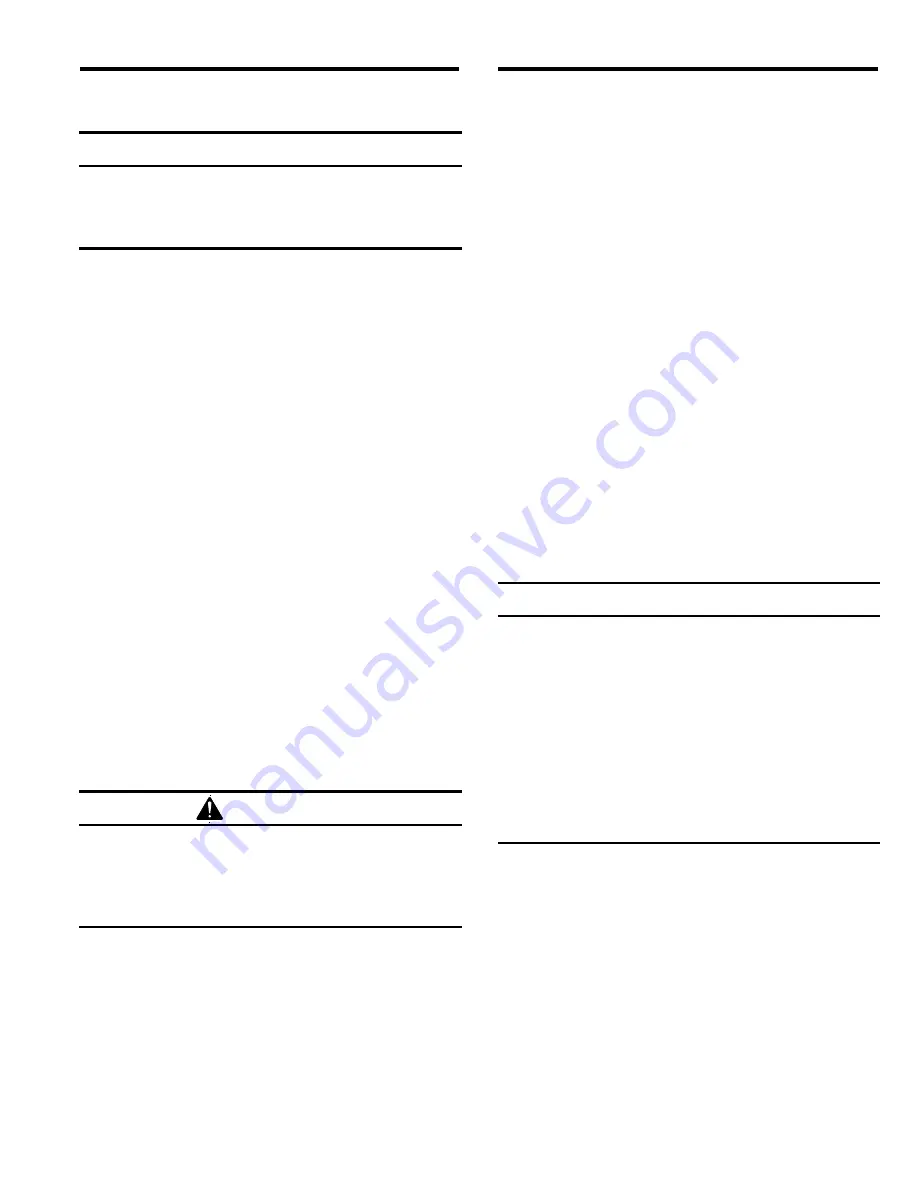
RPH DUST COLLECTOR
Page 3
2.2 Assembly
CAUTION
All seams assembled on the job site must be
sealed to weather-tight condition. Use mastic
tape and caulking on all seams as shown on the
assembly drawings.
2.2.1
The degree of assembly depends on the size and
style of the collector. There may be exceptions; but they
are usually as follows:
• RPH-2, RPH-3, RPH-6 & RPH-8: Factory assembled,
each requires locating and anchoring to a sound footing,
and assembly of the exhauster and ducting.
• RPH-4, RPH-10, RPH-12, & RPH-16: Requires field
assembly of the leg/hopper assembly and body, and
assembly of the exhauster and ducting. It must be located
and anchored to a sound footing.
• RPH-20 and larger: Requires field erection of the
structural leg and frame assembly, assembly of the hopper
and body, ladder, hand rail, exhauster and ducting. It must
be located and anchored to a sound footing.
2.2.2
Erect the collector as shown in the enclosed
assembly drawings. Pay special attention to the orientation
of the inlet and outlet duct openings, access doors, ladder,
handrail, and exhauster location. If the collector is part of a
facility, use the general arrangement drawings for the
placement of the components.
2.3 Anchors
WARNING
All anchors must be calculated and specified by
a qualified engineer. Inadequate anchoring to
the footing could result in hazardous shifting of
the collector and ducting, which could result in
death or serious injury.
2.3.1
Anchor modules to the footing with anchors
specified by a qualified engineer.
2.4 Exhauster
Assembly
NOTE: 3600 cfm and larger exhausters are floor mounted,
and require ducting from the collector, and an exhaust
stack with a damper adjustable from 0-80% closed.
Smaller exhausters are mounted on the collector body,
and do not require additional ducting.
2.4.1
Anchor the exhauster in position. NOTE:
Positioning of the exhauster must coincide with the
placement of the outlet ducting. Use temporary anchors
until the ducting is in place.
2.4.2
Attach exhaust stack and damper assembly to the
exhauster outlet.
2.5 Ducting
2.5.1
Clemco Industries Corp. does not usually supply
ducting, but does provide a general arrangement drawing
for suggested ducting.
2.5.2
The illustration in Figure 2 shows a typical ducting
and exhauster arrangement. The illustration is not to be
used to fabricate ducting.
CAUTION
All ducts, joints, and connections must be tight.
Any leaks will affect the overall performance of
the system.
The joint between the duct and exhauster
housing must be flexible, such as canvas or
rubber with band clamps. The ducting must be
self supporting. NO LOAD IS TO BE APPLIED TO
THE EXHAUSTER BY THE DUCTING.
Ducting must be supported sufficiently to place
no load on connecting equipment.
2.5.3
All duct work must be performed by qualified
licensed contractors familiar with industrial ventilation
practices, and must conform to local codes. Where state or
local codes conflict with each other or with specifications
by Clemco Industries Corp., the more stringent regulation
shall be followed.