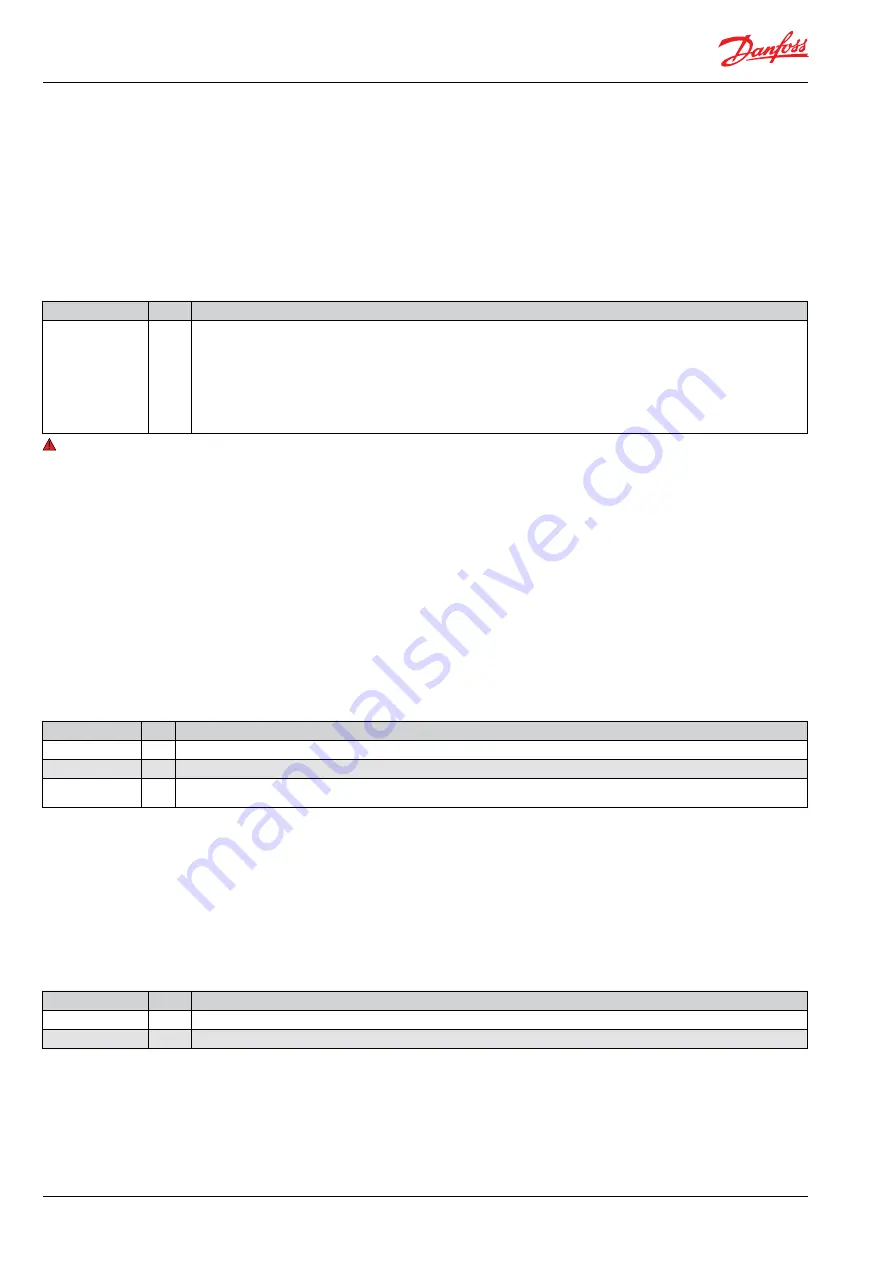
8
DKRCC.PS.RQ0.B7.02 /520H8832
© Danfoss A/S (AC-MCI / sw), 2014-11
Manual
Superheat Controller EIM 336
Operation
1.
Selecting a refrigerant
The controller needs to know which refrigerant is used in order to
accurately control the superheat. This can be selected by setting
the “o30 Refrigerant” to the desired refrigerant as defined in the list
below.
If no refrigerant is selected (“o30 Refrigerant” is set to 0 or an
undefined refrigerant), the “No Rfg. Sel.” alarm is set and the
controller will not start regulating.
Refrigerant setting
Before refrigeration can be started , the refrirant has to be defined.
You can select the following refrigerant.
Related parameters:
Symbolic name
PNU
Description
o30 Refrigerant
2551
1 = R12
2 = R22
3 = R134a
4 = R502
5 = R717
6 = R13
7 = R13b1
8 = R23
9 = R500
10 = R503
11 = R114
12 = R142b
13 = User defined
14 = R32
15 = R227
16 = R401A
17 = R507
18 = R402A
19 = R404A
20 = R407C
21 = R407A
22 = R407B
23 = R410A
24 = R170
25 = R290
26 = R600
27 = R600a
28 = R744
29 = R1270
30 = R417A
31 = R422A
32=R413A
33=R422D
34=427A
35=R438A
R36=Opteon
XP10
37 =R407F
Warning: Wrong selection of refrigerant may caurse damage to the compressor.
2.
Connecting and setting up a valve
The EIM 336 controller is designed to be used with Danfoss
ETS 6 valves with a maximum of 480 pulses from fully closed to
fully open. This setting should not be changed.
The speed of the valve can be changed by increasing or
decreasing the number of pulses per second, “n38 Max StepsSec”.
A larger value will make the value open or close faster. Note that
the torque of a stepper motor decreases as the speed increases.
Too high speeds should therefore be avoided. For the ETS 6 valve,
the recommended speed setting is 31 pulses per second.
When the controller is powered, the valve will first be closed
fully so that the controller starts from a known opening degree
(0%). In order to make sure that it is fully closed, the valve will be
closed 100% plus an additional contribution known as backlash.
The backlash takes into account that the stepper motor may
loose some steps due to too low torque or mechanical slippage
in the gears etc. The start backlash is the amount of extra steps in
percent to close once the valve is closed (less than 1%). If the valve
is opening and reaches its destination, it will move additional steps
in the opening direction, then move the same amount of steps in
the closing direction. This is called backlash and is the amount of
steps to add to compensate for spindle play.
Related parameters:
Symbolic name
PNU Description
n38 Max StepsSec 3033 Steps per second
n39 Start BckLsh
3034 Backlash, is the additional amount of steps, in percent, to close at startup and when the valve opening degree is less than 1%.
n40 Backlash
3035 Start Backlash is the amount of steps to compensate for spindle play
3.
Connecting and setting up a pressure sensor
The pressure sensor input is setup by default to accept an AKS32R
pressure transducer. If another sensor is to be used, it is important
to note that it needs to be a 0.5 - 4.5 V d.c. ratiometric type (10% -
90% of supply voltage).
The default range for the sensor is 0 to 16 bar absolute. Thi s
can be changed by setting the minimum transducer pressure,
“o20 MinTransPres” and the maximum transducer pressure, “o21
MaxTransPres” to the new values. The values must be entered in
bar absolute so a sensor with a range of -1 to 12 bar gauge, needs
to be entered as 0 to 13 bar absolute.
Related parameters:
Symbolic name
PNU
Description
o20 MinTransPres
2034
Minimum transducer pressure (in bar absolute x 10)
o21 MaxTransPres
2033
Maximum transducer pressure (in bar absolute x 10)