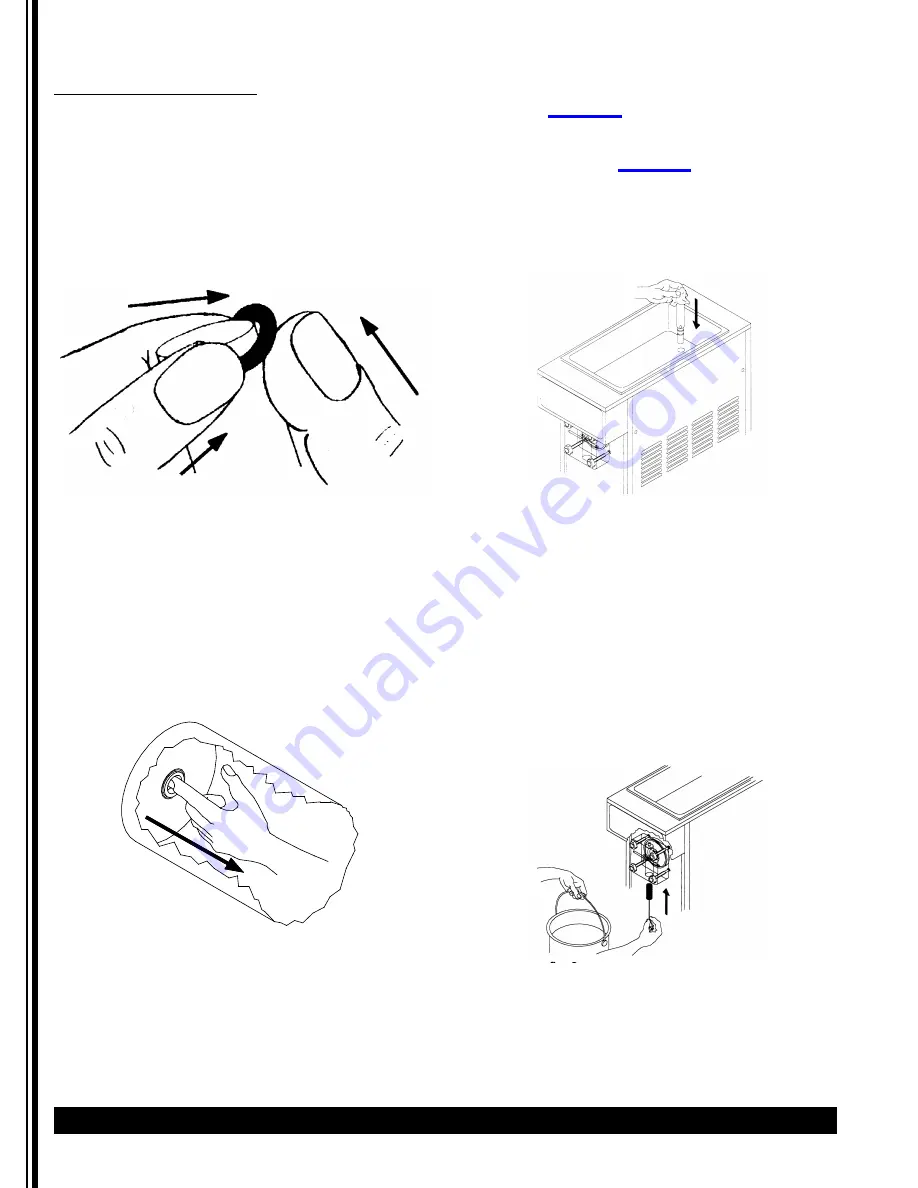
10
Crathco
®
Model 3311 Beverage Freezer
Cleaning and Maintenance (continued)
Disassembly and Cleaning
NOTICE:
The best way to remove an O-ring is to first
wipe off all of the lubricant using a clean paper towel.
Pinch the O-ring upward with a dry paper towel
between your index finger and thumb. When a loop is
formed in the O-ring, roll it out of the groove with your
other thumb. Always remove the O-ring farthest from
the end of the plunger first. Be careful not to pull or
tug excessively on O-rings. O-rings can be distorted and
will deteriorate sealing performance.Carefully inspect
the O-rings and replace if necessary. (See Figure Q)
3. Remove the dasher assembly from inside the
freezing cylinder taking care to avoid damaging
the rear seal assembly at the back of the
freezing cylinder. Disassemble the dasher
assembly by removing the stator rod and front
and rear stator rod bearings.
4. Remove stationary half of the shaft seal
assembly from the back end of the freezer
cylinder. This is accomplished by reaching into
the cylinder and pulling seal out with your
index finger. (See Figure R)
5. Slide the rotary half of the seal off the dasher
shaft. Inspect both seal components carefully
for nicks or cracks. Replace seal if defective.
NOTICE:
To prevent leakage the surfaces of the rotary
seal and the stationary seal must be smooth with no
chips or cracks.
NOTICE:
All units are shipped with a standard ceramic
seal (Part #
) unless otherwise specified.
Certain products contain coconut oil which requires a
different sealing material. For these products use the
coconut oil seal (Part #
). The stationary half
of the standard seal has a white polished surface. The
stationary half of the coconut oil seal has a glossy black
surface.
6. Remove carb tube from bottom of hopper and
remove O-rings. (See Figure S).
7. Remove drip tray and empty contents.
8. Take all components to the cleaning area.
9. Prepare 1 gallon solution of hot tap water and
common dishwashing detergent.
10. Thoroughly wash all components in a warm,
mild detergent solution including the inside of
the freezing cylinder and the mix storage
hopper.
DO NOT WASH COMPONENTS IN A
DISHWASHER.
11. Use a medium sized brush to clean the bottom
of the valve body and the inside of the plunger
bore with detergent solution taking care to
remove only remaining lubricant. (Figure T)
12. The exterior of the freezer should be cleaned as
needed with a cloth towel.
NOTICE:
Coarse rags, abrasive cleaners
and excessive force can damage and/or
scratch the surfaces of the freezer.
Figure Q
Ring Removal
Figure R
Removal of stationary half of seal
Figure S
Carb Tube
Figure T
Clean Valve Body
Содержание Standard 3311
Страница 34: ...34 Crathco Model 3311 Beverage Freezer Spinner Hook Up Model 3311 AC WC Units 115V Model Model 3311 220V Model...
Страница 38: ...38 Crathco Model 3311 Beverage Freezer Refrigeration Schematic Model 3311 115 220V Air Cooled Models...
Страница 39: ...Model 3311 Beverage Freezer Crathco 39 Refrigeration Schematic continued Model 3311 Water Cooled Models...