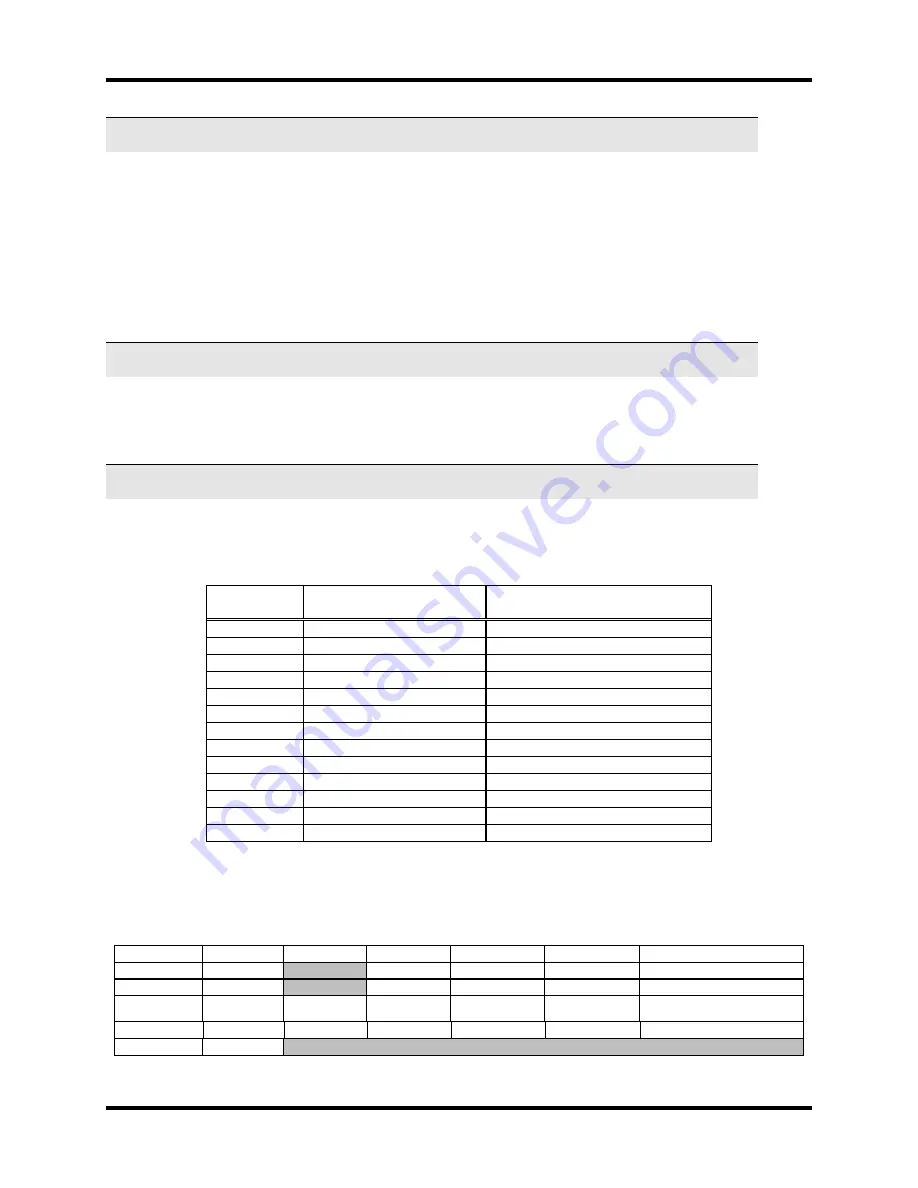
Kollmorgen Troubleshooting
SERVO
STAR
®
SP3 Power Block
24
WATCHDOG
In order to prevent the Watchdog fault from being triggered, the following power up sequence
must be used:
1.
Power up the PMAC2 controller
2.
Connect the SP3 to the PMAC2 controller
3.
Turn the 24 VDC power on (for units that are supplied with separate 24V logic power)
4.
Turn the AC power on.
F FAULT (MAXIMUM PWM FREQUENCY)
In order to prevent the Frequency Fault, the PMAC2 I900 parameter should be set such that the
PWM frequency does not exceed 15.5kHz.
FAULT CODE TRANSMISSION
The SP3 transmits FC_A, FC_B, FC_C and FC_D fault code bits to the PMAC2 controller via
lines CHU+, CHV+, CHW+ and CHT+ on connector C3. The following table shows the fault
codes and fault description.
Display PMAC
Code
(FCA-FCB-FCC-FCD)
Fault Description
t1 1011
Over-current
shut-down
t2 1011
Motor
over-temperature
t3
1011
Power amplifier over-temperature
o
1101
Power amplifier over-voltage
u
1110
Power amplifier under-voltage
≡
Watch
dog
P1 1001
Drive
over-current
P
1001
Power amplifier over-current
F
1100
PWM fault frequency
A1 1010
+12V
under-voltage
A2 1010
-12V
under-voltage
A3 1010
+5V
under-voltage
A4 1010
Reference
under-voltage
DIP switches 9 and 10 determine the signals transmitted to the PMAC2 on CHU+, CHV+,
CHW+ and CHT+. These signal lines can carry either the Hall Effect sensor values or fault
codes. CHU+, CHV+, CHW+, and CHT+ correspond to FC_A, FC_B, FC_C, and FC_D when
faults are annunciated through the signal lines. The settings are shown in the following table.
Switch 9
Switch 10
Status
CHU+
CHV+
CHW+
CHT+
Open Open
Hall A
Hall B
Hall C
Motor Over Temp
Closed Closed
FC_A FC_B FC_C
FC_D
Open Closed
No Faults
Hall A
Hall B
Hall C
Motor Over Temp
Faults
FC_A
FC_B
FC_C
FC_D
Closed Open
Not Used
www.szcxi.com | From
:
KOLLMORGEN