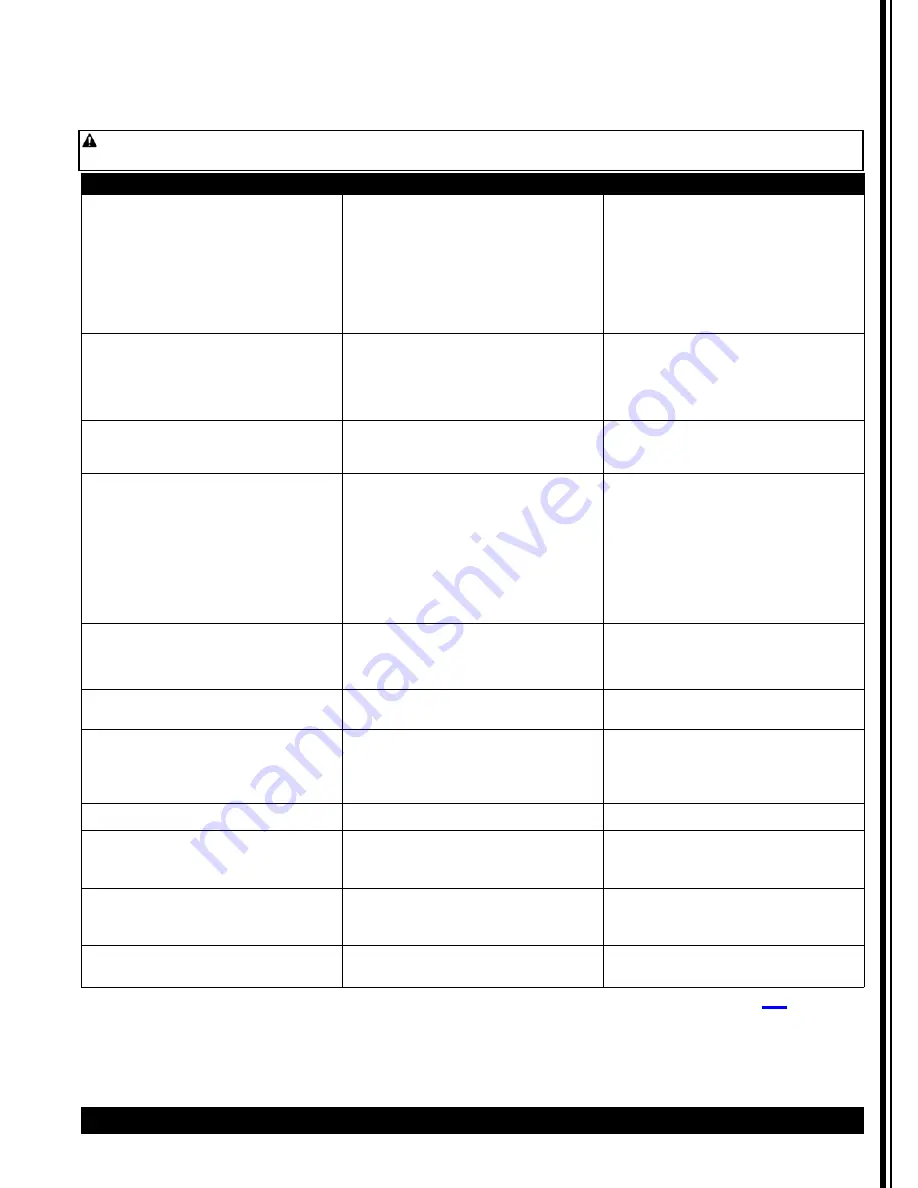
Freezer problems originate from three sources - improper operation, mix problems, or mechanical malfunction.
Always check for improper operation and mix problems first, as they are the most common cause of most
equipment problems
.
CAUTION:
Always disconnect power before attempting any maintenance procedures.
Only a qualified service technician should perform electrical and mechanical adjustments or repairs.
Model 3311 Beverage Freezer
Crathco
®
17
Troubleshooting
PROBLEM
PROBABLE CAUSE
SOLUTION
Machine will not run or freeze down
• Machine not plugged in
• Circuit breaker tripped or fuse blown
• Machine in CLEAN or OFF position
• Obstructed condenser air flow
(Air-cooled units)
• Compressor not operating
• Dasher not installed
• Low refrigerant charge
• Plug machine in
• Reset breaker or replace fuse
• Switch to ON position
• Clean condenser. Allow 6” (15 cm)
on both sides
• Check for cause and correct
• Install dasher (auger)
• Check for leaks, repair, and recharge
Product too soft
• Consistency setting too loose
• Consistency setting at maximum
(red spring)
• Product BRIX level too high
• Too much alcohol in mix
• Readjust consistency control
• Change to yellow consistency spring
• Lower liquid product BRIX level
• Lower alcohol content
Product too stiff
• Consistency adjuster set too firm
• Product BRIX level too low
• Readjust consistency setting or change
to red spring
• Increase product BRIX level
Product will not dispense
• Power switch OFF
• Inadequate mix in hopper. Red MIX
LOW light on
• Consistency adjuster set too firm
• Carburetor inlet hole clogged
• Drive belt broken or off pulley
• Drive shaft worn
• Drive motor failure
• Turn power switch ON
• Refill hopper
• Readjust consistency setting
• Unclog carburetor inlet hole
• Repair or replace
• Inspect square drive shaft pocket for
excessive wear, replace
• Replace motor
Leakage from drain tube, front of freezer
above drip tray
• Worn or defective shaft seal
• Seal installed incorrectly
• Replace seal and then lubricate at
each cleaning
• Remove and install seal
Excessive Dispensing Valve Leaks
• Worn or defective O-ring(s)
• Replace and lubricate
Clicking sound from inside machine
• Low voltage
• Extension cord is used
• Use dedicated circuit with proper
rating
• Connect directly to power source or
use power cord of proper size
Thumping sound from inside machine
• Worn belt
• Replace belt
Scraping sound during freeze down
• Frozen product scraping off of
cylinder walls
• No product in machine
• Sound should go away when product
is frozen to proper consistency
• Fill with product
Premature seal wear
• Incorrect installation of dasher
• Improper drive shaft clearance
• Incorrect shaft alignment
• Advise careful installation
• Adjust to proper
• Align shaft
Merchandiser light flickers when freezer
cycles
• Low voltage
• Connect freezer to dedicated circuit
with proper rating
If you still need help, call Grindmaster-Cecilware Technical Service Department, (502) 425-4776 or (
) 695-4500
(USA & Canada only) (Monday through Friday 8 AM - 6 PM EST). Please have the model and serial number ready
so that accurate information can be given.
Prior authorization must be obtained from Grindmaster-Cecilware for all warranty claims.
Grindmaster-Cecilware provides the industry’s BEST warranty. Visit our website at GMCW.com for
warranty terms and conditions.
Содержание Standard 3311
Страница 34: ...34 Crathco Model 3311 Beverage Freezer Spinner Hook Up Model 3311 AC WC Units 115V Model Model 3311 220V Model...
Страница 38: ...38 Crathco Model 3311 Beverage Freezer Refrigeration Schematic Model 3311 115 220V Air Cooled Models...
Страница 39: ...Model 3311 Beverage Freezer Crathco 39 Refrigeration Schematic continued Model 3311 Water Cooled Models...