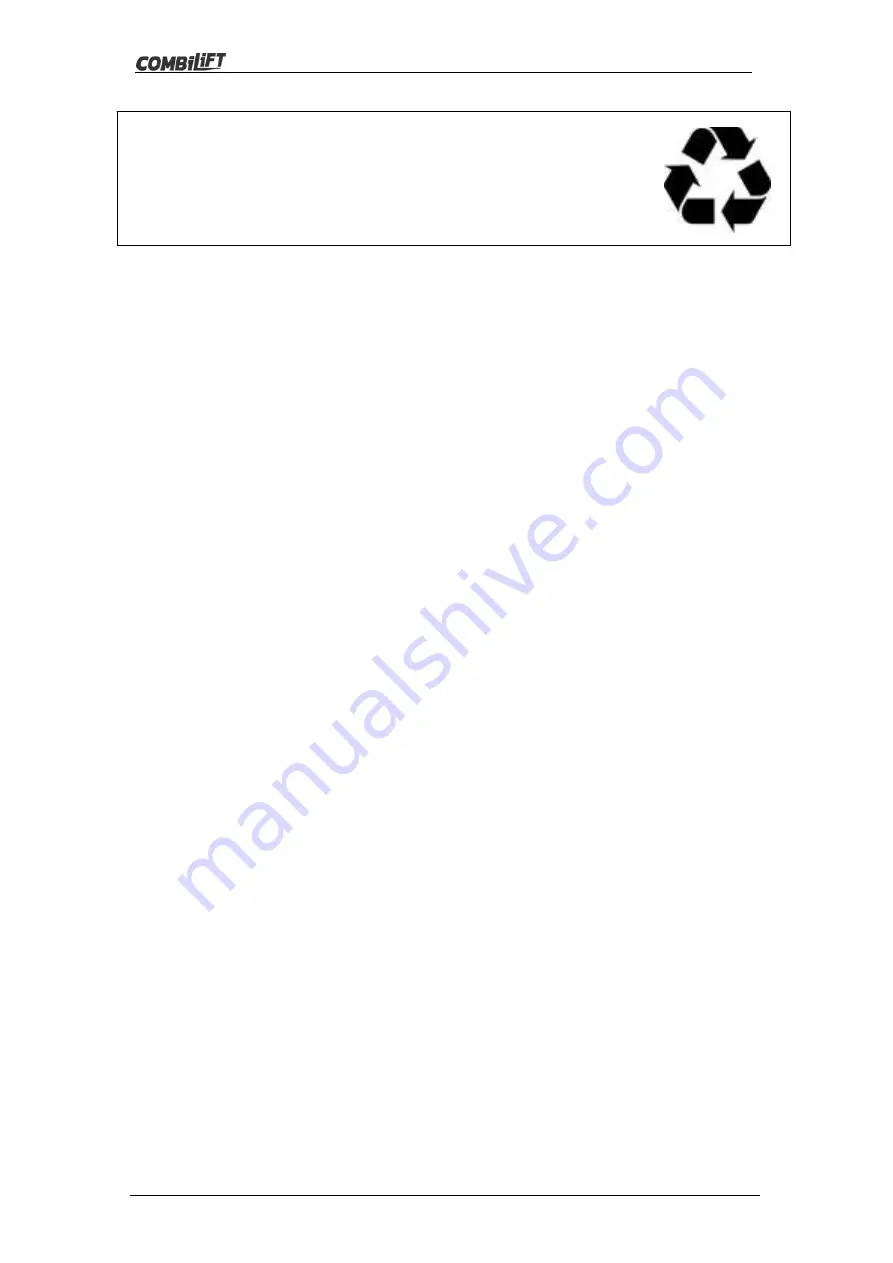
C25000 O&S Manual
40
C25000-OM-EN-05
Note
Do not pour spent fluids into the ground, down a drain or into a
stream, pond or lake. Observe relevant environmental
protection regulations when disposing of oil, coolant, fuel,
electrolyte and other harmful waste.
Return Filter:
(service Interval = 500 Hours)
The return filter, located on the top of the tank, must be replaced at intervals of
every 500 hours.
To replace the Return Filter:
1. Depressurise the system and clean the filter housing.
2. Loosen but do not remove the four bolts on the cover of the filter
housing.
3. Push down on the cover and turn clockwise to remove.
4. Remove the old filter element from the bowl using the handle on top of
the filter element.
5. Lubricate the seal on the new filter element with the operating fluid and
push the new filter element into the bowl. Only use a genuine Combilift
component.
6. Refit the housing lid by pushing onto the filter housing and turning
anticlockwise up to bolts.
7. Tighten the four bolts onto the housing lid.
Hydraulic Oil & In-Tank Strainer Filters:
(Service Interval = 2000 Hours)
The hydraulic oil and strainer filters located inside the hydraulic tank, must be
replaced at intervals of every 2000 hours (or 24 months depending on which
occurs first). The strainer filters can only be accessed when the hydraulic tank
has been drained.
To replace the Hydraulic Oil & In-Tank Strainer Filters:
1. Drain the hydraulic oil tank through the drain plug in the bottom of the
tank. Collect the oil in a suitable container.
2. Clean the tank then remove the access panel on the back of the tank.
3. Insert your hand into the tank and remove the filters by rotating anti-
clockwise.
4. Fit the new strainer filters. Only use a genuine Combilift components.
5. Refit the access panel to the front of the tank, remembering to correctly
fit a new O-ring seal.
6. Fill the tank to half way up the sight glass on the hydraulic oil gauge
with hydraulic oil of the same grade as the oil that was drained from the
tank.
7. Operate the truck for a short period the check the oil level. Top up the
tank to half way up the sight glass if necessary.
Volume of oil required to fill tank to half way up the gauge sight glass:
200 litres / 211 quarts