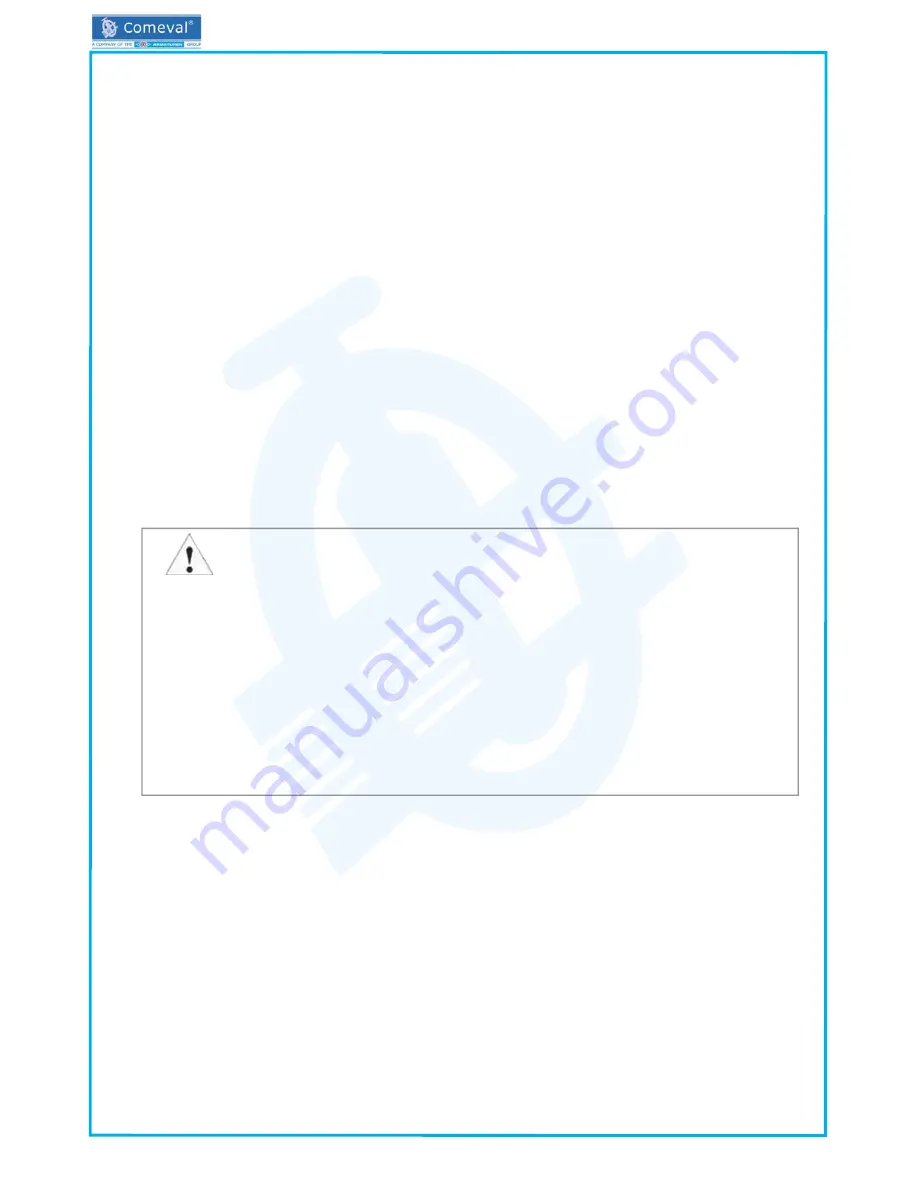
IOM -
SELF-ACTING DIAPHRAGM VALVES
MAXOMATIC VMXBERL24C
©COMEV
AL
V
A
L
VE SYSTEMS
T
echnical Dept. Ref. IOM-SELF-ACTING DIAPHRAGM V
A
L
VES, MAXOMA
TIC VMXBXERL24C-Ed.15/05
Comeval V
alve Systems reserves the right to alter any technical data contained in this Manual without prior notice. Regularly u
pdated data on www
.comeval.es
- Ensure valve surface is in good condition and retouch coating protection when needed.
- The fi lling, warming-up and starting-up of the system shall be gradual so as to avoid any inadmissible stress. Check for
tightness in valve connections, body/cover union and Pilot circuit body/bonnet union, and stem, and retighten crosswise
and gradually if necessary until leakage elimination. If leakage persists, unions should be inspected, surfaces should be
thoroughly cleaned and new gaskets correctly placed.
- Ensure the existence of gauges or pressure transmitters in good condition to register the pressure.
- Check the Pilot circuit according to given layout.
- Check the correct wiring of the Solenoid Valves and the tightness of their connectors.
- Operate gradually and wait enough time for the reaction of the system to avoid inadmissible stress or water hammers.
- The Main Valve is fi rst isolated from the rest of the system by means of the upstream and downstream isolation valves.
- Open slowly the upstream isolation valve so that the fl uid fi lls up the Main Valve and its circuit.
- Eliminate the air trapped in the top parts of the circuit by loosening the connections.
- Discard blocking or leakage in the Pilot piping.
- Open fully the upstream isolation valve.
- Ensure the Pilot adjusting screw is nearly loosen.
- Open slowly the downstream isolation valve, pressure should remain steady after a few seconds of fl uctuations.
- Set the preset downstream pressure by slowly turning clockwise the adjusting screw (fi rstly loosen its adjusting screw
nut) until reaching the desired value.
- After having set the Pilot, and checked the pressure in the gauge, wait as long as necessary for the system to balance
and make another reading, if necessary repeat the same procedure.
- After fi nishing the adjusting process, tighten back the adjusting screw nut.
- Once the valve installed, make an initial opening and closing operation to check its proper operability.
7. – CARE AND MAINTENANCE
The operator must defi ne maintenance and maintenance-intervals to meet requirements.
- Check for body and seat tightness and valve smooth operation without additional tools. Discard obstructions or blocking
in the Pilot system.
- Check the valve surface inside and outside and retouch coating protection when needed. If advanced corrosion or ero-
sion is observed, double check service and valve features and replace the valve properly.
- In case of body/cover leakage, retighten the bolts in a crosswise, moderate and uniform manner. If leakage cannot be
corrected, dismount the cover, clean sealing surfaces and replace the diaphragm when needed.
- It is recommended to open and close the solenoid valves at least once a day, in order to prevent from solenoid stuck
blocking.
- In case of seat leakage, try to close the Main Valve with the Manual Valve of the Pilot system if any to discard damages
or blocking in the Pilot system, and open the valve if possible to drain deposits or impurities trapped. If problem is not
solved, dismount the valve to inspect diaphragm and body seat and replace them when needed.
After any maintenance work please refer to chapters 5 and 6 for installation / commissioning.
Recommended Spare parts:
Use only original spare parts.
The diaphragm is a typical wear component and should be replaced periodically. Bodies, Pilots, Solenoids, manual valves
or strainers can also get damaged during service. Type and number of each spare part to be stored according to many
factors: service level, valves quantity, etc. In many cases a good choice is to keep complete valves as spare part.
Page 6
ATTENTION!
- In the event of infrequent use, operate the valve as frequently as possible to avoid deposits of dirt and valve
blocking. After long period without use of 4-way manual valve, remove the lever by losening the fi xing screw and
operate with a wrench in case of too much resistance to turn. Then place the lever back taking into account its
relative position
- When using the valve as an end seal, the employers’ liability insurance association specifi es the use of a safety
precaution such as a plug-in disc, blind fl ange, Before starting maintenance work on an end valve with a free stem
end, you must mount a blind fl ange.
- Before disassembling the valve, note chapters 10 & 11.
- When the valve is operated, there is a crushing hazard between the diaphragm and the body.
- Only carry out maintenance work in the pipework when the valve has been secured from operation (in case of
actuator, ensure it has been disconnected from the mains supply and secured from reactivation).
- Check correct position of nameplate and handle with care to avoid personnel cuttings.
- When the valve is operated, there is a crushing hazard between the diaphragm and the body. Ensure the valve
is not under operation in case hands are introduced inside the valve.