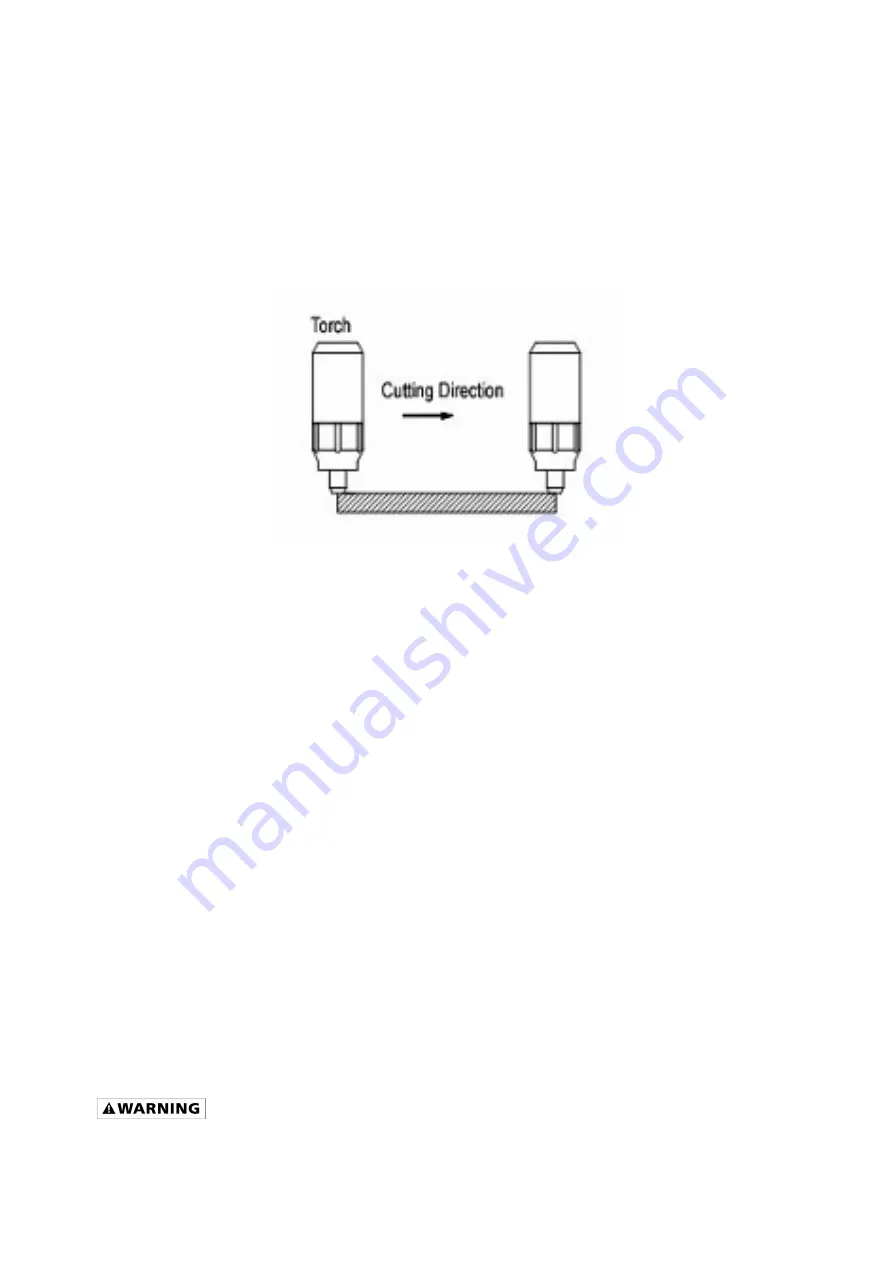
Page of 15
10
2. CUTTING OPERATION
2.1. Metal Sheet Cutting
- Put the torch’s nozzle at the start of the work piece. Turn on the torch switch to ignite the plasma
pilot. After the work piece is cut thorough, move the torch along the cutting direction uniformly. The
cutting speed is determined by watching to see if the cutting goes all the way through. If the speed
is too fast, the work piece won’t be cut thorough, or if too slow, the cut quality would be affected,
excessive warping may occur, or the arc could stop.
- When you’ve completed the cutting process, turn off the torch; the plasma pilot arc will stop.
2.2. Metal Mesh Cutting
-Fix the work piece and connect the earth cable with the work piece.
-Put the cutting nozzle onto the workpiece, lift torch up slightly from the work piece and turn on the
switch to cut.
2.3. Notice while cutting
- Unnecessary igniting of the pilot arc in the air will reduce the life-span of the torch’s electrode and
nozzle.
- It is best to start cutting at the edge of the work piece, unless you are piercing the work piece.
- Keep a space between the nozzle and the work piece. Pressing the nozzle on the work piece could
cause the nozzle to stick, reducing the smoothness of the cutting action creating an undesirable
result.
- Keep the torch’s nozzle vertical against the work piece, and watch to be sure the arc is moving
along the cutting line.
- For thin materials reduce the amperage setting to get the best cutting quality, reduce excessive
warping and to extend the life of the electrode and nozzle.
- Do not rapidly switch the torch trigger on and off; this will damage the pilot arc system and work
piece.
- The plasma cutter’s working air pressure range is 50-90psi. Notice: the internal pressure switch will
shut off when the air pressure falls below 50psi. The switch only works when the pressure rises to
50psi or above.
- Every 4-8 hours, check the air filter on your air supply and remove excess moisture. Too much
moisture in the cutter or torch may lead to operational trouble.
Always unplug the power supply before checking for and removing moisture.
Содержание PC 375
Страница 15: ...Page of 15 13 Circuit Chart...