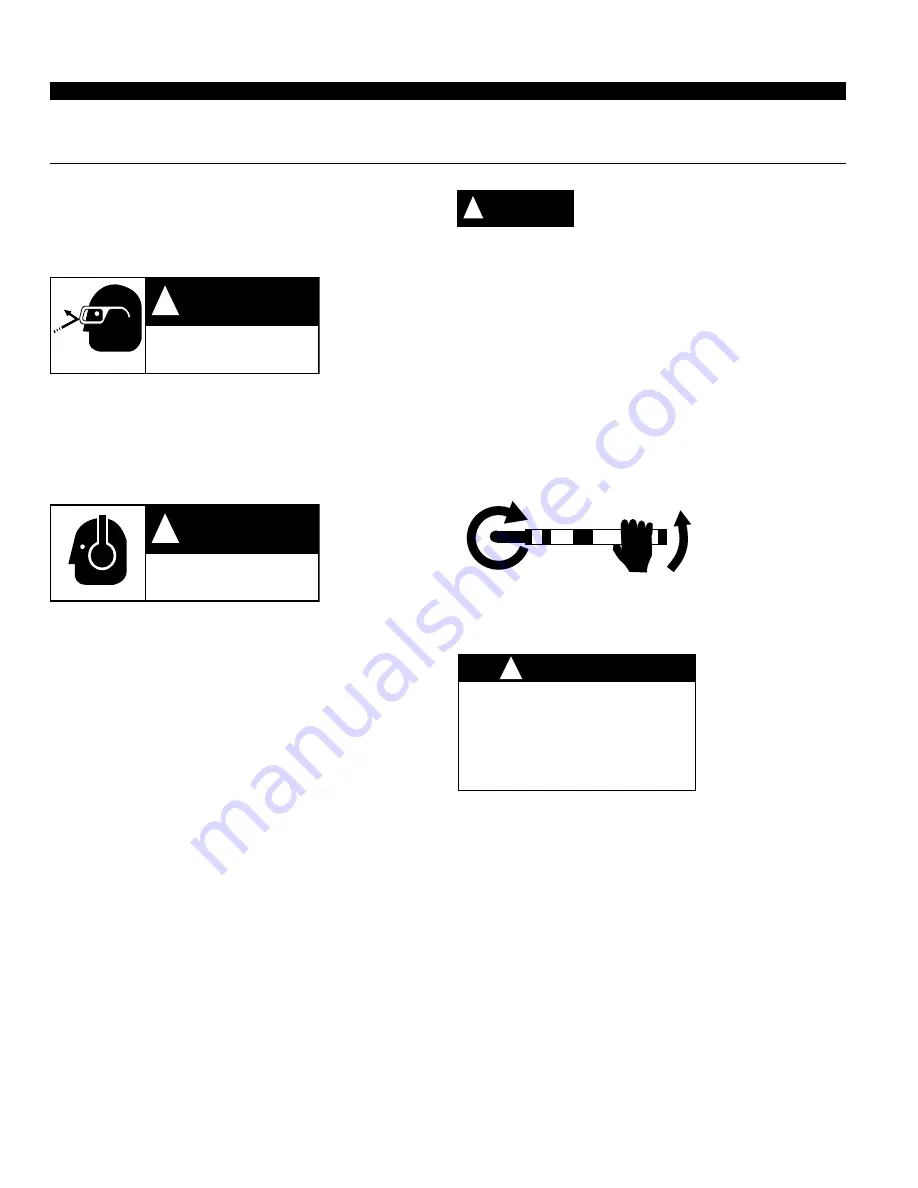
2
Safety Recommendations
For your safety and the safety of others, read and understand the
safety recommendations and operating instructions before operat-
ing a nutrunner.
Always wear protective equipment:
For additional information on eye protection and face protection,
refer to Federal OSHA Regulations, 29 Code of Federal Regula-
tions, Section 1910.133., Eye and Face Protection, and American
National Standards Institute, ANSI Z87.1, Occupational and Edu-
cational Eye and Face Protection. Z87.1 is available from the
American National Standards Institute, Inc., 11 West 42nd Street,
New York, N.Y. 10036.
Hearing protection is recommended in high noise areas 85 dBA or
greater. The operation of other tools and equipment in the area,
reflective surfaces, process noises and resonant structures can
substantially contribute to, and increase the noise level in the area.
Excessive air pressure above 90 PSIG or worn motor components
can also increase sound level emitted by tool. Proper hearing
conservation measures, including annual audiograms and training
in the use and fit of hearing protection devices may be necessary.
For additional information on hearing protection, refer to Federal
Regulations, Section 1910.95, Occupational Noise Exposure, and
American National Standards Institute, ANSI S12.6, Hearing Pro-
tectors.
Cleco nutrunners are designed to operate on 90 psig (6.2 bar)
maximum air pressure. If the tool is properly sized and applied,
higher air pressure is unnecessary. Excessive air pressure in-
creases the loads and stresses on the tool parts, sockets, and
fasteners and may result in breakage. Installation of a filter-
regulator-lubricator in the air supply line ahead of the tool is
recommended.
Before the tool is connected to the air supply, check the throttle for
proper operation (i. e., throttle moves freely and returns to closed
position). Being careful not to endanger adjacent personnel, clear
the air hose of accumulated dust and moisture. Before connecting
a tool to the air hose, removing a tool from service or changing
sockets, make sure the air line is shut off and drained of air. This will
prevent the tool from operating if the throttle is accidently engaged.
CAUTION
!
Personal hearing protection is
recommended when operating
or working near this tool.
WARNING
!
Impact resistant eye protection
must be worn while operating
or working near this tool.
When using right angle nutrunners, be sure the throttle is posi-
tioned relative to the angle head so that the throttle will not become
wedged against an adjacent object in the "ON" position due to
torque reaction. The angle head may be repositioned with respect
to the lever to accommodate proper location for task. If tool is to be
reversed, locate throttle lever in a neutral position that will prevent
entrapment. Refer to operating instructions for additional informa-
tion.
It is essential for safe operation that any operator of a nutrunner use
good balance, sure footing, and proper posture in anticipation of a
torque reaction.
Tools with clutches can stall rather than shut-off if adjusted over
maximum power output of tool, or if there is a drop in air pressure.
Operator must then resist stall torque until throttle is released.
Tool balance arms are available to absorb the torque reaction of the
tool while balancing the weight of the tool for improved ergonomic
applications.
Some individuals may be susceptible to disorders of the hands and
arms when performing tasks consisting of highly repetitive motions
and/or exposure to extended vibration. Cumulative trauma disor-
ders such as carpal tunnel syndrome and tendonitis may be caused
or aggravated by repetitious, forceful exertions of the hands and
arms. Vibration may contribute to a condition called Raynaud's
Syndrome. These disorders develop gradually over periods of
weeks, months, and years. It is presently unknown to what extent
exposure to vibrations or repetitive motions may contribute to the
disorders. Hereditary factors, vasculatory or circulatory problems,
exposure to cold and dampness, diet, smoking and work practices
are thought to contribute to the conditions.
Any tool operator should be aware of the following warning signs
and symptoms so that a problem can be addressed before it
becomes a debilitating injury. Any user suffering prolonged symp-
Spindle Rotation
Torque Reaction
Repetitive work motions and/or vibration
may cause injury to hands and arms.
Use minimum hand grip force consistent
with proper control and safe operation.
Keep body and hands warm and dry.
Avoid anything that inhibits blood circulation.
Avoid continuous vibration exposure.
Keep wrists straight.
WARNING
!
Avoid repeated bending of wrists and hands.
CAUTION
!
Содержание 35 Series
Страница 19: ...19 NOTES ...
Страница 20: ...20 670 Industrial Drive Lexington SC 29072 Phone 803 359 1200 Fax 803 359 2013 ...