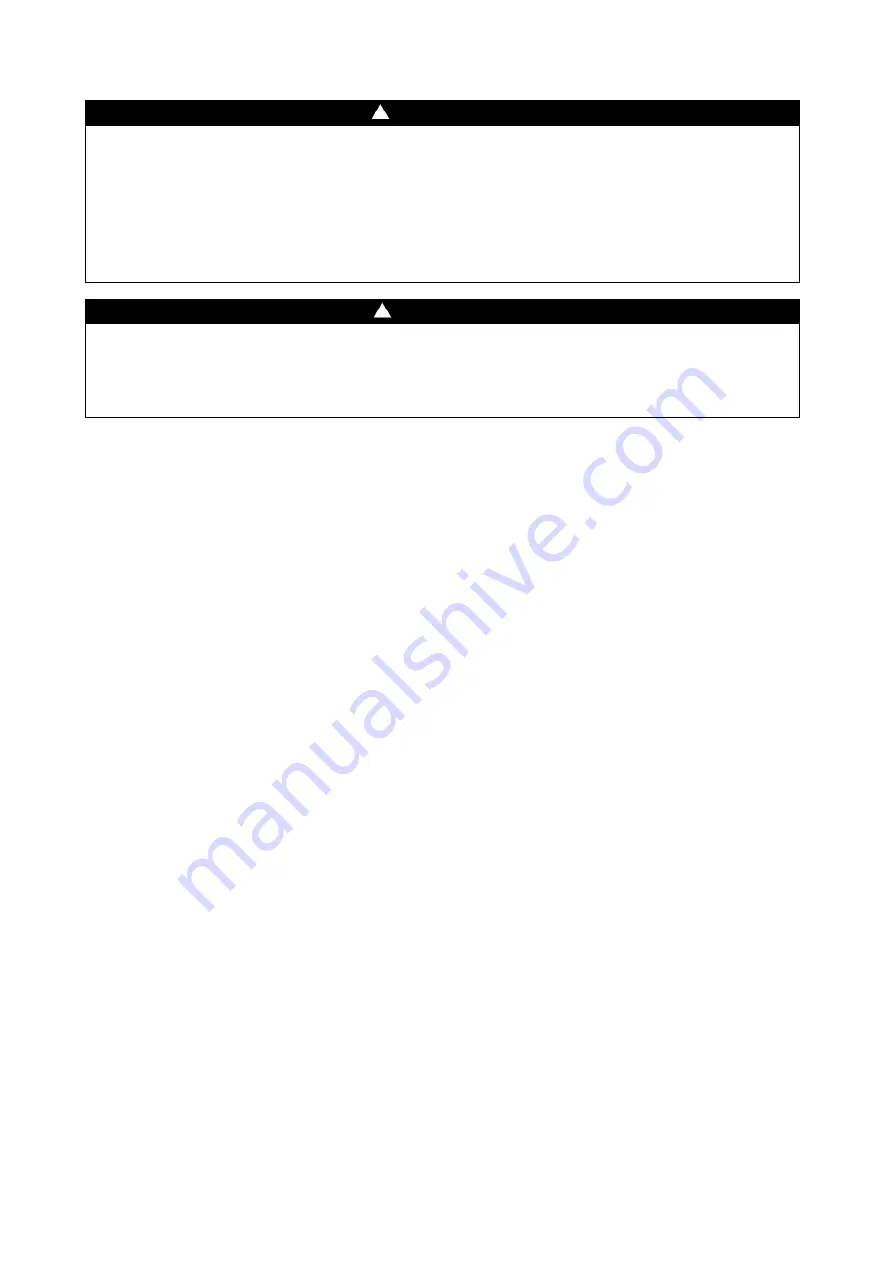
D
–EIMWC00408-16EN - 49/60
ATTENTION
The lubrication system has been designed to keep most of the oil charge inside the compressor. During operation,
however, a small amount of oil circulates freely in the system, conveyed by the refrigerant. The amount of
replacement oil going into the compressor should therefore be equal to the quantity removed rather than the amount
stated on the nameplate; this will avoid excess of oil during the following start-up.
The quantity of oil removed from the compressor must be measured after having allowed the refrigerant present in the
oil to evaporate for a suitable amount of time. To reduce the refrigerant content in the oil to a minimum, it is advised
that the electrical resistances be kept on and that the oil be removed only when it has reached a temperature of
35
45°C.
ATTENTION
The replacement of the oil filter requires careful attention with regard to oil recovering; the oil must not be exposed to
air for more than about 30 minutes.
In case of doubts, verify oil acidity or, if it is not possible to carry out the measurement, replace the charge of lubricant
with fresh oil stored in sealed tanks or in a way that meet supplier specifications.
Fr4200 compressor
The compressor oil filter is located at the coupling of the oil inlet piping and the compressor body (suction side). It is
strongly advised that it be replaced when its pressure drop exceeds 2.0 bar. The pressure drop across the oil filter is the
difference between the compressor delivery pressure minus oil pressure. Both pressures can be controlled through the
microprocessor for both compressors.
Required materials:
Oil filter Code 95816-401
– Quantity 1
Gaskets kit Code 128810988
– Quantity 1
Compatible oils:
DAPHNE HERMET OIL FVC68D
The standard oil charge for a compressor is18 litres.
Oil filter replacement procedure
Procedure to replace oil filter
1)
Shut down both compressors by turning the Q1 and Q2 switches to the Off position.
2)
Turn the Q0 switch to Off, wait for the circulation pump to turn off and open the general disconnecting switch
Q10 to cut off the machine’s electrical power supply.
3)
Place a label on the handle of the general disconnecting switch in order to prevent accidental start-up.
4)
Close the suction, discharge and liquid injection valves.
5)
Connect the recovery unit to the compressor and recover the refrigerant in a suitable and clean container.
6)
Evacuate the refrigerant until the internal pressure has turned negative (compared to atmospheric pressure).
The amount of refrigerant dissolved in the oil is reduced to a minimum in this way.
7)
Drain the oil in the compressor by opening the drain valve located under the oil separator.
8)
Remove the oil filter cover and remove the internal filter element.
9)
Replace the cover and internal sleeve gaskets. Do not lubricate the gaskets with mineral oil in order not to
contaminate the system.
10)
Insert the new filter element.
11)
Reposition the filter cover and tighten the screws. The screws must be tightened alternately and progressively
setting the torque wrench at 60 Nm.
12)
Charge the oil from the upper valve located on the oil separator. Considering the high hygroscopy of ester oil, it
should be charged as quickly as possible. Do not expose ester oil to the atmosphere for more than 10 minutes.
13)
Close the oil charging valve.
14)
Connect the vacuum pump and evacuate the compressor up to a vacuum of 230 Pa.
15)
On reaching the above vacuum level, close the vacuum pump valve.
16)
Open the system’s delivery, suction and liquid injection valves.
17)
Disconnect the vacuum pump from the compressor.
18)
Remove the warning label from to the general disconnecting switch.
19)
Close the general disconnecting switch Q10 to supply power to the machine.
20)
Start the machine by following the start-up procedure described above.