduction
How to Install
How to Configure the System
For more detailed information including the full range of set-up options and diagnosis tools please refer to the chapters:
How to Control the FC 300
How to Access FC 300 Parameters
Parameters
Troubleshooting
2.2.1. Technical Overview
The Interbus system is divided into two different systems: remote and local.
The remote system enables the user to connect up to 256 stations on a single system with a maximum of 400m cable length between stations.
The local bus system enables the user to establish communication to Input/Output devices through a single twisted pair of Cables. This type of commu-
nication typical uses simple devices, e.g. Digital I/O devices.
The Interbus option described in this manual supports remote bus only. For communication on the remote bus, the Interbus system provides two different
types of communication: Process Data and PCP (Peripherals Communication Protocol). The Process Data is cyclic communication to devices with high
priority.
Examples of this type of communication are digital and analogue I/O or control word and reference to frequency converters.
PCP communication is used for communications which do not require high speed and typically only are activated on request from the user-written program.
Typical time to read/write a single value is 100 to 200 milliseconds. Examples of this type of communication are configuration data, or reading of service
parameters such as running hours, numbers of power ups and kWh.
2.3.1. Assumptions
This manual assumes that you are using a Danfoss Interbus Option in conjunction with a Danfoss FC 300 Automation Drive. It is also assumed that your
master is a PLC or PC that is equipped with a serial communication card supporting all the Interbus communication services required by your application,
and that all requirements stipulated in the Interbus standard as well as those set up in the Drivecom frequency converter Profile and its company-specific
implementation, as well as those pertaining to the VLT frequency converter are strictly observed as well as all limitations therein fully respected.
2.4.1. Hardware
This manual relates to the Interbus option type no. 130B1211.
2.5.1. Background Knowledge
The Danfoss Interbus Option is designed to communicate with any master abiding by the Interbus standard. It is therefore assumed that you have full
knowledge of the PC or PLC you intend to use as a master in your system. Any questions pertaining to hardware or software produced by any other
manufacturer are beyond the scope of this manual and are of no concern to Danfoss.
If you have questions about how to set up master-to-master communication or communication to a non-Danfoss slave, please consult the appropriate
manuals.
FC 300 Interbus Operating Instructions
2. Introduction
MG.33.H3.02 - VLT is a registered Danfoss trademark
5
2