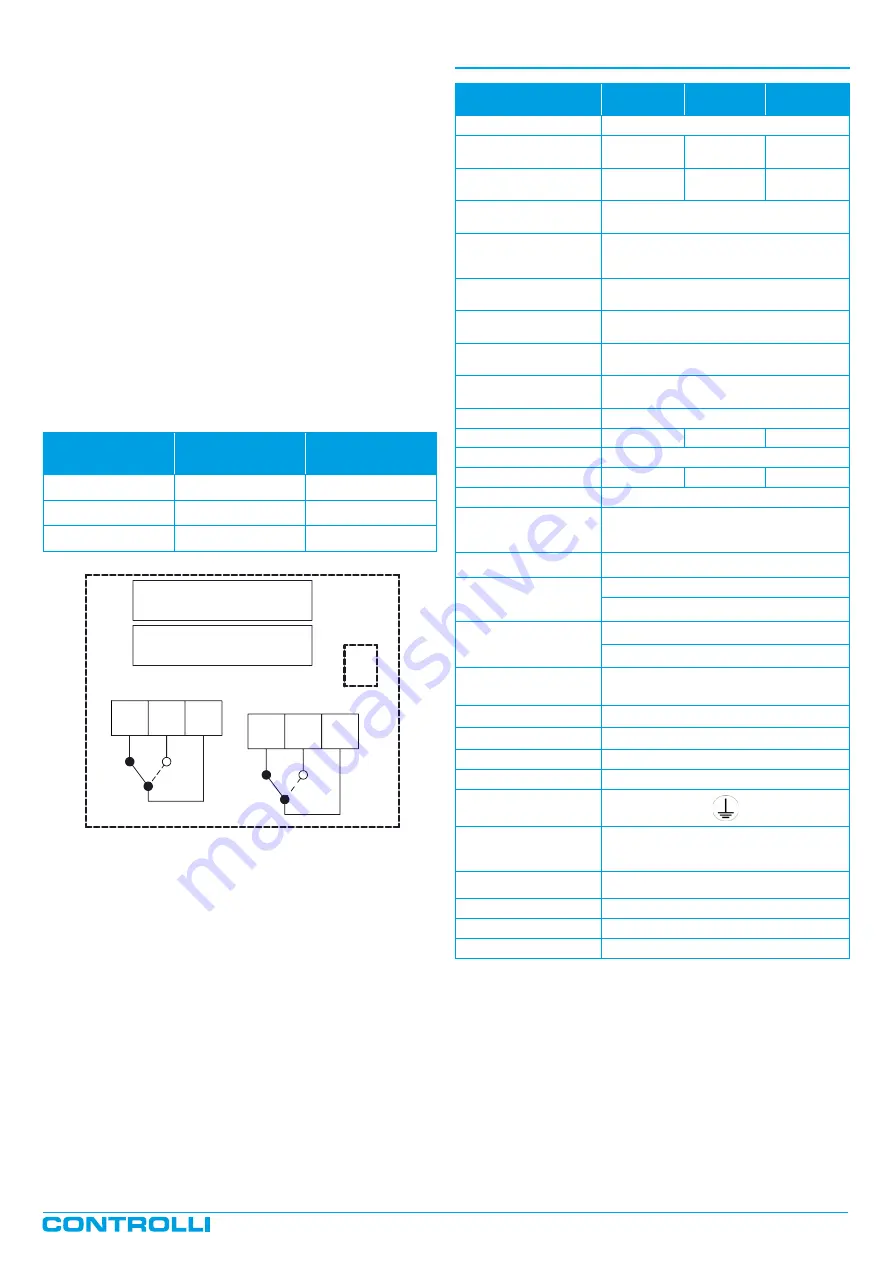
Manual operation handle can also be used to modify any DIP switch
setting or as re-set function after any alarm occurrence.
The actuator is supplied with the manual override lowered (ON). It
is not necessary to remove power supply to modify DIP switches set-
ting, but, in this case, pay attention to 230V high voltage presence.
Position Feedback
The actuator utilizes a 2-10V position feedback (look at DIP n. 1 set-
tings).
Calibration
The actuator has both auto and manual stroke calibration. The ac-
tuator is delivered with DIP n. 7 set to auto. Manual calibration is not
necessary unless maintenance is required on the valve or certain
alarm functions are desired.
End Point Auxiliary Switches (with accessory DMVE)
End point switches change over when the valve is fully open or
closed. They are free contacts with 24V AC/DC, 4A max voltage on
terminals. End point switches can be utilized to indicate valve stroke
end positions and for relay control of additional plant equipment.
When the actuators are controlled individually or in sequence, it is
possible to use the end switches to toggle when the valve is fully
open or fully closed. The auxiliary switch position according to con-
trol signal (Y) is shown in the picture below.
K1 K2 KC1
K1 K2 KC1
End point position
End point position
DMVE
RELE' DI CHIUSURA
RELE' DI APERTURA
K3 K4 KC2
Po
sizione
di fine corsa
Posizione di fine corsa
K3 K4 KC2
OPENING RELAY
CLOSING RELAY
DMVE
Diagnostic
The actuator is provided with a self diagnostic algorithm able to de-
tect faulty conditions:
•
stroke calibration out of range 5-60mm;
•
unexpected stall condition (e.g. valve stuck or extra stroke due
to actuator link loose);
•
voltage supply out of range.
These faulty conditions are signalled via the GREEN and RED LED on
the lower electronic board blinking accordingly (see “Diagnostic –
Alarm Function Table”).
Control signal (Y)
Relay
KC1
Relay
KC2
0-0,5Vdc
KC1 to K2
KC2 to K3
0,5-9,5Vdc
KC1 to K1
KC2 to K3
9,5-10Vdc
KC1 to K1
KC2 to K4
TECHNICAL CHARACTERISTICS
MVE206R
MVE206SR
MVE210R
MVE210SR
MVE215R
MVE215SR
Power supply F N
230Vac ±10%, 50-60Hz
Power consumption
(running)
13VA/6W
18VA/8W
21VA/11W
Power consumption
(holding)
11VA/5W
11VA/5W
13VA/7W
Charging phase
consumption
32VA/18W
Ultracapacitors charging
phase
(if totally discharged)
130s
Running and emergency
return time
1,1s/mm
Modulating with Controlli
valves stroke 16,5mm
18s
Modulating with Controlli
valves stroke 25mm
28s
Modulating with Controlli
valves stroke 45mm
50s
Floating
60s
Transformer Size [VA]
50
60
80
Stroke
5-60mm (limited to 30mm for MVE.SR)
Force
600N
1000N
1500N
Duty cycle
max 50%/60 minutes
Analogue input Y M
voltage 0-10V - impedance > 100kΩ (range:
0-10Vdc, 2-10Vdc, 0-5/2-6Vdc, 5-10/6-10Vdc)
500Ω (range 4-20mA)
Digital inputs Y1 Y2
connection of Y1, Y2 to M
Output V+
voltage 16Vdc ± 0,5V
max load 25mA,
Output U
voltage 2-10Vdc (0-100%)
max load 2mA
Number of cycles of
emergency
1.000
Type of movement
linear
Ambient temperature
operation -10T50°C; storage -20T50°C
Ambient Humidity
max 90% RH
Protection degree
IP54 (with PG13,5 cable gland - not supplied)
Insulation class
Standard
Emission/Immunity EMC 2004/108/CE according
to EN 61326-1;
LVD 2006/95/CE according to EN61010-1.
Material
housing: aluminium - cover: ABS plastic
Colour
aluminium / white
Weight [kg]
1,7 (MVE2xxR); 1,6 (MVE2xxSR)
Dimensions [mm]
refer to the picture on the page 7
1
st
Issue rev. b
04/2016
DBL462e
Page 2