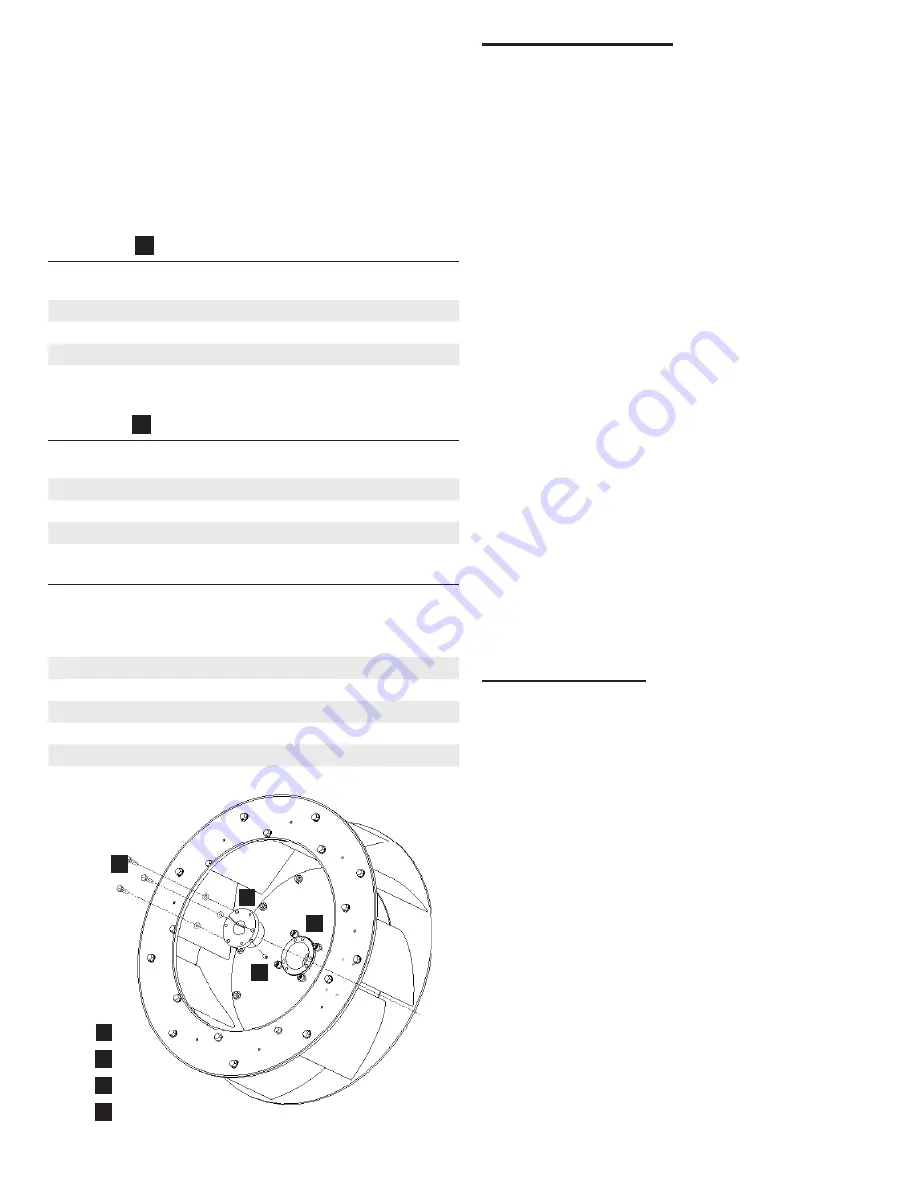
3
MPA IO&M
B51223-005
Hub
Bushing
Bushing Screws
Bushing Set Screw
D
C
B
A
D
C
B
A
Verify fastener tightness, these may have loosened
during shipment or installation:
• Bushing set screw torque
• Bolts on inlet funnel.
• Motor bolt torque
• Nuts holding housing frame to base and base to ground
(customer specifications)
• Bushing fastener torque
• Ensure piezo ring tubing will not contact the impeller
Perform list again until unit is operating properly.
Motor Maintenance
The three basic rules of motor maintenance are to keep the
motor clean, dry, and properly lubricated. Keeping motors
and windings clean is important because dirt and dust
can cause heat to be trapped causing overheating and/or
premature failure. Blow dust and dirt out of windings and off
the motor periodically. Use low pressure (50 psi) airstream
to prevent winding damage. Keep the areas surrounding the
motor clear so the air can circulate through the motor cooling
fan.
Motors should be kept dry to avoid electrical short circuits.
Motors kept in storage for long periods of time can have
moisture condense on the windings. Be certain the motor is
dry before using.
Some smaller motors are permanently lubricated. Motor
bearing lubrication, if required, must follow a rigorous
schedule. Motors less than 10 hp running eight hours a
day in a clean environment should be lubricated once
every five years; motors 15 to 50 hp, every 3 years; and
motors 50 to 150 hp, yearly. See motor manufacturer
specifications for recommended greases. For motors in a
dusty or dirty environment or running 24 hours a day, divide
the service interval by 2. If the environment is very dirty or
high temperatures exist, divide the service interval by 4.
Lubrication requirements are normally attached to the motor.
Do not over-lubricate.
The major cause of motor bearing failure is contamination
of grease, insufficient grease, over lubrication, and
incompatibility of grease. If a fan is to be stored for any
length of time and the bearings are re-greasable, the motor
bearings should immediately be filled with grease while
rotating the fan and then the bearings should be re-greased
and rotated monthly. This will prevent moisture, which
condenses within the bearing, from corroding the raceways.
Troubleshooting
Use safety practices when investigating fan or system
performance problems. General safe practices and
performance troubleshooting guidelines can be found in
AMCA Publication 410: Recommended Safety Practices for
Users and Installers of Industrial and Commercial Fans, and
AMCA Publication 202-98 (R2011): Troubleshooting. Fan
application and field measurement procedures can be found
in AMCA Publication 201-02 (R2011): Fans and Systems
and AMCA Publication 203-90 (R2011): Field Performance
Measurement of Fan Systems.
The following chart on page 4 indicate possible
areas to check when air or sound values do not meet
expectations. Most fan problems can be pinpointed to
one of these areas:
Bushing Fastener Torque
Bushing Type
Screw Size
Recommended
Torque
JA
10-24
60 in-lbs.
SD/SDS
1/4-20
108 in-lbs.
SK
5/16-18
180 in-lbs.
SF
1/8-16
360 in-lbs.
C
Bushing Set Screw Torque
Bushing Type
Screw Size
Recommended
Torque
SD/SDS
1/4-20
60 in-lbs.
SK
5/16-18
110 in-lbs.
SF
3/8-16
200 in-lbs.
B
Motor Bolt Torque
NEMA Frame
Bolt Size
(Grade 5)
Washers
Size
(Top and
Bottom)
Recommended
Torque (ft-lb)
56-145T
5/16
5/16
18
182-215T
3/8
3/8
31
254U-286TS
1/2
1/2
75
324-365T
9/16
9/16
107
404T-405T
3/4
3/4
267