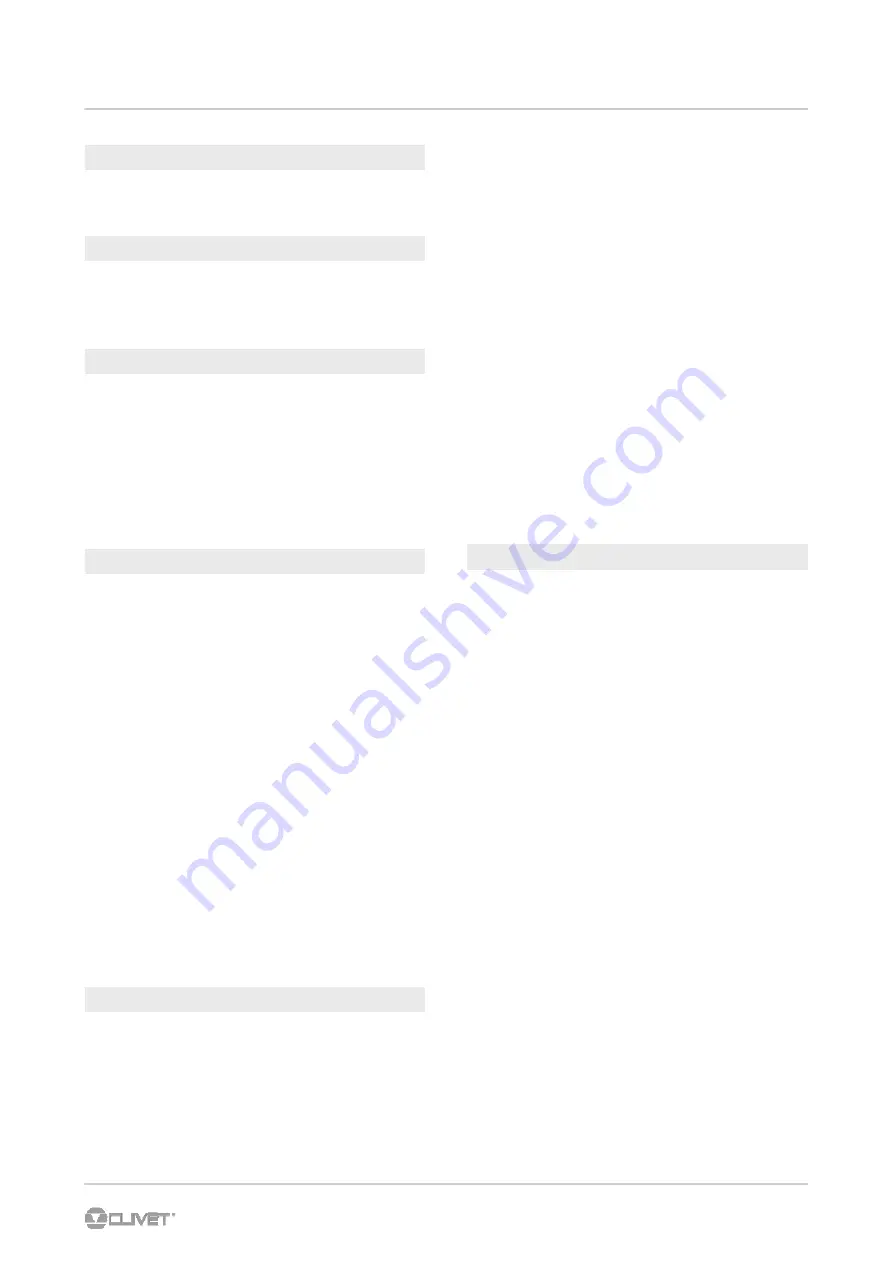
54
11 - RESIDUAL RISKS
Smell of burning, smoke or other signals of serious anomalies
may indicate a situation which could cause damage to people,
things or the unit itself.
Electrically isolate the unit (yellow-red isolator).
Contact the authorised service centre to identify and resolve
the problem at the source of the anomaly.
Accidental contact with exchange batteries, compressors, air
delivery tubes or other components may cause injuries and/or
burns.
Always wear suitable clothing including protective gloves to
work inside the danger zone.
Maintenance and repair operations carried out by non-
qualified personnel may cause damge to persons, things or
the unit itself.
Always contact the qualified assistance centre.
Failing to close the unit panels or failure to check the correct
tightening of all of the panelling fixing screws may cause
damage to persons, things or the unit itself.
Periodically check that all of the panels are correctly closed
and fixed.
If there is a fire the temperature of the refrigerant could reach
values that increase the pressure to beyond the safety valve
with the consequent possible projection of the refrigerant itself
or explosion of the circuit parts that remain isolated by the
closure of the tap.
Do not remain in the vicinity of the safety valve and never
leave the refrigerating system taps closed.
11.1 GENERAL
11.2 DANGER ZONE
11.3 HANDLING
11.4 INSTALLATION
11.5 GENERAL RISKS
11.6 ELECTRICS PARTS
In this section the most common situations are signalled. As
these cannot be controlled by the manufacturer these could
be a source of risk situations for people or things
This is an area in which only an authorised operator may work.
The danger zone is the area inside the unit which is accessible
only with the deliberate removal of protections or parts thereof
The handling operations, if implemented without all of the
protection necesssary and without due caution, may cause
the fall or the tipping of the unit with the consequent damage,
even serious, to persons, things or the unit itself.
Handle the unit following the instructions provided in the pre-
sent manual regarding the packaging and in compliance with
the local regulations in force.
Should the gas refrigerant leak please refer to the refrigerant
"Safety sheet".
An incorrect installation of the unit could cause water leaks,
condensate accumulation, leaking of the refrigerant, electric
shock, bad functioning or damage to the unit itself.
Check that the installation has been implemented by qualified
technical personnel only and that the instructions contained in
the present manual and the local regulations in force have
been adhered to.
The installation of the unit in a place where even infrequent
leaks of inflammable gas and the accumulation of this gas in
the area surrounding the area occur could cause explosions
or fires.
Carefully check the positioning of the unit.
The installation of the unit in a place unsuited to support its
weight and/or guarantee adequate anchorage may cause the
fall or the tipping of the unit with the consequent damage to
things, people or the unit itself.
Carefully check the positioning and the anchoring of the unit.
Easy access to the unit by children, unauthorised persons or
animals may be the source of accidents, some serious.
Install the unit in areas which are only accessible to authori-
sed person and/or provide protection against intrusion into the
danger zone .
An incomplete attachment line to the electric network or with
incorrectly sized cables and/or unsuitable protective devices
can cause electric shocks, intoxication, damage to the unit or
fires.
Carry out all of the work on the electric system referring to the
electric layout and the present manual ensuring the use of a
system thereto dedicated.
An incorrect fixing of the electric components cover may
favour the entry of dust, water etc inside and may
consequently can electric shocks, damage to the unit or fires.
Always fix the unit cover properly.
When the metallic mass of the unit is under voltage and is not
correctly connected to the earthing system it may be as
source of electric shock and electrocution.
Always pay particular attention to the implementation of the
earthing system connections.
Contact with parts under voltage accessible inside the unit
after the removal of the guards can cause electric shocks,
burns and electrocution.
Open and padlock the general isolator prior to removing the
guards and signal work in progress with the appropriate
shield.
Contact with parts that could be under voltage due to the start
up of the unit may cause electric shocks, burns and
electrocution.
When voltage is necessary for the circuit open the isolator on
the attachment line of the unit itself, padlock it and display the
appropriate warning shield.
Содержание WSAN-XIN 21
Страница 44: ...44 8 MAINTENANCE SPARE PARTS SIZES 21 31 41 ...
Страница 46: ...46 8 MAINTENANCE SPARE PARTS SIZES 51 71 ...
Страница 55: ...55 NOTES ...