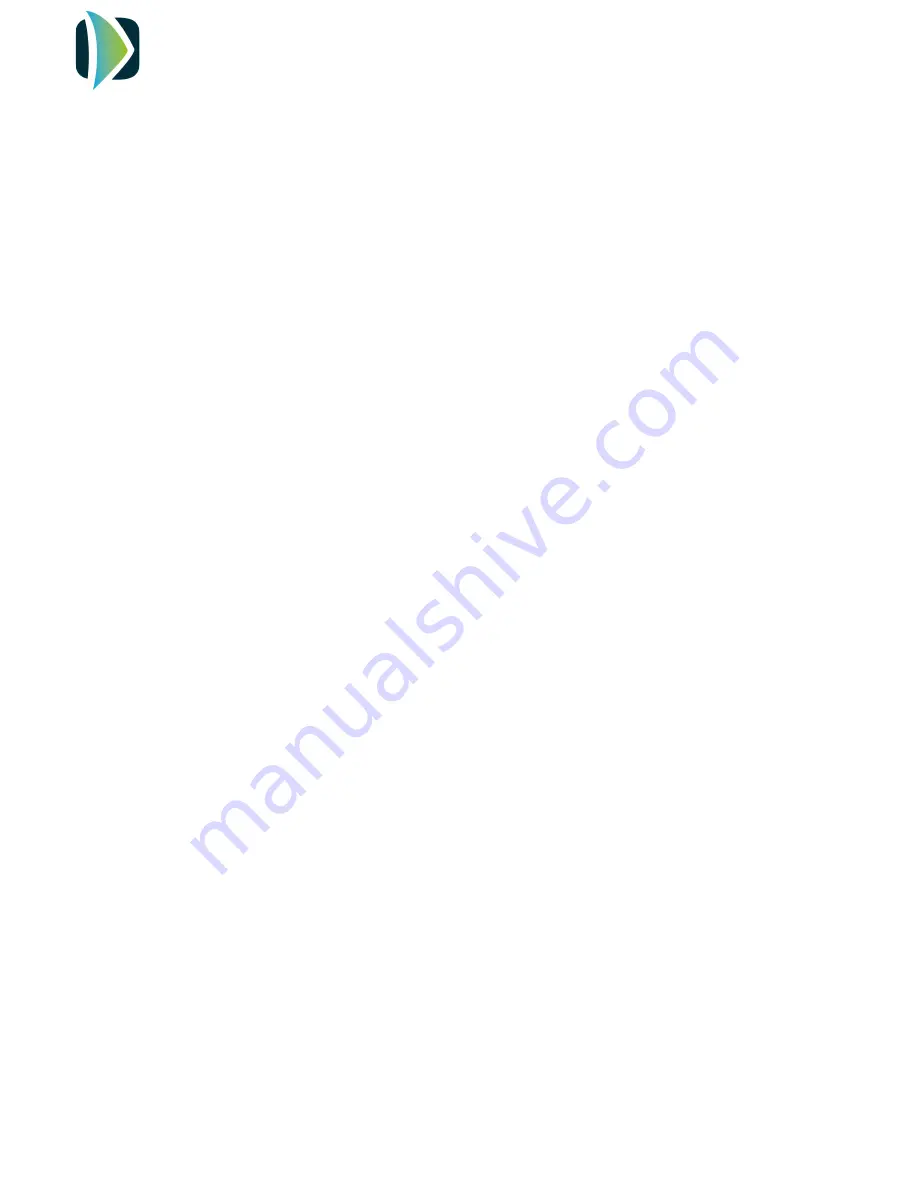
INSTALLATION AND USER MANUAL
HTM-24E
6
V0REV5ES1218
4.
INSTALLATION STEPS
Before starting the installation, check the availability of all the necessary components and
tools:
-
High and low pressure manometers
-
Vacuum pump
-
Scales
-
Coolant bottle (R407C depending on the model)
-
Nitrogen bottle
-
Refrigerant quality copper pipe
-
Pipe-cutter
-
Tube bender
-
Pipe expander
-
Welder
-
Copper Rods (40% Siver)
-
Insulating hose
-
Drill
-
Screwdriver
-
Hydraulic installation components
-
Electric installation components
Once it has been checked that it is available all the necessary components and tools, the
installer should follow the next steps:
1.
Placing and anchoring panels
2.
Installation of the liquid distributors
3.
Installation of the gas manifold
4.
Joining and welding the refrigerant pipes
5.
Placing the Heating Module
6.
Joining and welding liquid and suction line between heating module and panels.
7.
Nitrogen pressure test (maximum10 bar)
8.
Vacuum
Содержание HTM EVI SERIES
Страница 1: ...1 V0REV5ES1218 INSTALLATION AND USER MANUAL HTM EVI SERIES ...
Страница 2: ...INSTALLATION AND USER MANUAL HTM 24E 2 V0REV5ES1218 ...
Страница 21: ...INSTALLATION AND USER MANUAL HTM 24E 21 V0REV5ES1218 12 ANNEX HYDRAULIC SCHEME ...
Страница 22: ...22 V0REV5ES1218 ELECTRICAL DIAGRAM THREE PHASE UNITS ...
Страница 24: ...INSTALLATION AND USER MANUAL HTM 24E 24 V0REV5ES1218 ELECTRONIC EXPANSION VALVE DIAGRAM ...