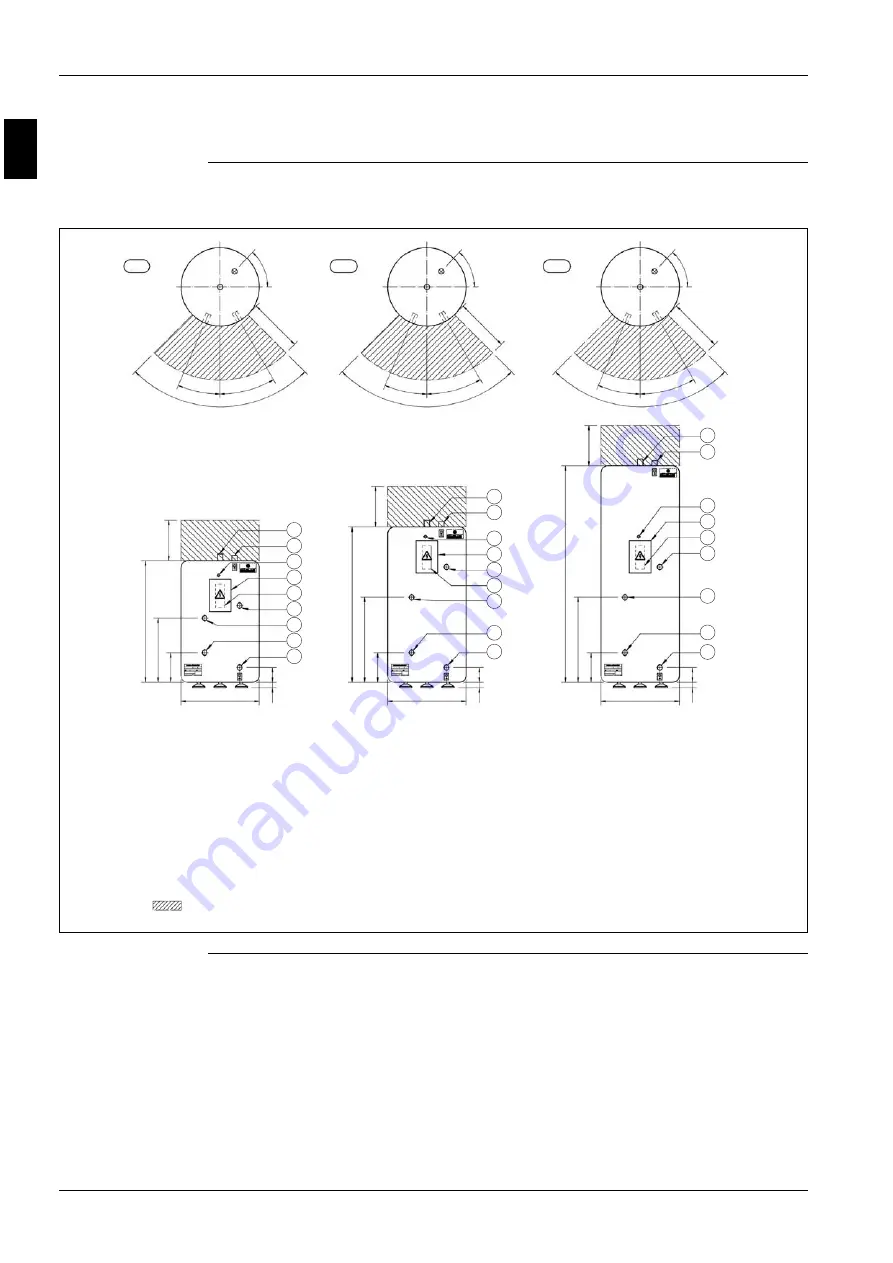
General Outline: Altherma
ESIE06-03
1–10
3
11
4
5
1.5
EKSWW150~300V3: Outlook and Dimensions - Service Space
Outlook and
dimensions -
Service space
The illustration below shows the outlook and the dimensions of the unit (mm).
580
0-40
1
1
0
220
475
300
900
580
0-40
1
1
0
220
630
300
11
5
0
580
0-40
1
1
0
220
630
300
1600
23°
90°
30°
23°
90°
30°
23°
90°
30°
47°
400
47°
400
47°
400
150 L
200 L
300 L
8
2
8
8
2
9
6
7
3
4
5
1
2
9
6
3
7
4
5
1
9
6
7
3
4
5
1
Required service space
around the tank
Содержание Altherma EKHBH Series
Страница 2: ...ESIE06 03 1 2 Part 1 System Outline 3 1 1 5 ...
Страница 26: ...Functional Diagrams ESIE06 03 1 26 Part 1 System Outline 3 1 1 4 5 ...
Страница 32: ...Piping Diagrams ESIE06 03 1 32 Part 1 System Outline 3 1 1 4 5 ...
Страница 38: ...Switch Box Layout ESIE06 03 1 38 Part 1 System Outline 3 1 1 4 5 ...
Страница 58: ...PCB Layout ESIE06 03 1 58 Part 1 System Outline 3 1 1 4 5 ...
Страница 60: ...ESIE06 03 2 2 Part 2 Functional Description 3 1 2 5 ...
Страница 68: ...Hydro box Functional Concept ESIE06 03 2 10 Part 2 Functional Description 3 1 2 4 5 ...
Страница 88: ...ESIE06 03 3 2 Part 3 Troubleshooting 3 1 3 5 ...
Страница 134: ...Error Codes System Malfunctions ESIE06 03 3 48 Part 3 Troubleshooting 3 1 3 4 5 ...
Страница 152: ...Additional Checks for Troubleshooting ESIE06 03 3 66 Part 3 Troubleshooting 3 1 3 4 5 ...
Страница 154: ...ESIE06 03 5 2 Part 5 Disassembly and Maintenance 3 1 5 ...
Страница 180: ...Removal procedure outdoor unit ERYQ005 007AAV3 ESIE06 03 5 28 Part 5 Disassembly and Maintenance 3 1 5 5 ...