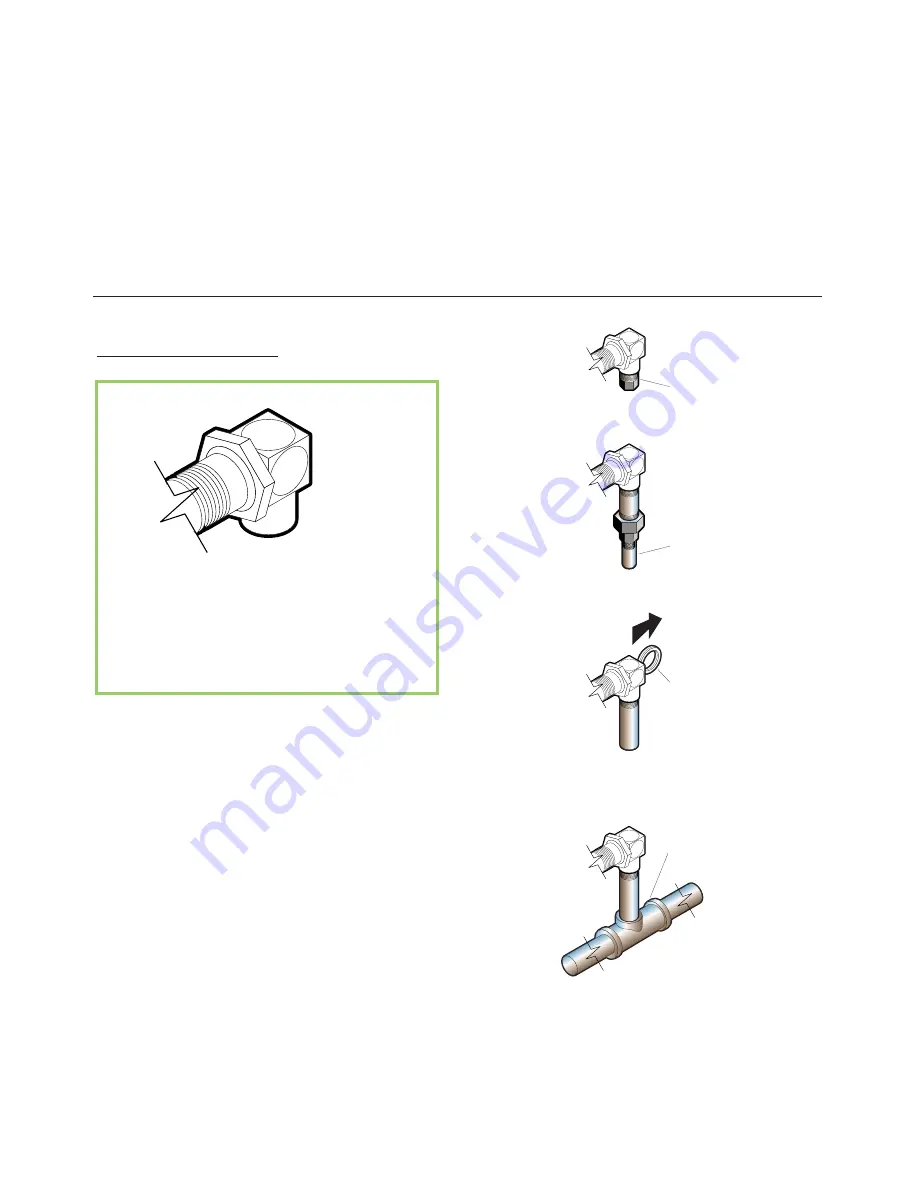
20
SAFETY INSPECTION CHECKLIST
-
TILTING MODELS (pg. 1 of 2)
Regular inspection and maintenance of units is essential to obtain trouble free and safe operation of
equipment. Inspections must include testing of the pressure relief valve and checks of the operating
system to insure that it has not been altered.
No safety features designed into the equipment should ever be tampered with
.
Tampering with or bypassing controls is a very dangerous practice and unfortunately we have seen several
cases of this. Following is a short list of the most common and the most dangerous alterations performed
on kettles.
✘
Plug
✘
Tube
diameter
reduced
✘
Frozen,
stuck, or
plugged
✘
Plumbed to
drain or
water line
1
2
3
4
✔
Incorrect Installations
1
Safety valve has plug threaded into the
discharge opening preventing any steam from
escaping.
2
Safety valve’s tube diameter has been
reduced.
3
Safety valve is sticking, frozen shut or plugged.
To test, refer to page 23, PRESSURE RELIEF
VALVE PERIODIC TESTING PROCEDURE.
4
Safety valve is plumbed to a drain or water
line creating back pressure and reducing flow.
SAFETY VALVE:
This illustrations show the correct configuration
of a factory installed Safety Valves.
Any modifications are unacceptable.
This illustrations show the correct configuration of a factory installed Safety Valves.
Any modifications are unacceptable.