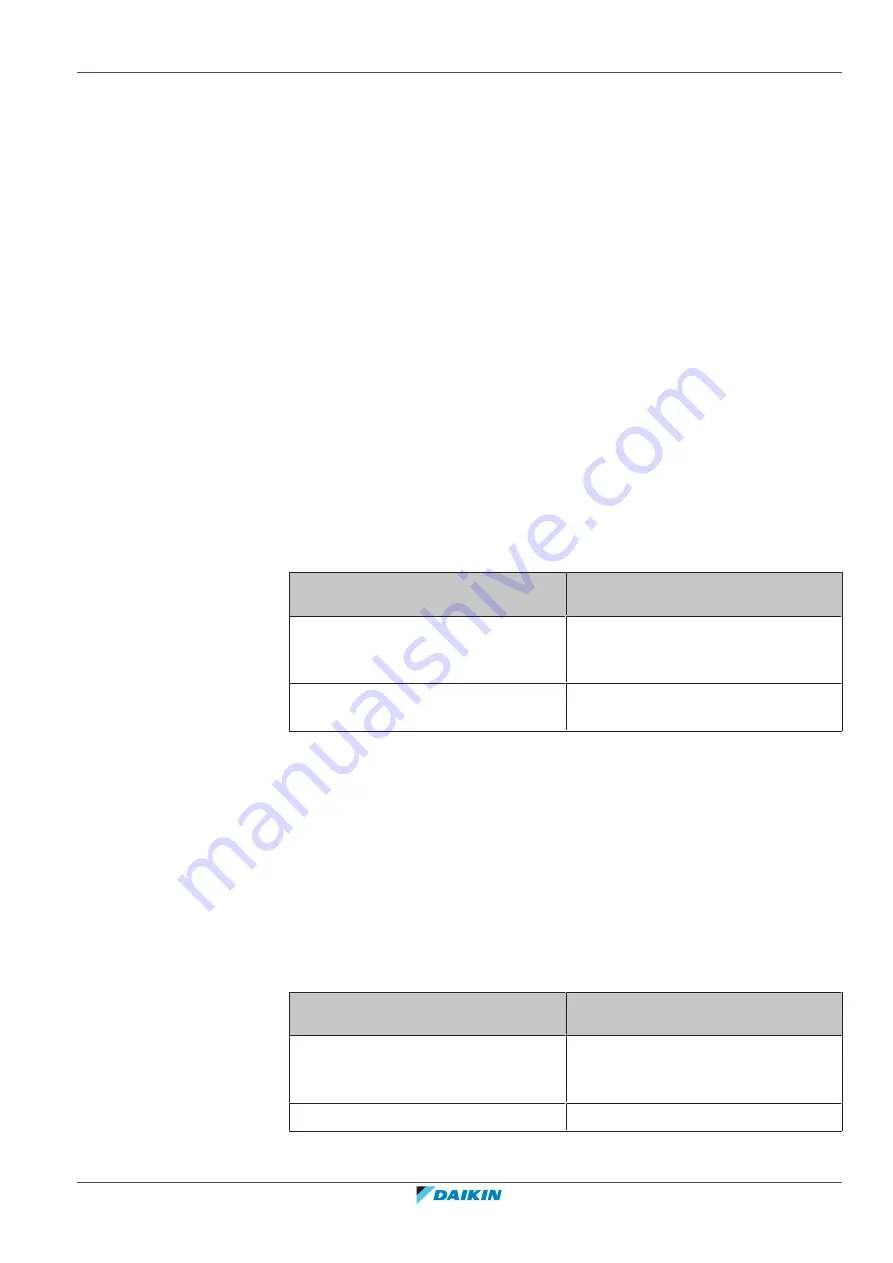
3
|
Third party components
Service manual
127
FTXF20~71A + FTXF20~25B + FTXF20~42C + ATXF20~71A + ATXF20~42C
+ RXF20~71A + RXF20~60B + RXF20~42C + ARXF20~71A + ARXF20~42C
Split Sensira R32
ESIE18-12E – 2021.02
3 Third party components
3.1 Electrical circuit
3.1.1 Checking procedures
To check the power supply of the unit
Prerequisite:
Stop the unit operation via the user interface.
Prerequisite:
Turn OFF the respective circuit breaker.
Prerequisite:
Remove the required plate work, see
1
Check that the power supply cables and earth connection are firmly fixed to
the power supply terminal X1M.
2
Measure the insulation resistance between each power supply terminal and
the ground using a megger device of 500 V DC. All measurements MUST be
>1MΩ. If insulation resistance is <1MΩ, earth leakage is present.
3
Turn ON the power using the respective circuit breaker.
4
Measure the voltage between L and N on the power supply terminal X1M.
Result:
The voltage MUST be 230 V AC ± 10%.
5
Unbalance between the phases MUST NOT exceed 2%.
Is the measured voltage (power supply)
correct?
Action
Yes
Return to the troubleshooting of the
specific error and continue with the
next procedure.
No
Adjust the power supply, see
To check the power supply to the indoor unit
Prerequisite:
Stop the unit operation via the user interface.
Prerequisite:
Turn OFF the respective circuit breaker.
1
Remove the required plate work, see
2
Check that the power supply cables and earth connection are firmly fixed to
the indoor unit power supply terminal X1M.
3
Turn ON the power using the respective circuit breaker.
4
Measure the voltage between L and N on the indoor unit power supply
terminal X1M.
Result:
The voltage MUST be 230 V AC ± 10%.
Is the measured voltage (power supply)
correct?
Action
Yes
Return to the troubleshooting of the
specific error and continue with the
next procedure.
No
Continue with the next step.
5
Check the power supply to the unit, see
127].
Содержание ARXF A Series
Страница 169: ......
Страница 170: ......
Страница 171: ......
Страница 172: ...ESIE18 12E 2021 02 Copyright 2018 Daikin Verantwortung für Energie und Umwelt ...