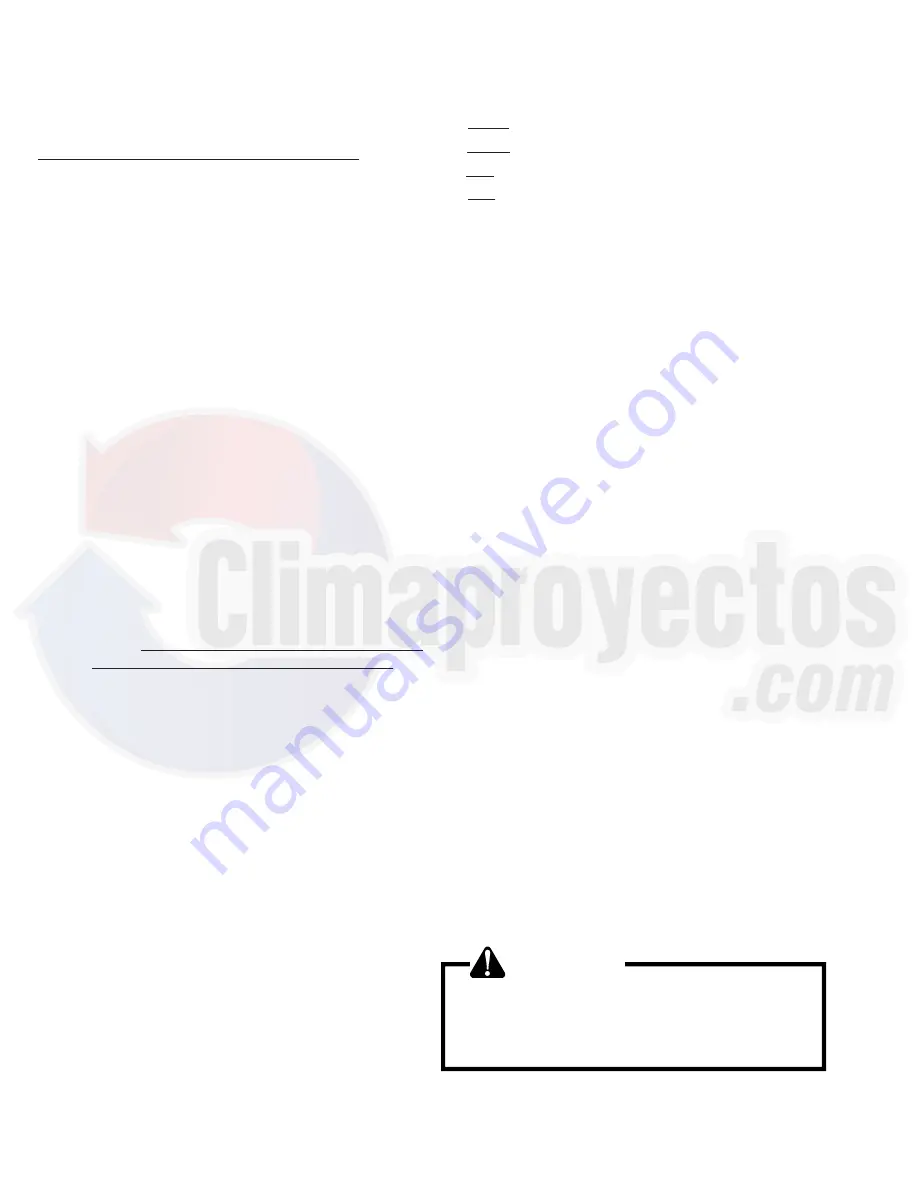
SERVICING
80
Units Equipped with Adjustable Expansion
Valves should be charged by Subcooling and
Superheat adjusted only if necessary.
1. Purge gauge lines. Connect service gauge manifold to
base-valve service ports. Run the system in low stage at least
10 minutes to allow pressure to stabilize.
2. Temporarily install a thermometer on the liquid line at the
liquid line service valve and 4-6" from the compressor on the
suction line. Ensure the thermometer makes adequate con-
tact and is insulated for best possible readings. Use liquid line
temperature to determine subcooling and vapor temperature
to determine superheat.
3. Check subcooling and superheat. Systems with TXV
application should have a subcooling of 5 to 7°F and super-
heat of 7 to 9 °F.
a. If subcooling and superheat are low, adjust TXV to 7 to 9
ºF superheat, and then check subcooling.
NOTE:
To adjust superheat, turn the valve stem clockwise to
increase and counter clockwise to decrease.
b. If subcooling is low and superheat is high, add charge
to raise subcooling to 5 to 7 °F then check superheat.
c. If subcooling and superheat are high, adjust TXV valve
to 7 to 9 ºF superheat, then check subcooling.
d. If subcooling is high and superheat is low, adjust TXV
valve to 7 to 9 ºF superheat and remove charge to lower
the subcooling to 5 to 7 ºF.
NOTE:
Do NOT adjust the charge based on suction
pressure unless there is a gross undercharge.
4. Disconnect manifold set, installation is complete.
SUBCOOLING FORMULA = SATURATED LIQUID
TEMP. - LIQUID LINE TEMP.
NOTE
: Check the Schrader ports for leaks and
tighten valve cores if necessary. Install caps finger-
tight.
HEAT PUMP - HEATING CYCLE
The proper method of charging a heat pump in the heat mode
is by weight with the additional charge adjustments for line
size, line length, and other system components. For best
results on outdoor units with TXVs, superheat should be 2-
5°F at 4-6" from the compressor. Make final charge adjust-
ments in the cooling cycle
S-104 CHECKING COMPRESSOR EFFICIENCY
The reason for compressor inefficiency is broken or damaged
scroll flanks on Scroll compressors, reducing the ability of the
compressor to pump refrigerant vapor.
The condition of the scroll flanks is checked in the following
manner.
1. Attach gauges to the high and low side of the system.
2. Start the system and run a "Cooling Performance Test.
If the test shows:
a. Below normal high side pressure.
b. Above normal low side pressure.
c. Low temperature difference across coil.
d. Low amp draw at compressor.
And the charge is correct. The compressor is faulty - replace
the compressor.
S-106 OVERFEEDING
Overfeeding by the expansion valve results in high suction
pressure, cold suction line, and possible liquid slugging of the
compressor.
If these symptoms are observed:
1. Check for an overcharged unit by referring to the cooling
performance charts in the servicing section.
2. Check the operation of the power element in the valve as
explained in S-110 Checking Expansion Valve Operation.
3. Check for restricted or plugged equalizer tube.
S-107 UNDERFEEDING
Underfeeding by the expansion valve results in low system
capacity and low suction pressures.
If these symptoms are observed:
1. Check for a restricted liquid line or drier. A restriction will
be indicated by a temperature drop across the drier.
2. Check the operation of the power element of the valve as
described in S-110 Checking Expansion Valve Operation.
S-108 SUPERHEAT
The expansion valves are factory adjusted to maintain 7 to 9
degrees superheat of the suction gas. Before checking the
superheat or replacing the valve, perform all the procedures
outlined under Air Flow, Refrigerant Charge, Expansion Valve
- Overfeeding, Underfeeding. These are the most common
causes for evaporator malfunction.
CHECKING SUPERHEAT
Refrigerant gas is considered superheated when its tempera-
ture is higher than the saturation temperature corresponding
to its pressure. The degree of superheat equals the degrees
of temperature increase above the saturation temperature at
existing pressure. See Temperature - Pressure Chart on
following pages.
CAUTION
To prevent personal injury, carefully connect and
disconnect manifold gauge hoses. Escaping liquid
refrigerant can cause burns. Do not vent refrigerant
to atmosphere. Recover during system repair
or final unit disposal.
1. Run system at least 10 minutes to allow pressure to
stabilize.