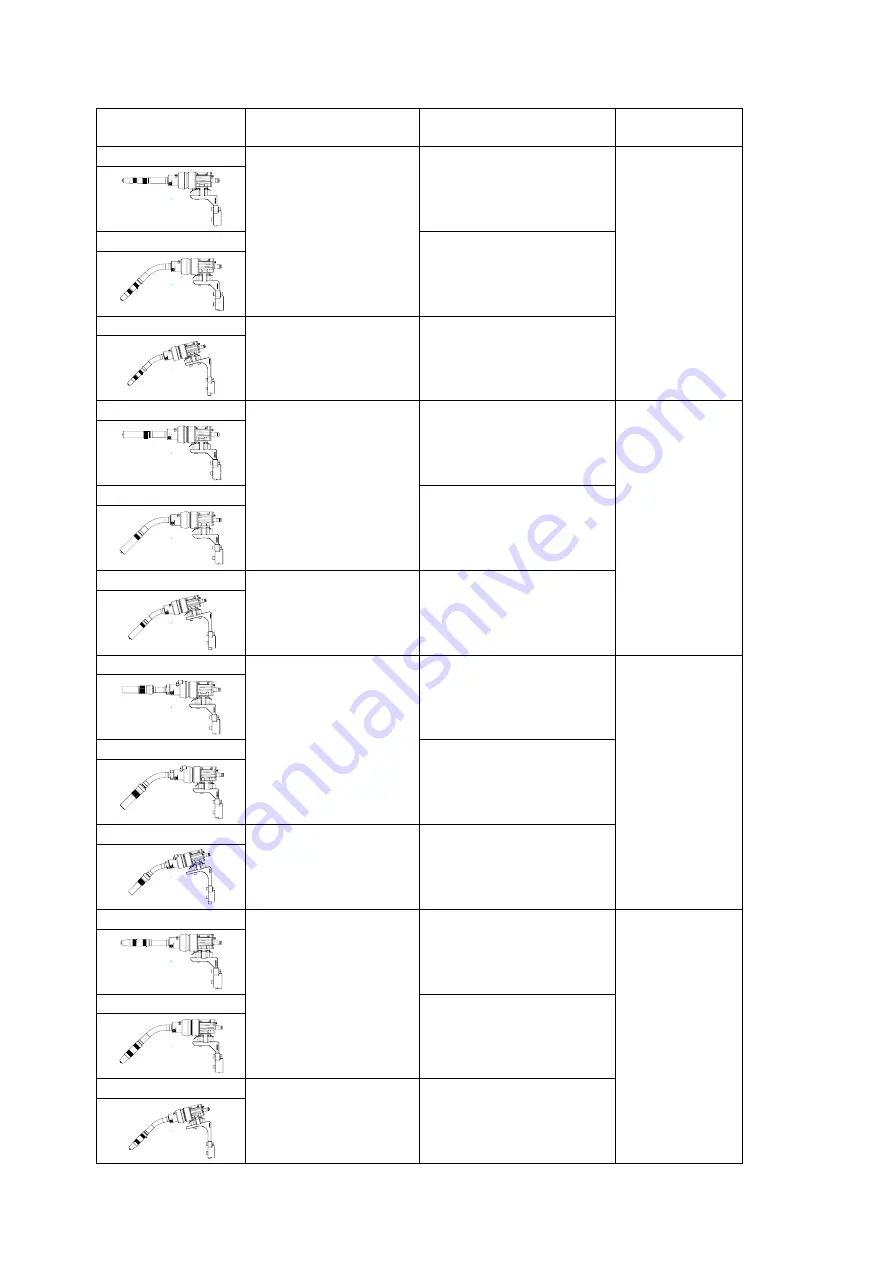
-
11
-
Table 3.1 Type of Torch mounting bracket ASSY / Torch gauge ASSY / Tip gauge
Torch model
Torch mounting
bracket ASSY
Torch gauge ASSY
Tip gauge
RT3500S
L6300E
RT3500H
L10620B
L6300C
RT3500L
L10620C L10620E
L317X
RT5000S
L6300E
RT5000H
L10620B
L6300C
RT5000L
L10620C L10620E
L317Z
RTW5000S
L6300E
RTW5000H
L10620B
L6300C
RTW5000L
L10620D L10620E
L10319H
RZ3500S
L6300E
RZ3500H
L10620B
L6300C
RZ3500L
L10620D L10620E
L10669D
Содержание OTC RT3500H
Страница 2: ......