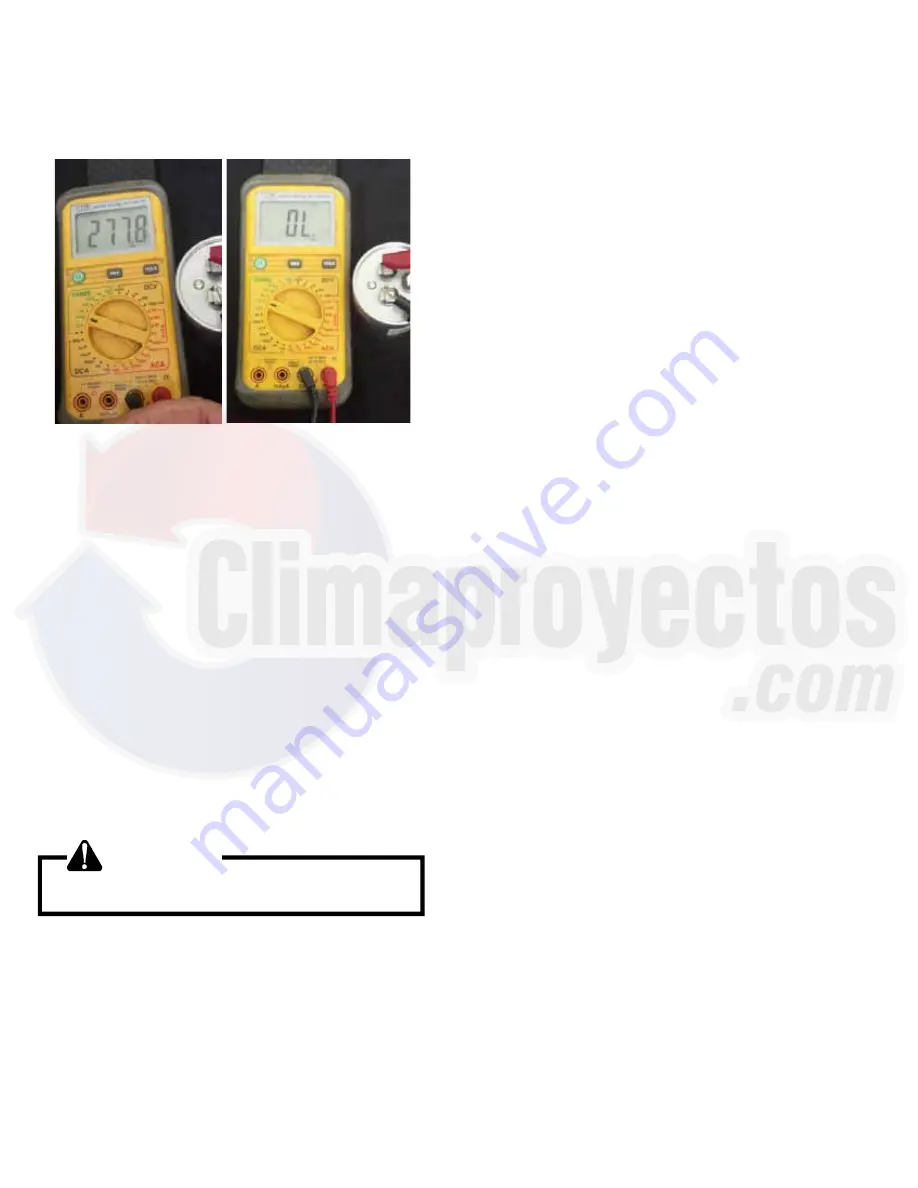
SERVICING
60
3. Digital meter will show a reading momentarily (Figure 1).
Note the reading.
Figure 1
Figure 2
4. Reading will immediately return to the OL = (Open Line)
(Figure 2). Every attempt of Step 2 will show the same
result as was in step 4 and Step 5. This indicates that the
capacitor is good.
5. If there is no Change, then capacitor is dead and must be
replaced.
Check for Analog Meter
A. Good Condition - indicator swings to zero and slowly
returns to infinity. (Start capacitor with bleed resistor will
not return to infinity. It will still read the resistance of the
resistor).
B. Shorted - indicator swings to zero and stops there -
replace.
C. Open - no reading - replace. (Start capacitor would
read resistor resistance.)
S-15B CAPACITANCE CHECK USING A DIGITAL
MULTI-METER (IN CAPACITANCE MODE)
WARNING
Discharge capacitor through a 20 to 30 OHM
resistor before handling.
NOTE
:
You can do this test with a multi-meter if you
have a Capacitance meter on your multi-meter.
1. Remove the capacitor from the circuit.
2. Now Select "Capacitance" on your multi-meter.
3. Now connect the capacitor terminals to the multi-meter
leads.
4. If the reading is near to the actual value of the capacitor
(i.e. the printed value on the capacitor). The capacitor
is good. (Note that the reading may be less than the actual
printed value of the capacitor).
5. If you read a significantly lower capacitance or none at
all, then capacitor is dead and must be replaced.
S-16G CHECKING EMERSON ULTRATECH
TM
ECM
MOTORS
DESCRIPTION
The DVPTC and MBVC models utilize an Emerson, 4-wire
variable speed ECM blower motor. The ECM blower motor
provides constant CFM.
The motor is a serially communicating variable speed motor.
Only four wires are required to control the motor: +Vdc,
Common, Receive, and Transmit.
The +Vdc and Common wires provide power to the motor's
low voltage control circuits. Typical supply voltage is 9-15
volts DC.
GENERAL CHECKS/CONSIDERATIONS
1. Check power supply to the air handler or modular blower.
Ensure power supply is within the range specified on
rating plate. See section S-1.
2. Check motor power harness. Ensure wires are continu-
ous and make good contact when seated in the connec-
tors. Repair or replace as needed.
3. Check motor control harness. Ensure wires are continu-
ous and make good contact when seated in the connec-
tors. Repair or replace as needed.
4. Check thermostat and thermostat wiring. Ensure thermo-
stat is providing proper cooling/heating/continuous fan
demands. Repair or replace as needed.
5. Check blower wheel. Confirm wheel is properly seated
on motor shaft. Set screw must be on shaft flat and
torqued to 165 in-lbs minimum. Confirm wheel has no
broken or loose blades. Repair or replace as needed.
6. Ensure motor and wheel turn freely. Check for interfer-
ence between wheel and housing or wheel and motor.
Repair or replace as needed.
7. Check housing for cracks and/or corrosion. Repair or
replace as needed.
8. Check motor mounting bracket. Ensure mouting bracket
is tightly secured to the housing. Ensure bracket is not
cracked or broken.