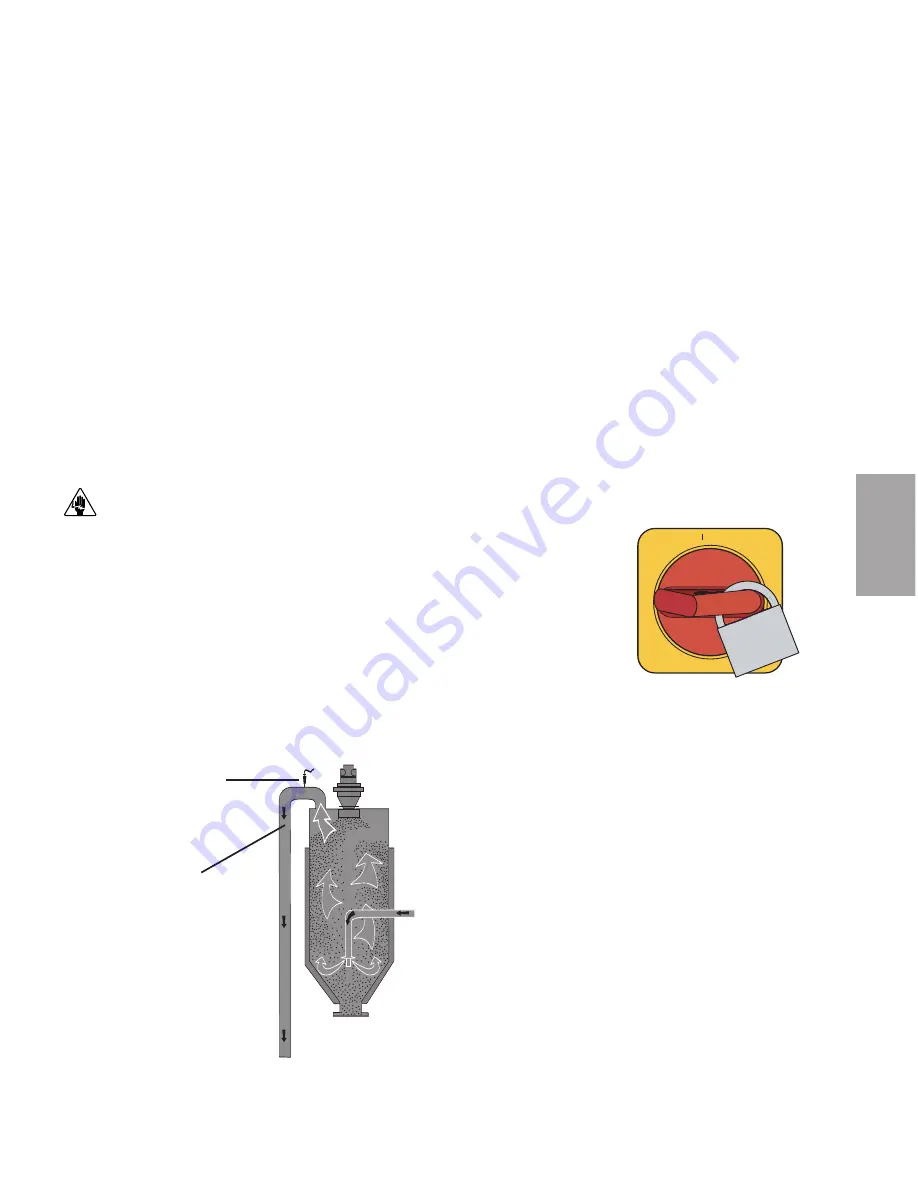
3
Description
I n s t a l l a t i o n l
3 - 1 3
C o n n e c t i n g t h e R T D S e n s o r s
( c o n t i n u e d )
3
Route the process protection RTD cable to the control center. Plug the con-
nector into the receptacle in the side of the control center labeled “Protection”.
Hand tighten the connector. Coil any excess cable and secure it with a wire tie.
Process Setback RTD Probe (Optional)
The optional process setback RTD probe is a sensor in the outlet of the hopper and
is normally supplied with a closed loop dehumidifying dryer system. The purpose
of the setback option is to reduce the energy consumption and prevent over drying
when material stops flowing through the hopper.
CAUTION:
Always disconnect and lock out the main power sources before mak-
ing electrical connections. Electrical connections should be made only by quali-
fied personnel.
1
Turn the disconnect dial on the control center door to the Off or O posi-
tion. Lock out the main power (see Page 1-5 for complete lock out informa-
tion).
2
Insert the process setback RTD probe into the hopper outlet. Center the end
of the probe in the process air outlet of the hopper so that the tip does not touch
the outlet tube walls. Tighten the nuts to lock the RTD probe in place.
ON
O OFF
Typical Hopper
Process
Setback RTD
Location
Process Air
Outlet
(continued)
✐
Note:
If the length of the setback
RTD is too short for your installation,
contact Conair Parts Department
(800.458.1960) to purchase an
extension cable. From outside the
United States, call 814.437.6861.
Содержание Hopper Temperature Controller
Страница 6: ...iv l Table of Contents...
Страница 12: ...1 6 l Introduction...
Страница 20: ...2 8 l Description...
Страница 62: ...4 26 l Operation...
Страница 63: ...Maintenance Preventative maintenance checklist 5 2 S E C T I O N 5 M a i n t e n a n c e 5 Maintenance l 5 1...
Страница 80: ...6 16 l Troubleshooting...