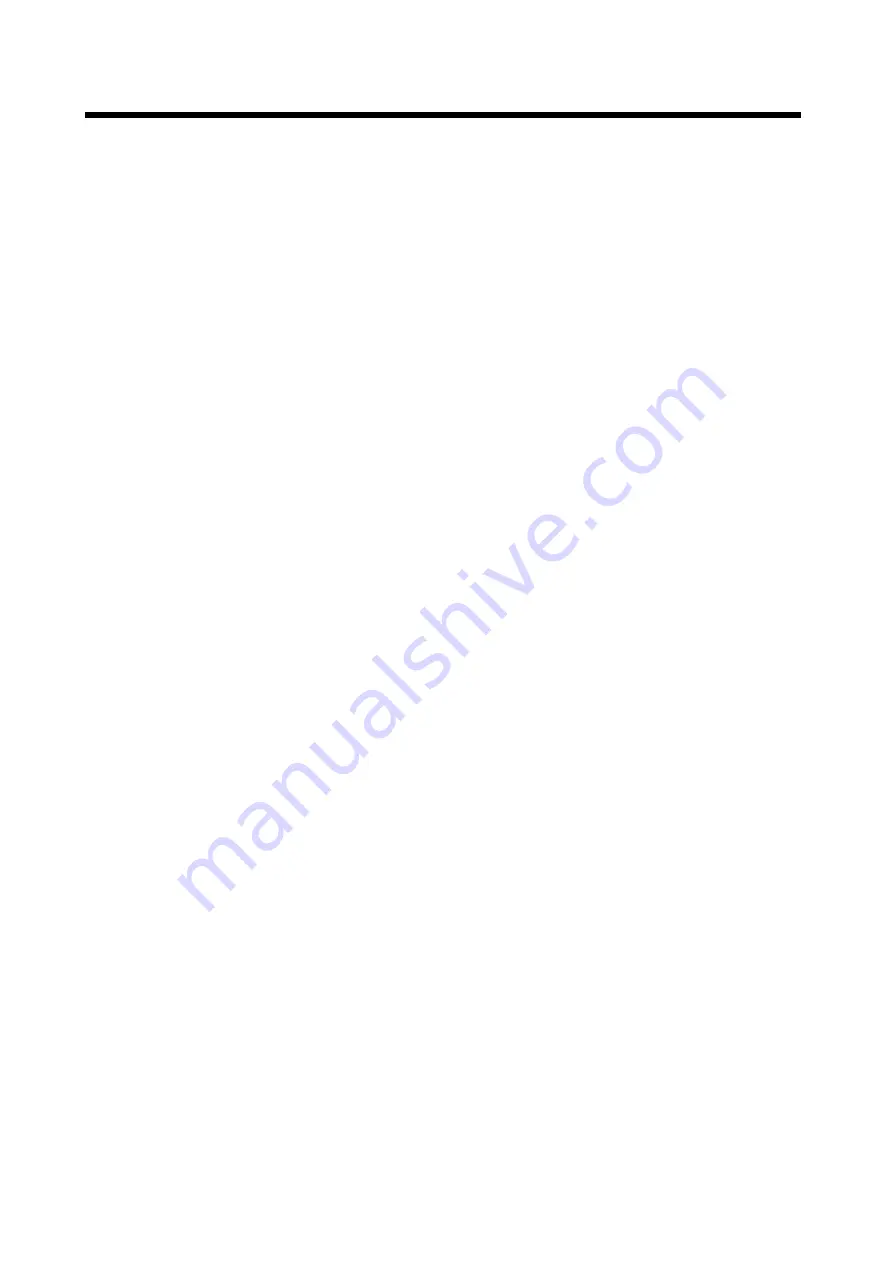
D
–EIMWC00408-16EN - 22/60
Operation
Op
erator’s responsibilities
It is important that the operator is appropriately trained and becomes familiar with the system before operating the
machine. In addition to reading this manual, the operator must study the microprocessor operating manual and the wiring
diagram in order to understand start-up sequence, operation, shutdown sequence and operation of all the safety devices.
During the machine’s initial start-up phase, a technician authorized by the manufacturer is available to answer any
questions and to give instructions as to the correct operating procedures.
The operator is advised to keep a record of operating data for every installed machine. Another record should also be
kept of all the periodical maintenance and servicing activities.
If the operator notes abnormal or unusual operating conditions, he is advised to consult the technical service authorized
by the manufacturer.
Description of the machine
This machine, of the water condensation type, is made up of the following main components:
-
Compressor
:
The single-screw compressor of the Fr 3200 or Fr4100 series is of the semi-hermetic
type and utilises gas from the evaporator to cool the motor and allow optimal operation
under any expected load conditions. The oil-injection lubrication system does not require
an oil pump as oil flow is ensured by the pressure difference between delivery and
suction. In addition to ensuring lubrication of ball bearings, oil injection dynamically seals
the screw, thus enabling the compression process.
-
Evaporator
:
The direct-expansion shell and tube type evaporator is of ample size in order to ensure
optimum efficiency under all load conditions.
-
Condenser
:
The shell and tube type condenser has external high efficiency micro fins.
The liquid subcooled by the lower part of the tubes not only improves overall efficiency of
the machine but also compensates variations in heat load by adapting the refrigerant
load to all foreseen operating conditions.
-
Expansion valve
:
The machine has a an electronic expansion valve, which is controlled by an electronic
device called a Driver that optimises its operation.
Description of the refrigeration cycle
The low-temperature refrigerant gas from the evaporator is drawn by the compressor through the electric motor, which is
cooled by the refrigerant. It is subsequently compressed and during this process the refrigerant mixes with the oil from
the oil separator.
The high-pressure oil-refrigerant mixture is introduced into the centrifuge-type high-efficiency oil separator, where the oil
is separated from the refrigerant. The oil accumulated on the bottom of the separator is forced by the pressure difference
back into the compressor while the oil-free refrigerant is sent to the condenser.
The refrigerant fluid is evenly distributed inside the condenser throughout the volume of the exchanger, and the gas in
contact with the tubes is cooled and successively starts to condense.
The condensed fluid at saturation temperature passes through the subcooling section where it looses even more heat,
increasing the efficiency of the cycle. The heat taken from the fluid during cooling, condensation and subcooling is
exchanged with that of the water passing inside the condenser tubes.
The subcooled fluid flows through the high-efficiency filter dryer and then reaches the expansion element (expansion
valve) through which a fall in pressure starts off the expansion process resulting in the vaporisation of part of the
refrigerant liquid.
The result at this point is a low-pressure and low-temperature liquid-gas mixture entering the evaporator, where it takes
the heat required for vaporisation.
When the refrigerant liquid-vapour is uniformly distributed in the direct expansion evaporator tubes, heat is exchanged
with the cooling water, thus reducing the temperature until complete evaporation, followed by superheating.
Once it has reached the superheated-vapour state, the refrigerant leaves the evaporator and is once again taken into the
compressor to repeat the cycle.
Description of the refrigeration cycle with partial heat recovery
The low-temperature refrigerant gas from the evaporator is drawn by the compressor through the electric motor, which is
cooled by the refrigerant. It is subsequently compressed and during this process the refrigerant mixes with the oil from
the oil separator.
The high-pressure oil-refrigerant mixture is introduced into the centrifuge-type high-efficiency oil separator, where the oil
is separated from the refrigerant. The oil accumulated on the bottom of the separator is forced by the pressure difference
back into the compressor while the oil-free refrigerant is sent to the condenser.
The upper portion of the condenser has cooling tubes through which about 10% of the heat rejection (mainly discharge
gas superheat) of the unit is recovered.