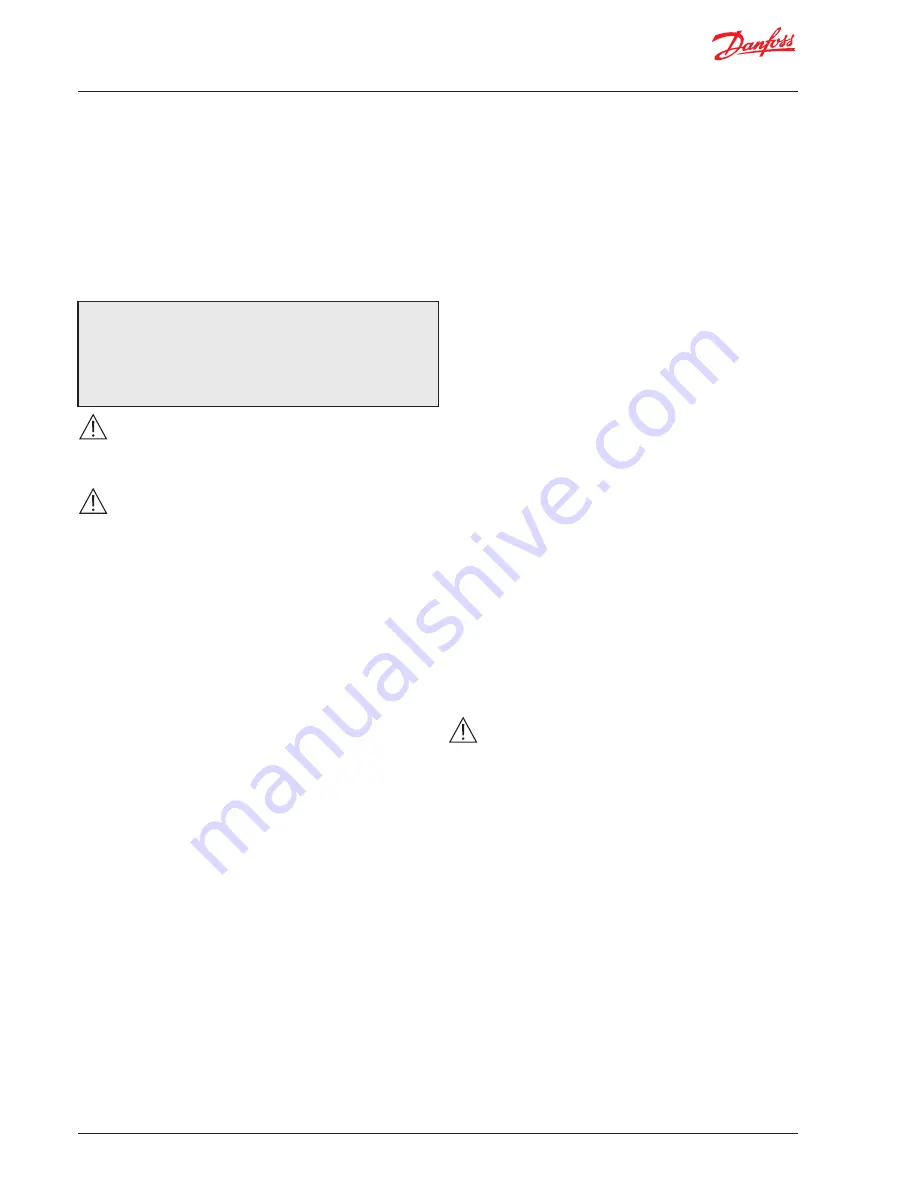
Installation and Operation Guide | DGS Modbus
© Danfoss | ADAP-KOOL® | 2016.12
14 | RS8HJ102 |
6. Functional Tests and Calibration
6.1 Introduction
To comply with the requirements of EN378 and the European
F-GAS regulation, sensors must be tested annually. However, local
regulations may specify the nature and frequency of this test.
NOTE: The DGS Modbus is calibrated at the factory.
After installation, a zero adjustment may be required to
DGS-SC due to differences in environmental conditions.
DGS-IR should never need any adjustment after instal-
lation.
CAUTION
: Check local regulations on calibration or testing re-
quirements.
CAUTION
: The DGS Modbus contains sensitive electronic compo-
nents that can be easily damaged. Do not touch nor disturb any of
these components while lid is removed and when replacing it.
IMPORTANT
: If the DGS-SC is exposed to a large leak it should be
tested to ensure correct functionality by electrically resetting the
zero setting and carrying out a bump test. See procedures below.
This does not apply to DGS-IR.
IMPORTANT
: Danfoss recommends annual checks and gas
calibration. Danfoss also recommends sensor replacement every
3 years or as required. Calibration frequency may be extended
based on application, but should never exceed 2 years.
IMPORTANT
: In applications where life safety is critical, calibration
should be done quarterly (every 3 months) or on a more frequent
basis. Danfoss is not responsible for setting safety practices and
policies. Safe work procedures including calibration policies are
best determined by company policy, industry standards, and local
codes.
IMPORTANT
: Failure to test or calibrate the unit in accordance
with applicable instructions and with industry guidelines may
result in serious injury or death. The manufacturer is not liable for
any loss, injury, or damage arising from improper testing, incorrect
calibration, or inappropriate use of the unit.
IMPORTANT
: Before testing the sensors on-site, the DGS Modbus
must have been powered up and allowed to stabilise. See section
5.
IMPORTANT
: The testing and/or calibration of the unit must be
carried out by a suitably qualified technician, and must be done:
• in accordance with this manual
• in compliance with locally applicable guidelines and regulations.
Suitably qualified operators of the unit should be aware of the
regulations and standards set down by the industry/country for
the testing or calibration of this unit. This manual is only intended
as a guide and, insofar as permitted by law, the manufacturer ac-
cepts no responsibility for the calibration, testing, or operation of
this unit.
The frequency and nature of testing or calibration may be deter-
mined by local regulation or standards.
EN378 and the F-GAS Regulation require an annual check in ac-
cordance with the manufacturer’s recommendation.
There are two concepts that need to be differentiated:
• bump test
• calibration.
Bump Test:
Exposing the sensor to a gas and observing its response to the
gas. The objective is to establish if the sensor is reacting to the gas
and all the sensor outputs are working correctly. There are two
types of bump test.
Quantified:
A known concentration of gas is used.
Non-Quantified:
A gas of unknown concentration is used.
Calibration:
Exposing the sensor to a calibration gas, setting the “zero” or
standby voltage to the span/range, and checking/adjusting all
the outputs, to ensure that they are activated at the specified gas
concentration.
CAUTION
: Before you carry out the test or calibration:
• Advise occupants, plant operators, and supervisors.
• Check if the DGS Modbus is connected to external systems
such as sprinkler systems, plant shut down, external sirens and
beacons, ventilation, etc. and disconnect as instructed by the
customer.
• Deactivate alarm delays if selected at JP5, JP6 as per Figure 1 or
via Modbus. See section 7.
• For bump test or calibration the DGS Modbus should be pow-
ered up overnight. The instrument should be fully stabilised per
Section 5.