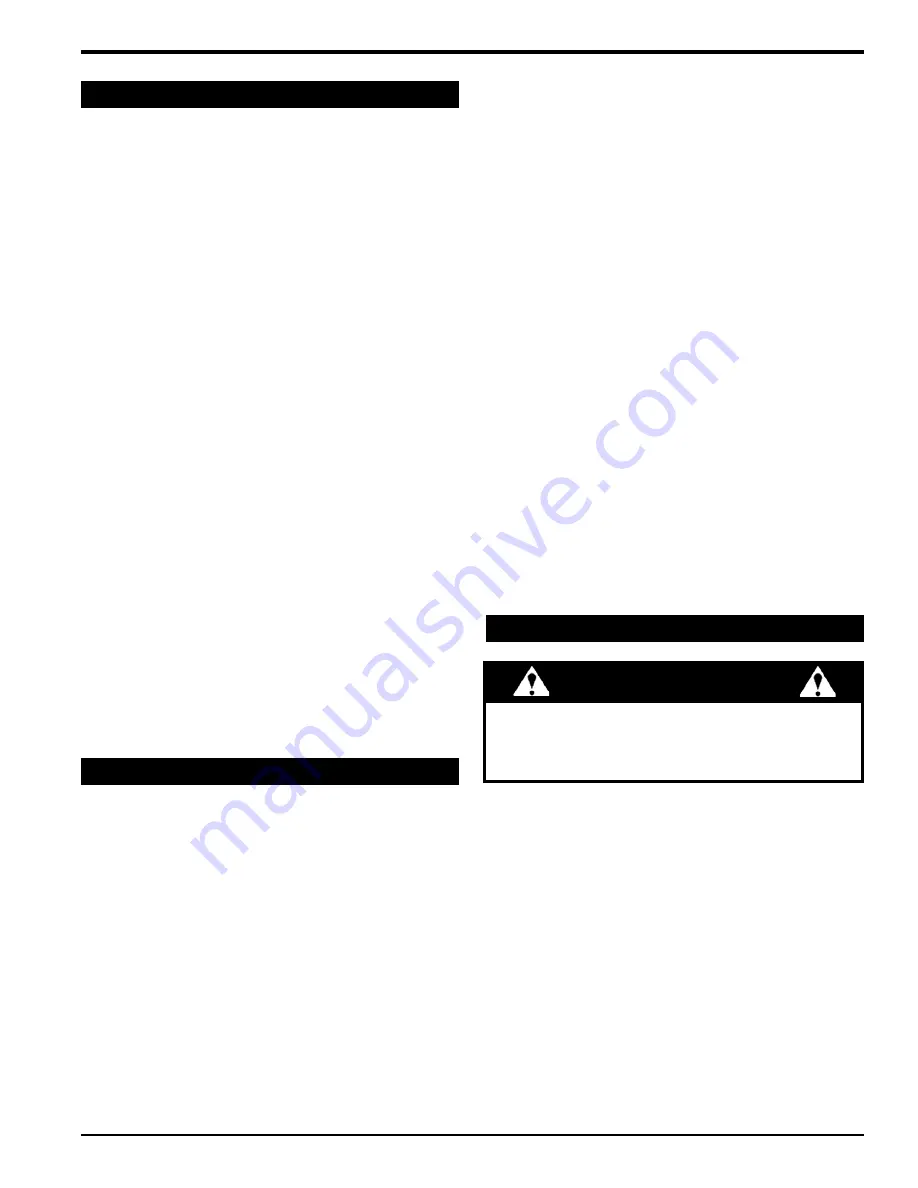
PN 26037-00 R072208
37
OPERATION
5.3 pRe-opeRaTion checKliST
5.4.1 pRe-STaRT inSpecTion
Read the Operator’s Manual.
1.
Check that the hydraulic lines and electrical harnesses are
2.
routed where they will not contact moving parts. Be sure all
components are clipped, taped or tied securely in place.
Check that all required nuts and bolts are installed and
3.
tightened to their specified torque.
5.4 machine bReaK-in
Efficient and safe operation of the CWS requires that each op-
erator reads and understands the operating procedures and all
related safety precautions outlined in this section. A pre-operation
checklist is provided for the operator. It is important for both per-
sonal safety and maintaining the good mechanical condition of
the machine that this checklist is followed:
Before operating the machine and each time thereafter, the fol-
lowing areas should be checked off:
Service the machine per the schedule outlined in the Service
1.
Record.
Use only a combine of adequate power and specifications
2.
to operate the machine.
Check that all guards are installed, secured and function-
3.
ing as intended. Do not operate with missing or damaged
shields.
Ensure that the machine is properly attached to the header
4.
and that mechanical retainers, such as quick pins, are in-
stalled.
Check the cutterbar, reel area and drives for entangled
5.
material.
Check the chains and sprockets for proper tension and align-
6.
ment. Adjust as required.
Visually inspect the hydraulic system for leakage, loose fit-
7.
tings, and damaged hoses. Tighten fittings, replace damaged
components and wipe up leaked or excess hydraulic fluid.
Check condition of driveline slip clutch friction discs. If install-
8.
ing replacement discs, adjust spring height to original height.
Deviation from original setting may be needed depending
upon disc wear. Run-in is recommended at the start of the
season (see section 5.2.2).
5.4.2 afTeR opeRaTing foR 2 houRS
Re-torque fasteners and hardware.
1.
Check that all safety decals are installed and legible. Apply
2.
new decals if required.
Check that no hydraulic hoses are being pinched, crimped,
3.
or are rubbing. Reroute as required.
Check that the wiring harness is not being pinched, crimped,
4.
or rubbing. Reroute as required.
Check the tension and alignment of all drive chains. Adjust
5.
as required.
The gearbox will generate heat. The typical operating tem-
6.
perature of the gearbox is 180° F.
5.4.3 afTeR opeRaTing foR 10 houRS:
Re-torque fasteners and hardware.
1.
Check that all guards are installed, secured and function-
2.
ing as intended. Do not operate with missing or damaged
shields.
Check safety decals. Install new ones if required.
3.
Check the routing of hydraulic lines and the wiring harness.
4.
Reroute as required to prevent pinching, crimping, binding,
or rubbing.
Refer to the normal servicing and maintenance schedule as
5.
defined in the Service Record.
5.5 neuTRal dRive ShafT (opTional)
When harvesting in conditions where air flow is unnecessary,
you can bypass the fan to improve combine fuel economy. To
do so, place all controls in neutral or off, stop combine engine,
set parking brake, remove ignition key, and wait for all moving
parts to stop. Then, move the driveline ends that are connected
to each end of the gearbox stub shaft to the neutral shaft located
behind the fan.
To slide a driveline on and off the splined shafts, pull back the
spring-loaded collar at the end of the driveline. After moving the
driveline to the desired shaft, release the end collar and make
sure the driveline locks into place on the shaft.
Place all controls in neutral or off, stop combine engine, set
parking brake, remove ignition key, wait for all moving parts to
stop, then properly block machine before servicing, adjusting,
repairing, or unplugging.
WaRning
Содержание CWS 1010
Страница 35: ...PN 26037 00 R072208 31 ASSEMBLY Figure 27 Air hose installation 4 15 FAN HOSE ASSEMBLY...
Страница 54: ......
Страница 55: ......
Страница 56: ...237 12th St NW P O Box 849 West Fargo ND 58078 0849 PH 1 800 247 7335 FAX 701 282 9522 www crary com...