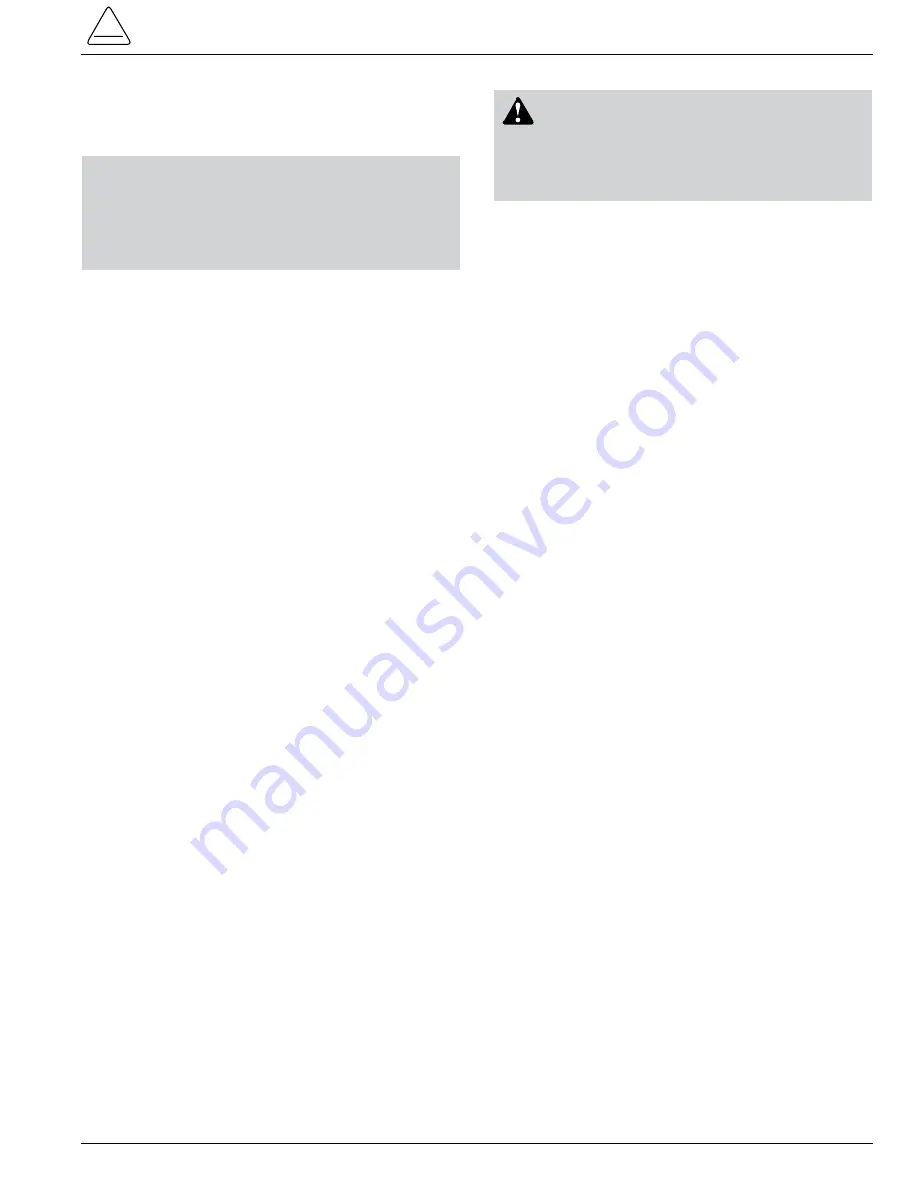
43
S225-10-30
!
SAFETY
FOR LIFE
External Application of a Motor Start
Capacitor on a Single-Phase Voltage
Regulator
Test the motor capacitor before performing this procedure.
Refer to the
Motor Capacitor Problem
section of this
manual.
Introduction
A step voltage regulator utilizes a capacitor to start the
motor of the tap-changer. A number of regulators operat-
ing in the field have an internally mounted, under-oil motor
start capacitor. The motor start capacitor, if failed, will not
allow the tap-changer to operate. In this situation, the
motor may be able to be operated by proper application of
a capacitor in the control box of the regulator.
Required Items
•
Appropriately sized temporary capacitor. If in doubt as
to correct capacitor size, contact the Cooper Power
Systems Service Department.
Spring-drive model McGraw Edison regulator tap-
changers utilized a 7.5 μF, 440 V, 100 ˚C capacitor.
Direct-drive model McGraw Edison regulator tap-
changers, built 1994 and earlier, utilized a 40 μF, 440 V,
100 ˚C capacitor.
Direct-drive model McGraw Edison regulator tap-
changers, built 1995 and after, utilized a 50 μF, 440 V,
100 ˚C capacitor.
QD-8 and QD-5 Quik-Drive model Cooper Power
Systems regulator tap-changers utilize a 50 μF, 440 V,
100 ˚C capacitor.
QD-3 Quik-Drive model Cooper Power Systems regu-
lator tap-changers, for domestic use, utilize 12 μF,
440 V, 100 ˚C motor capacitors.
QD-3 Quik-Drive model Cooper Power Systems regu-
lator tap-changers, for international use on 50 Hz regu-
lators, utilize 15 μF, 440 V, 100 ˚C motor capacitors.
•
Temporary capacitor leads.
Leads should be connected to the temporary capaci-
tor terminals and have terminals on the free lead end
that can be attached to a control box terminal screw or
wire. Alligator clips work well in most applications.
• Screwdriver.
As needed to allow capacitor leads to be attached into
the control circuit where screw terminals are present.
Procedure
.
Identify the raise (R) and lower (L) circuits coming into
the control box from the regulator.
2 .
Place a momentary short circuit across the raise and
lower leads to discharge any residual capacitive volt-
age that may be in the motor circuit.
3 .
Connect temporary capacitor leads. Connect the tem-
porary capacitor leads across the raise (R) and lower
(L) circuit lead wires on
TB
1
, located on the top of the
control assembly back panel. A capacitor connected in
this way electrically replaces the failed internal capaci-
tor.
4 .
Operate the tap-changer. Energize the control and run
the regulator to neutral.
5 .
Remove the unit from service, as outlined in the
INSTALLATION: Removal from Service
section of
this manual.
6 .
Remove the internal capacitor.
7 .
Install an external capacitor, located electrically between
the position indicators mechanical limit switches and
the motor.
Note:
The described procedure will work in cases where
the limit switches located in the position indicator
are closed. Closed switches provide the electrical
path necessary for the capacitor to be across the
raise and lower motor windings. If either of the limit
switches are open, the circuit is interrupted and the
motor will not turn. Limit switches are typically open
at
6 Raise
or
6 Lower
or at whatever tap posi-
tion they are set to open. Any permanent place-
ment of a capacitor must be electrically connected
between the motor and the limit switches.
WARNING:
Hazardous Voltage. Residual capaci-
tive voltage may be present in the motor circuit.
Remove the power from the control box and follow the
appropriate shorting procedure to discharge any residual
voltage. Failure to comply can cause serious injury or
death.
VR-T229.0
CAUTION:
Equipment Damage. Test the motor capaci-
tor before performing this procedure. Installing another
motor capacitor in the circuit with a motor capacitor that
is not open will result in double capacitance and double
motor current. Failure to comply can result in damage to
the control panel.
VR-T228.0