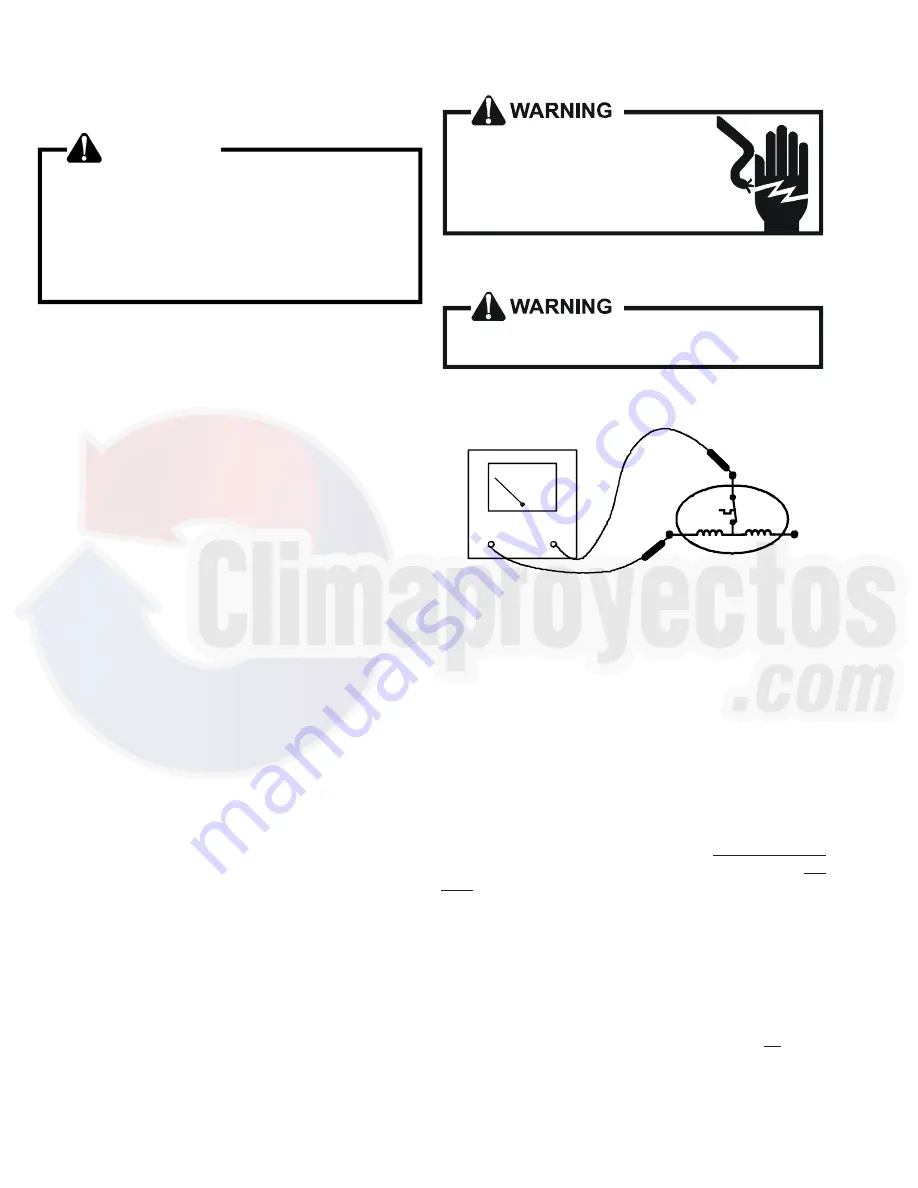
SERVICING
68
S-17 CHECKING COMPRESSOR
WARNING
Hermetic compressor electrical terminal venting can
be dangerous. When insulating material which
supports a hermetic compressor or electrical terminal
suddenly disintegrates due to physical abuse or as a
result of an electrical short between the terminal and
the compressor housing, the terminal may be
expelled, venting the vapor and liquid contents of the
compressor housing and system.
If the compressor terminal PROTECTIVE COVER and
gasket (if required) are not properly in place and secured,
there is a remote possibility if a terminal vents, that the
vaporous and liquid discharge can be ignited, spouting
flames several feet, causing potentially severe or fatal
injury to anyone in its path.
This discharge can be ignited external to the compressor
if the terminal cover is not properly in place and if the
discharge impinges on a sufficient heat source.
Ignition of the discharge can also occur at the venting
terminal or inside the compressor, if there is sufficient
contaminant air present in the system and an electrical
arc occurs as the terminal vents.
Ignition cannot occur at the venting terminal without the
presence of contaminant air, and cannot occur externally
from the venting terminal without the presence of an
external ignition source.
Therefore, proper evacuation of a hermetic system is
essential at the time of manufacture and during servicing.
To reduce the possibility of external ignition, all open
flame, electrical power, and other heat sources should be
extinguished or turned off prior to servicing a system.
If the following test indicates shorted, grounded or open
windings, see procedures S-19 for the next steps to be
taken.
S-17A RESISTANCE TEST
Each compressor is equipped with an internal overload.
The line break internal overload senses both motor
amperage and winding temperature. High motor tem-
perature or amperage heats the disc causing it to open,
breaking the common circuit within the compressor on
single phase units.
Heat generated within the compressor shell, usually due
to recycling of the motor, high amperage or insufficient
gas to cool the motor, is slow to dissipate. Allow at least
three to four hours for it to cool and reset, then retest.
Fuse, circuit breaker, ground fault protective device, etc.
has not tripped -
HIGH VOLTAGE!
Disconnect ALL power before servicing
or installing. Multiple power sources
may be present. Failure to do so may
cause property damage, personal injury
or death.
1. Remove the leads from the compressor terminals.
See warnings S-17 before removing compressor
terminal cover.
2. Using an ohmmeter, test continuity between terminals S-
R, C-R, and C-S, on single phase units.
S
R
C
COMP
OHMMETER
TESTING COMPRESSOR WINDINGS
If either winding does not test continuous, replace the
compressor.
NOTE:
If an open compressor is indicated, allow ample time
for the internal overload to reset before replacing compressor.
S-17B GROUND TEST
If fuse, circuit breaker, ground fault protective device, etc.,
has tripped, this is a strong indication that an electrical
problem exists and must be found and corrected. The circuit
protective device rating must be checked, and its maximum
rating should coincide with that marked on the equipment
nameplate.
With the terminal protective cover in place, it is acceptable to
replace the fuse or reset the circuit breaker ONE TIME ONLY
to see if it was just a nuisance opening. If it opens again, DO
NOT continue to reset.
A Meghometer should not be used to determine good or bad
compressors. There is not an industry recognized specifica-
tion for mega ohm values for small tonnage compressors.
Scroll compressors can have the motor winding end-turns in
the oil, which can produce a lower resistance reading to
ground. The insulation type is the same for scroll and
reciprocating compressors.
Disconnect all power to unit
, making sure that
all
power
legs are open.