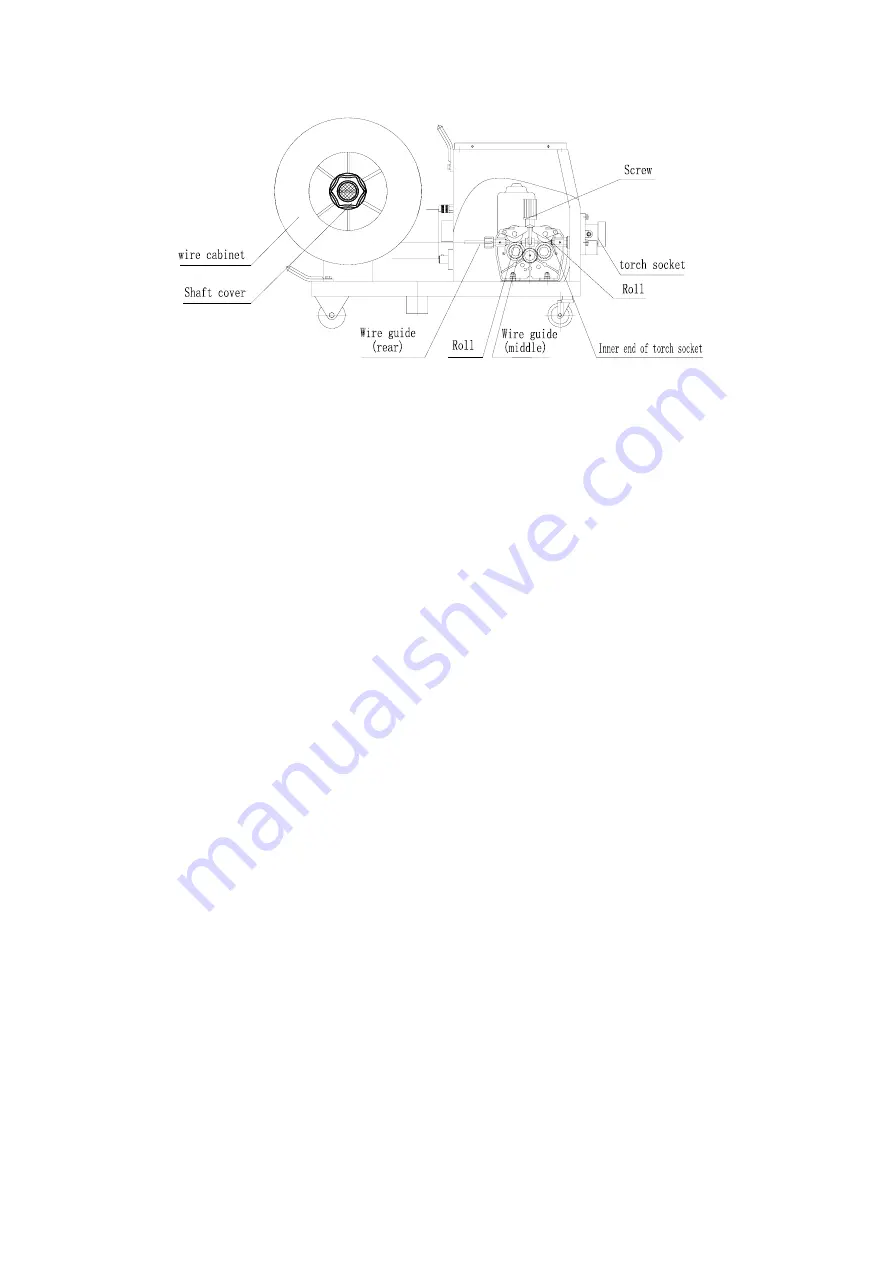
Page
10
5.5 Installation and Connection for Wire Feeder System (See Chart)
* Select suitable wire
for the
welding job. The wire diameter must be matched with drive roll; wire guide pipe
liner and contact tip (Please Refer to Table 3).
* Open the cover of wire cabinet, put wire spool on the shaft. Attention: Wire end under the wire spool
opposite wire feeder.
* There is damping screw device in the wire spool (hex head screw will be seen when open the cover).Pull the
wire reel with hand when coarsely adjust. If resistance is over large, may adjust damping bolt, screw
clockwise will enlarge, and vice versa. The cover must be screwed firmly after adjustment.
* Feed wire into “Wire Guide Rear” of wire feeder, align wire with roll groove through “Feed Roll”.
5.1.6 Connection between HD and Torch
* Connect torch head with “Torch Socket” on front panel.
5.1.7 Connection between HD and Work Piece
Connect quick connector (male) of earth cable to the socket on the front panel of welding machine, and
twist the quick connector (male) clockwise to ensure the tight connection. The other end clamps work
piece.
6.
Operation
Notice:
* Cut off power and close valve when finished welding or leave the job site temporary.
* The welding worker should wear protected gear.
* Isolating light screen must be placed around the job site in case of arc light influence.
* Inflammable or explosive materials are prohibited to access the job site.
6.1 Wo r k P i e c e C l e a n i n g B e f o re We l di ng
Weld site must be cleaned, no existing rust, greasy dirt, water and paint etc.
6.2 A d j u s tm e n t a n d Te s t b e fo re We l di ng
* The fan will work after connecting.
* Pressure data will be shown after open the valve of CO
2
cylinder.
* Open the valve of gas regulator (rotate clockwise), loose “feed roll”, press torch switch, adjust gas flow to
meet the requirements of technology and then press “feed roll”.
* Press torch switch and feed the wire to torch head.
* The torch cable must be pulled a line in case of wire jam.
* The nozzle and contact tip must be dismantled when testing wire feeding to prevent wire jam at torch head.
* First, please observe the wire whether through the groove of feed roll when wire feeding, if not, adjust.
Second, please observe whether wire feeding speed is even. If not, the reason may be that the pressing roll
is too firm or loose. You should adjust it to assure of even feeding.
Содержание HD-350
Страница 21: ...Page 19...