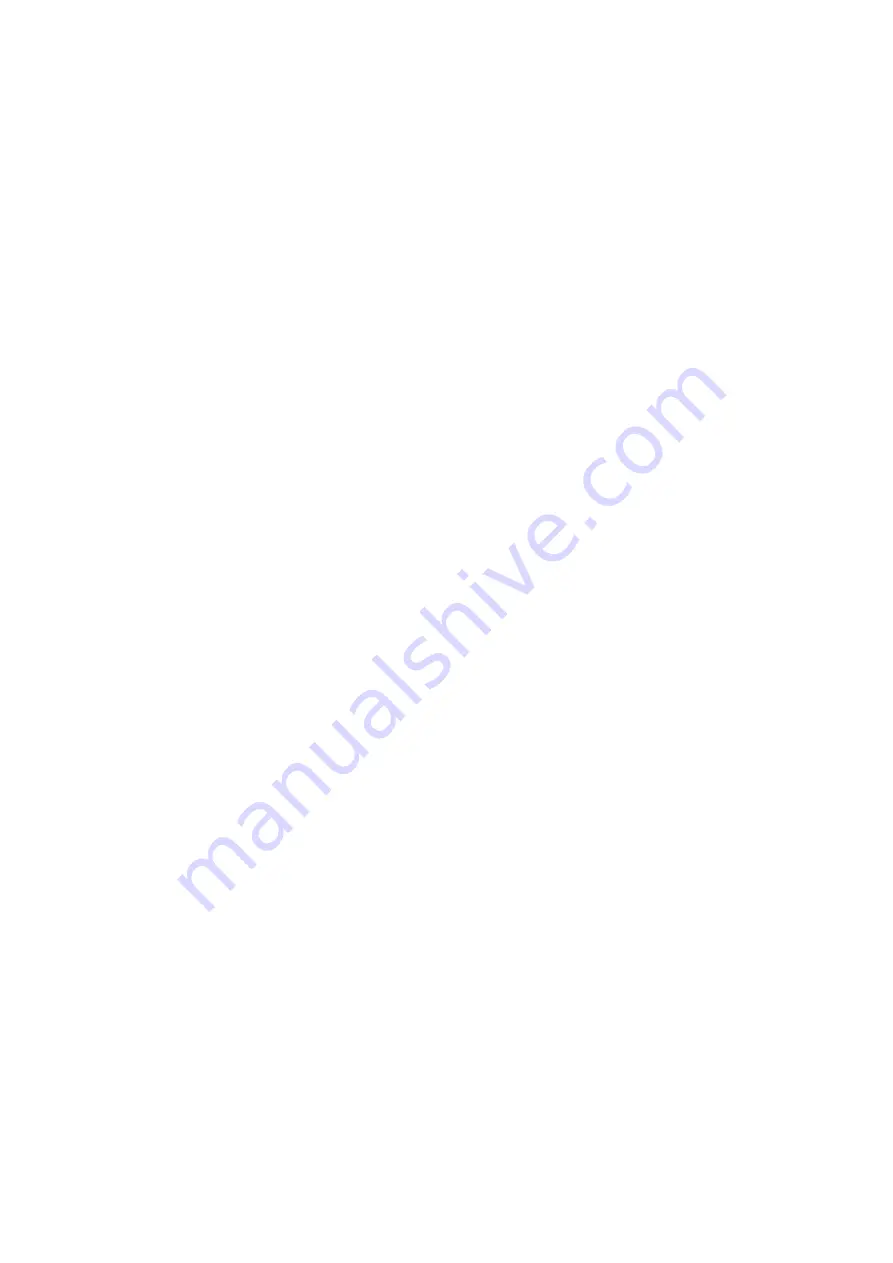
GENERAL INSTRUCTIONS
Please read this section carefully, especially if this is your first etched brass kit. Many modellers
fight shy of working in this medium, but the basic skills are relatively easy to acquire. Once
you’ve learned how to form and solder brass, you’ll find all kinds of modelling possibilities will
open up for you.
Assembling an etched kit involves exactly the same skills that a scratchbuilder uses – the only
difference is that the cutting out of the parts is already done for you. Some filing and trimming
will, however, be necessary from time to time. Where this is the case, I have highlighted it in the
instructions.
The main skill to master is soldering and I would recommend a Weller 40 Watt soldering iron.
This has a 6mm diameter, removable copper bit. The bit is shaped like a screwdriver and has a
bright coating of solder (tinned). This combination of iron and bit shape is ideal for running fillet
joints and has a good reserve of heat, that is necessary for soldering small parts on to large
components. Note the shape and condition of a new bit, as this won’t last long and will need
restoring back to this condition.
It is important to keep the bit clean and in good condition as you work. Get a soldering iron
stand containing a damp sponge; old oxidized solder is wiped off on this before picking up fresh
solder for each joint. If you haven’t made a joint for some time you may find that a hard black
crust has formed on the bit. Remove this with a brass wire brush (suede brush) and then feed
some multicore solder onto each side of the bit to restore a bright surface (referred to as wetting
or tinning the bit). After about 8 hours use you will find the bit is in poor condition, with holes and
a ragged edge. File the bit back to its original shape using a hand bastard file and then polish the
surfaces on emery cloth. Coat the bit with Fluxite Soldering Paste (traditionally used by
plumbers) and this will prevent the bare copper oxidizing as the iron heats up. Then feed
multicore solder onto the bit to form a generous coating and leave to bubble away for a couple of
minutes before wiping excess off to give a bit almost as good as new.
A smaller Antex 25 Watt iron with a 3.2mm screwdriver bit is very useful for small assemblies
and detail work such as handrails, but will have insufficient heat reserve for main assembly work.
The Antex has a plated iron bit, after a little use with 145° solder a grey oxide appears on the bit
that will prevent you from picking up the solder. Touch the bit to some multicore solder and it will
flash over the bit, wetting it so that you can continue picking up 145° solder. I have found no
problems with mixing the two solders in this way.
I use 145° solder for virtually all assembly work. I prefer it in wire form, available from
Branchlines, but it is also produced in stick form by Carrs. I find that its lower working
temperature helps to give a quick clean joint. Limiting the build up of heat in components, which
may cause distortion. I find that I can hold parts together with my finger ends and make a joint
before heat reaches my fingers or other etched parts drop off.
I use 60/40, tin/lead, fluxed multicore electrical solder (melting point about 190°) mainly to keep
the iron bits in good condition. As it gives a slightly stronger joint than 145° I sometimes use it for
small spot joints on handrail wire, lamp brackets etc, but still use extra liquid flux.
For all brass and nickel silver work I use Carrs green label liquid flux. You will soon get the feel
for how much to use but more problems are caused by too little flux than too much.
Before soldering components together, thoroughly clean both surfaces along the join line with a
glass fibre burnishing brush. Using your tweezers or a knife blade etc, hold the parts together in
the correct position and, with an old paintbrush, run some flux along the area to be joined. Still
keeping the parts correctly aligned, pick up a small quantity of solder on the tip of your iron and
carry it to the joint (unlike electrical soldering, when you feed solder into the joint). Hold the iron
against the joint just long enough for the solder to flash between the parts. Don’t let go of the
parts until the solder has cooled – this takes from five to ten seconds. To run a fillet of solder
along a joint, wait until the solder flashes between the parts and then pull the molten solder along
Page 2
Содержание GWR TOAD Diagram AA7
Страница 12: ...Page 12 ...
Страница 13: ...Page 13 ...