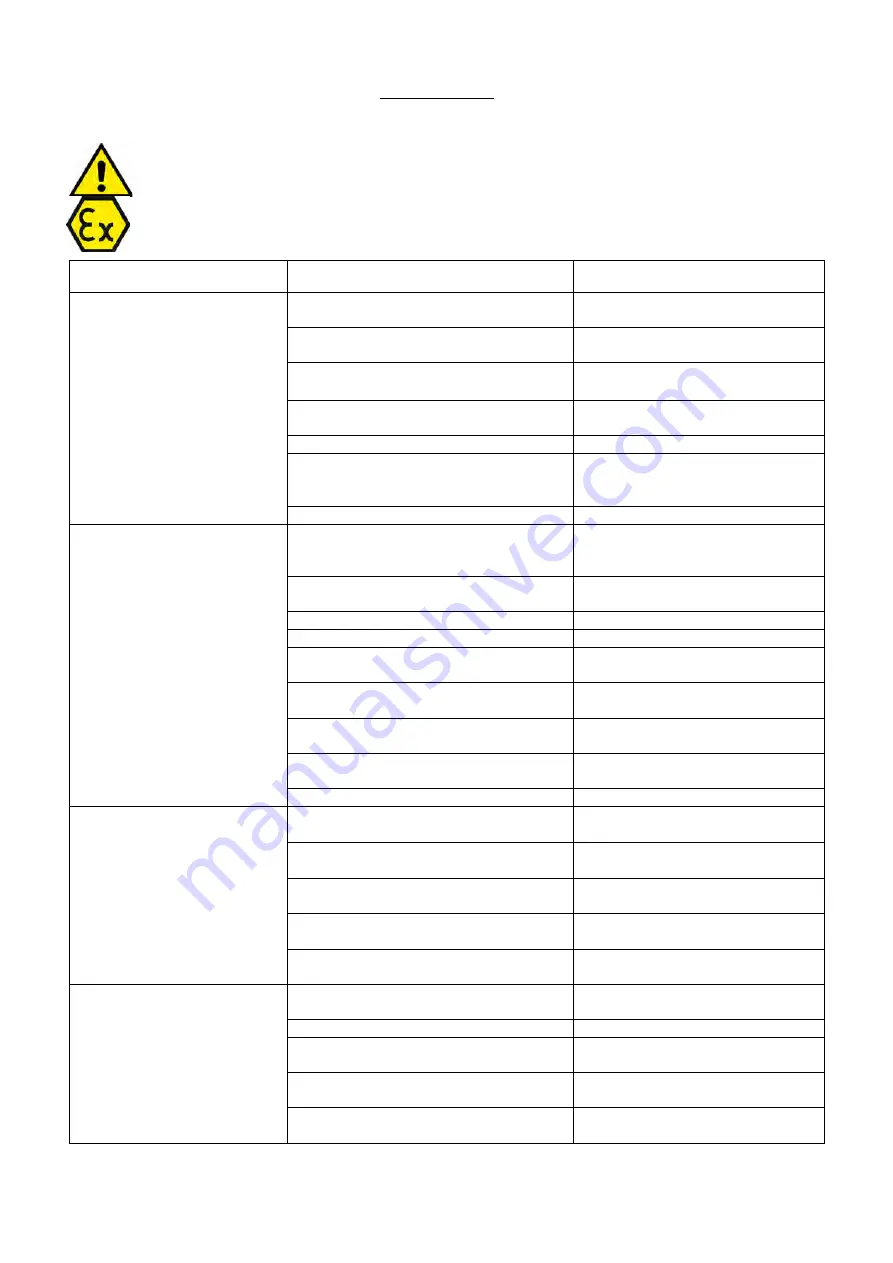
ENGLISH
29
Service instruction and service video can be found on www.dabpumps.com.
9. FAULT FINDING
Before attempting to diagnose any fault, make sure that the fuses have been removed or the mains switch has been
switched off. It must be ensured that the power supply cannot be accidentally switched on. All rotating parts must
have stopped moving.
All regulations applying to pumps installed in potentially explosive environments must be observed. It must be
ensured that no work is carried out in potentially explosive atmosphere.
INCONVENIENTS
PROBABE CAUSES
REMEDIES
Failure in
electric pump.
Lack of current to the motor.
Check electric network, supply cables,
connections and fuses.
Insufficient voltage.
Check the value (see chapter 10
“Technical Data”).
Thermal protection activated.
Wait for motor cooling, reset thermal
relay and check ratin starting.
No signal from electrodes for level control.
Wait for level reset, check efficiency of
level control relay and relevant electrodes.
One phase interruption (three-phase motors).
Reset connections.
Clogged impeller.
Remove obstruction, wash and clean
(contact the Assistance Service if
necessary).
Motor failure.
contact the Assistance Service.
Electric pump starting with thermal
protection intervention winding.
Voltage different from plate.
Measure the voltage between two phases
of the motor. Tolerance: - 10 %/+ 6 %.
Restore the correct voltage.
Wrong rotation direction.
Invert two of the three phases (see par.
7.2: “Direction of rotation”)
Three-phase motor: phase interruption.
Reset connections.
Three-phase motor: Low rating.
Adjust rating of relay value.
Short-circuit; earth leakage in electric cables or
motor.
Individuate interruption and repair (contact
the Assistance Service if necessary).
Too high temperature of pumped liquid.
Check whether the right type of pump has
been selected.
Pumped liquid too dense.
Dilute liquid. Check whether the right type
of pump has been selected.
Dry running of the electropump.
Check the level of liquid in the sinkhole
and the level control instruments.
Defective thermal relay.
Replace it.
Electric pump drawing more power
than value of plate.
Overload due to pump clogged.
Remove obstruction and clean (contact
Assistance Service if necessary).
Pumped liquid too dense or viscious.
Dilute liquid. Check whether the right
pump has been selected.
Overload due to obstruction.
Remove obstruction and clean of
extraneous bodies.
Wrong rotation direction.
Invert two of the three phases (see par.
7.2: “Direction of rotation”).
The pump is operating outside the allowed
working range.
Check the work point of the pump and, if
necessary, increase the delivery pressure.
Insufficient performances.
Suction, impeller, valve ordelivery pipeline
clogged.
Clean carefully.
Weared pump or impeller.
Replace or repair.
Errato senso di rotazione.
Invert two of the three phases (see par.
7.2: “Direction of rotation”).
Air or gas in the pumped liquid.
Increase dimensions of pit or collecting
tank and foresee degasing devices.
Presence of air in the pump.
Vent the pump. (see installation
paragraph).