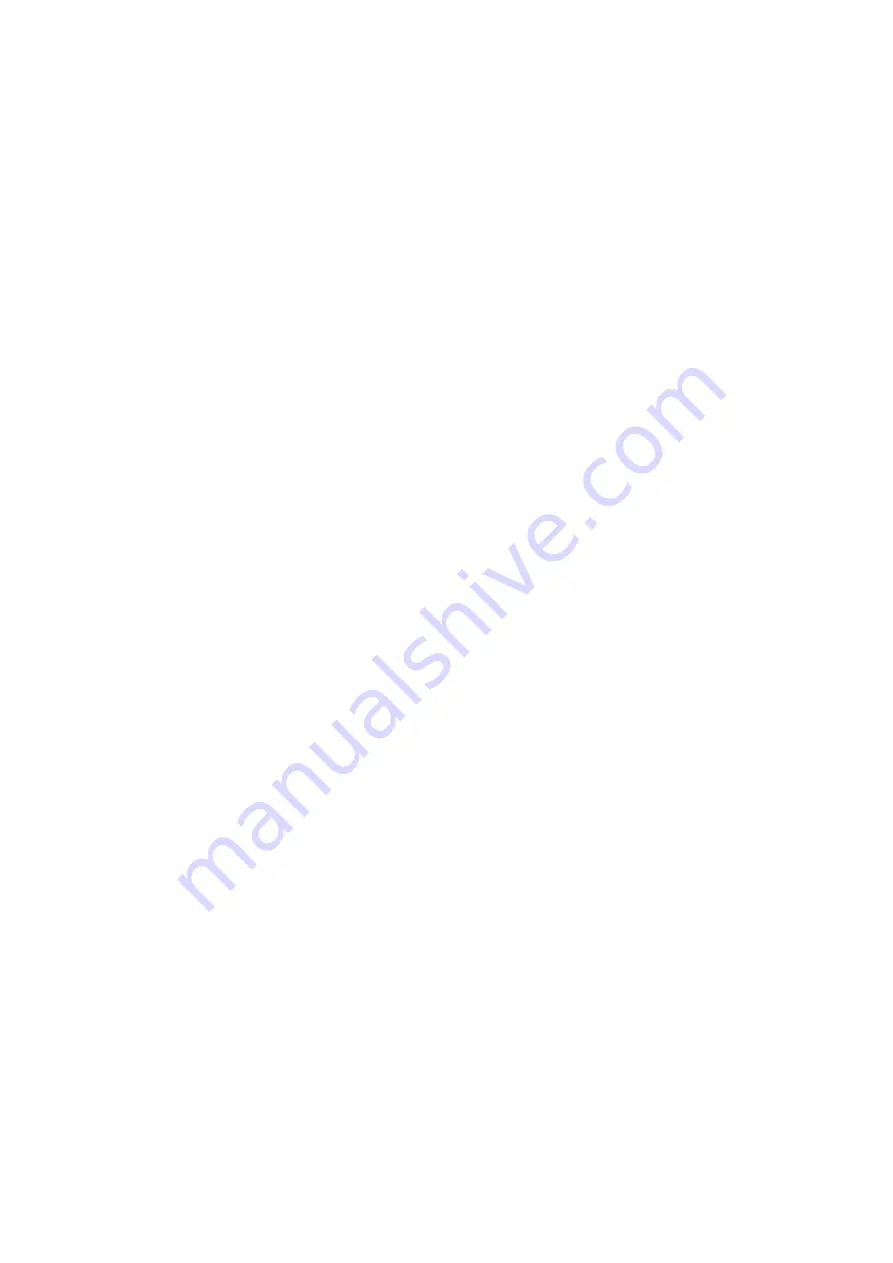
the joint with the iron tip. Don’t load the iron tip with a lot of extra solder, but work the joint in 1”
lengths, bringing in small quantities of solder. Brass is a very forgiving material and if you get
something out of alignment, use heat from the iron to desolder the joint before starting again. For
complicated assemblies, it is a good idea to only tack solder parts together. You can then make
adjustments by desoldering until you are happy with the location of parts and then solder solid.
When you need to laminate two or more layers of brass together, align the parts and carefully
clamp them together, either in the vice or by holding them with miniature crocodile clips. Run flux
around the edges, and then go around with the soldering iron. Clean up thoroughly afterwards.
To fit small parts and overlays on to a larger assembly, such as strapping to a wagon side,
when you need to prevent finely detailed areas such as planking becoming clogged up with
solder. Tin the back of the small component first, then hold in place on the model and apply flux.
Carefully wipe the tip of your iron on a sponge to remove any solder from it (dry iron), and then
touch it against the parts to be joined. After a few seconds you’ll see molten solder bubbling from
the edges. Remove the iron, still holding the parts in place, and allow the joint to cool. An
alternative is to use solder paint (I would recommend Carrs 188 solder paste). As the name
suggests, this is a flux and solder in one. Simply apply a thin coat of solder paint to the back of
the component instead of tinning. Still apply a small amount of liquid flux before you solder the
part into place.
Any surplus solder should be removed using a craft knife, I find No 10 curved scalpel blades
ideal, then burnish clean with a glass fibre brush. With practice, you’ll learn how to use the
minimum amount of solder to do the job. Flux is corrosive so, after each soldering session, give
your model a good scrub with washing up liquid or Jif. After a day or two, any remaining flux
residues will show as a green film, which should be washed away.
To cut parts from the fret, use a sharp Stanley knife on a piece of hardboard or a pointed
scalpel blade on a block of softwood. Remove tags and burrs with a fine file.
Three-dimensional parts are formed by folding. On an etched brass kit, the fold lines are
normally half-etched on the inside of the fold. You’ll be able to fold most parts using smooth-
jawed pliers. For longer parts folding bars are desirable.
Other useful tools include a bench vice, a good pair of tweezers, a set of Swiss files (get a full
set of cheap ones and then buy quality replacements for the three that you use the most), a pin
vice with a selection of drills from 0.5mm to 2.1mm plus a few larger sizes that you use regularly
(2.6mm for axle bearings etc), some square-nosed pliers and some very pointed-nosed ones,
preferably with smooth jaws. Buy cheap tools first and duplicate the most used ones with quality.
Try to complete all high-temperature soldering before attaching any of the cast whitemetal
parts. These can be attached with two-part epoxy resin such as Devcon or Araldite Rapid.
Ensure the surfaces to be glued are clean and free of grease.
A
better alternative is to solder your white metal castings using Carrs 70 degree low melt solder
and Carrs red label white metal flux. The iron should be run at a much lower heat so that you do
not melt the castings. I have a domestic light dimmer switch and plug socket fixed to a piece of
wood, wired up with a lead and 3 amp mains plug to the input side of the dimmer switch and the
output of the dimmer switch into the plug socket (remember to continue the earth). Plug your 40
Watt iron (25 Watt iron won’t work) with a clean and freshly tinned bit into this and experiment
with adjusting the switch until you find the range of temperature at which the solder melts, but a
scrap casting does not.
Note
as the iron is running at a lower voltage it will take longer to heat
up, so when you think the adjustment is correct do check a few minutes later on another scrap
casting to see that it doesn't melt. Then scribe a mark on the switch knob to indicate this position.
When attaching white metal fittings to brass the surface of the brass must be tinned with 145°
solder, to allow the solder to grip. The surface of the casting at the joint should be burnished
bright. The casting can then be soldered into place with 70° solder and fillets of solder run into
any gaps with no risk of melting the casting.
Page 3
Содержание GWR TOAD Diagram AA7
Страница 12: ...Page 12 ...
Страница 13: ...Page 13 ...