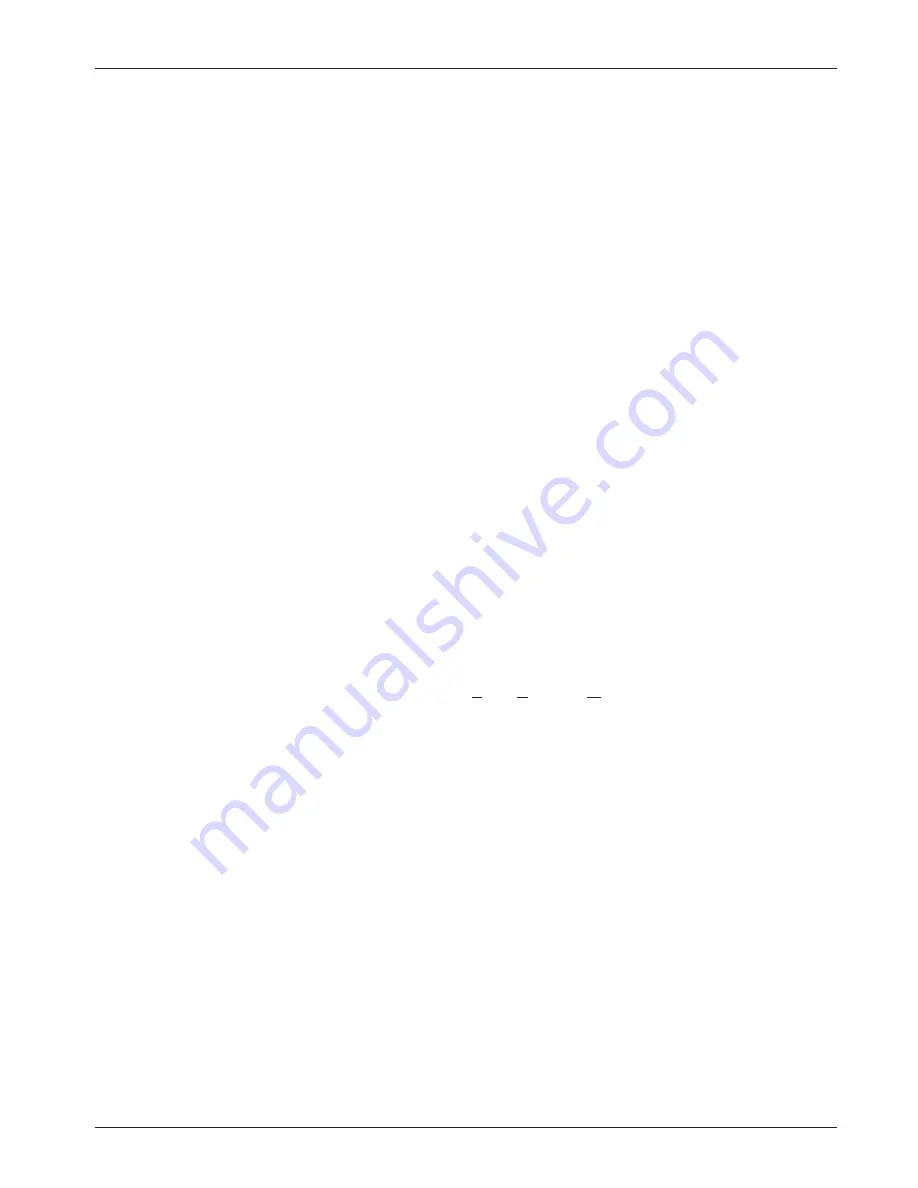
Curtis PMC 1297 Manual
A-9
APPENDIX A: GLOSSARY
Smooth, stepless operation
Like all Curtis PMC 1200 Series controllers, the 1297 allows superior operator
control of the vehicle’s drive motor speed. The amount of current delivered to
the motor is set by varying the “on” time (duty cycle) of the controller’s power
MOSFET transistors. This technique—pulse width modulation (PWM)—
permits silent, stepless operation.
Speed limiting
The maximum traction motor speed can be limited in two ways: through the
maximum speed parameter
(see Section 3
A
, page 31)
and through the minimum
field current limit parameter
(see Section 3
A
, page 41).
The latter (Field Min) is
the primary means of adjusting vehicle top speed.
The maximum pump motor speed can be limited through the maximum
pump speed parameter
(see Section 3
B
, page 46)
.
Spyglass display
The Curtis 840 Spyglass display sequences between hourmeter, BDI, and fault
code messages—
see Section 2, page 19
.
Static-return-to-off (SRO)
The programmable SRO feature prevents the vehicle from being started when
“in gear” (i.e., with a direction already selected)—
see Section 3
A
, page 45
.
Status LED
A built-in Status LED (Light Emitting Diode) is visible through the label
located on top of the 1297 controller. The Status LED flashes a 2-digit fault
identification code when a fault is detected by the controller. The fault code
continues to flash until the fault has been corrected and the fault condition has
been cleared. Clearing the fault condition typically requires cycling KSI for
faults detected during startup, and cycling the interlock switch for faults
detected during operation. The fault codes are defined in Table 6—
see Section
7, page 87
.
Taper rate
The taper rate determines how quickly the vehicle changes direction when the
opposite direction is selected—
see Section 3
A
, page 26.
Temperature compensation for current limits
Full temperature compensation provides constant current limits throughout the
normal operating range (heatsink temperatures of -25
°
C to +85
°
C). The
temperature sensor that regulates the current limits is also used to calculate the
heatsink temperature displayed by the programmer.