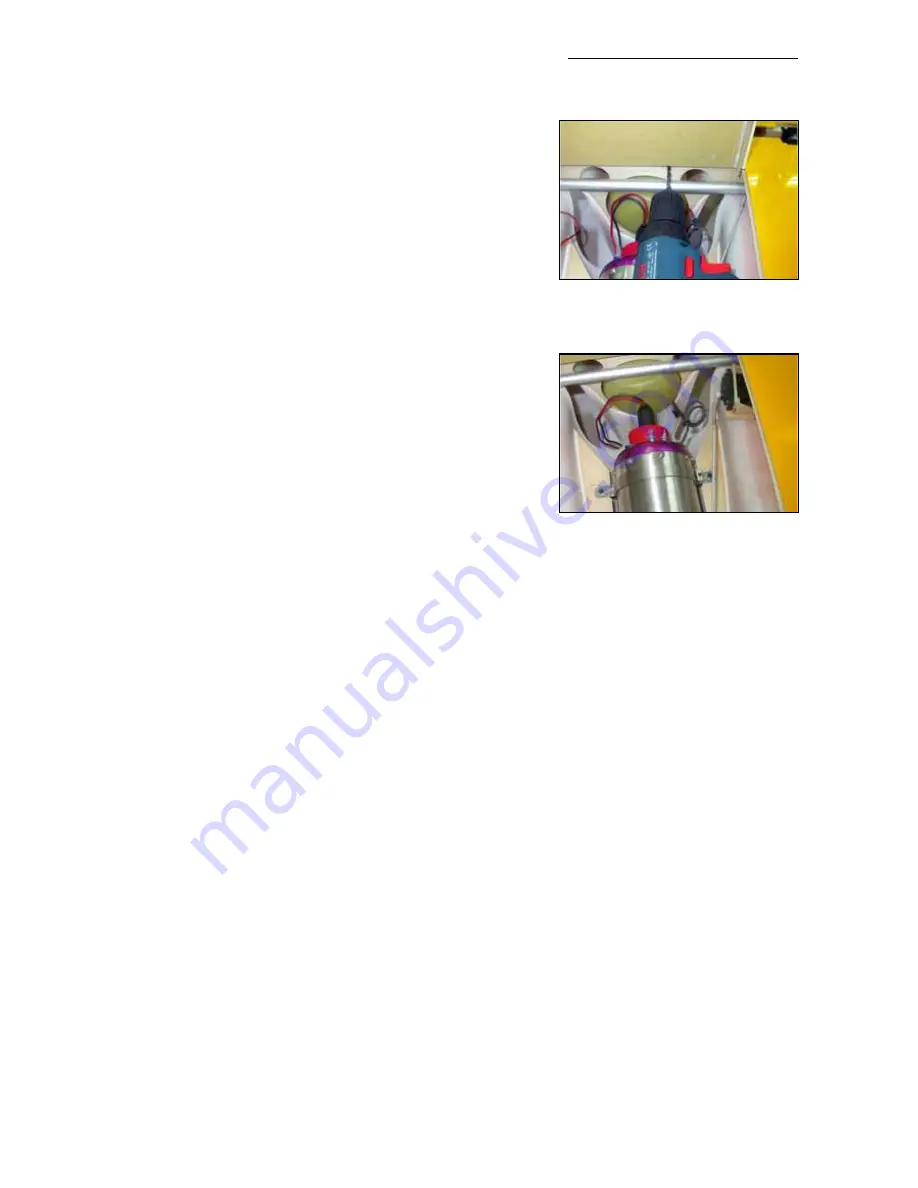
on your turbine you may have to make a shallow bend in the
back end of the M3 rod so that it clears the turbine in the full
deflected position. If needed you can stiffen this linkage by
gluing a length of 4mm brass tube over it.
Servo choice:
The vector nozzle must be controlled by a
powerful servo, and we recommend at least 9kg torque.
Used in this example is a digital JR8411 servo which is
strongly recommended for this control.
The thrust tube is oval in shape, and you can adjust it final-
ly by bending slightly to make it symmetrical behind the tur-
bine nozzle.
Note:
An alternative position for the thrust vectoring servo is
at the side of the turbine behind the plywood bulkhead (see
photo). This position does give a shorter linkage, but you will
need to bend the metal tab on the thrust tube a little to be in
line with the servo arm for steel clevises, as you cannot use
a plastic ball link on the thrust tube because of the temper-
ature.
Engine Installation and Hatch
Turbine installation is very simple with easy access thru’ the large bottom hatch. Mount your
motor using the manufacturers brackets, and bolt onto the plywood siderails, using the sup-
plied M4 bolts and T-nuts underneath the ply rails. Make sure it is straight and in line with the
flying axis of the model, and also the Thrust vector tube. Some brands of turbine have slightly
offset mounting brackets, (eg: JetCat) and in this case you should pack them up off the ply
mounting rails with scrap plywood spacers to get the turbine in the vertical centre of the height
of the opening cut in the back of the plane.
We recommend a turbine with a thrust in the range between 7 - 12kg for the ‘new Rookie. The
photos in this manual show an electric-start AMT Netherlands Mercury HP.
As this is an ‘open’ engine installation, rather than a fully-enclosed type, be very careful to
securely fix all the cables and tubes that go to your motor, as well as the rudder servo cables
so that they cannot be sucked into the engine.
The large hatch is already cut loose for you in the factory, and only needs the plywood stiffen-
ers to be glued to it, the 0.8mm plywood lip added around the opening and 2 hatch catches to
secure it. First add a small (3 - 4mm wide) lip around both sides and the back edge of the
hatch opening, cut from the 0.8mm plywood strips supplied. Sand the underside of the fuse-
lage around the opening first, and then glue in place with thin CA. (see photo P4 and P8)
The 2 slightly curved plywood rails should be glued to the inside of the hatch, about 10 -12mm
in from the edges, with the radiused end at the front. Use 30 minute epoxy and micro-balloons
mix for this, and tape the hatch in the closed position while the glue dries - otherwise you can
be sure that the shape of the hatch won’t fit the fuselage shape afterwards! You can apply
some balsa sticks CA’d onto strips of paper tape while the glue dries to make sure the shape
stays perfect if you wish. (see photo P10)
Composite-ARF New Rookie
9
(above) This is an alternative posi-
tion of Vector Thrust system servo.
(above) Drill a 8mm Ø hole thru’
the rear bulkhead for the thrust
vector linkage as shown.