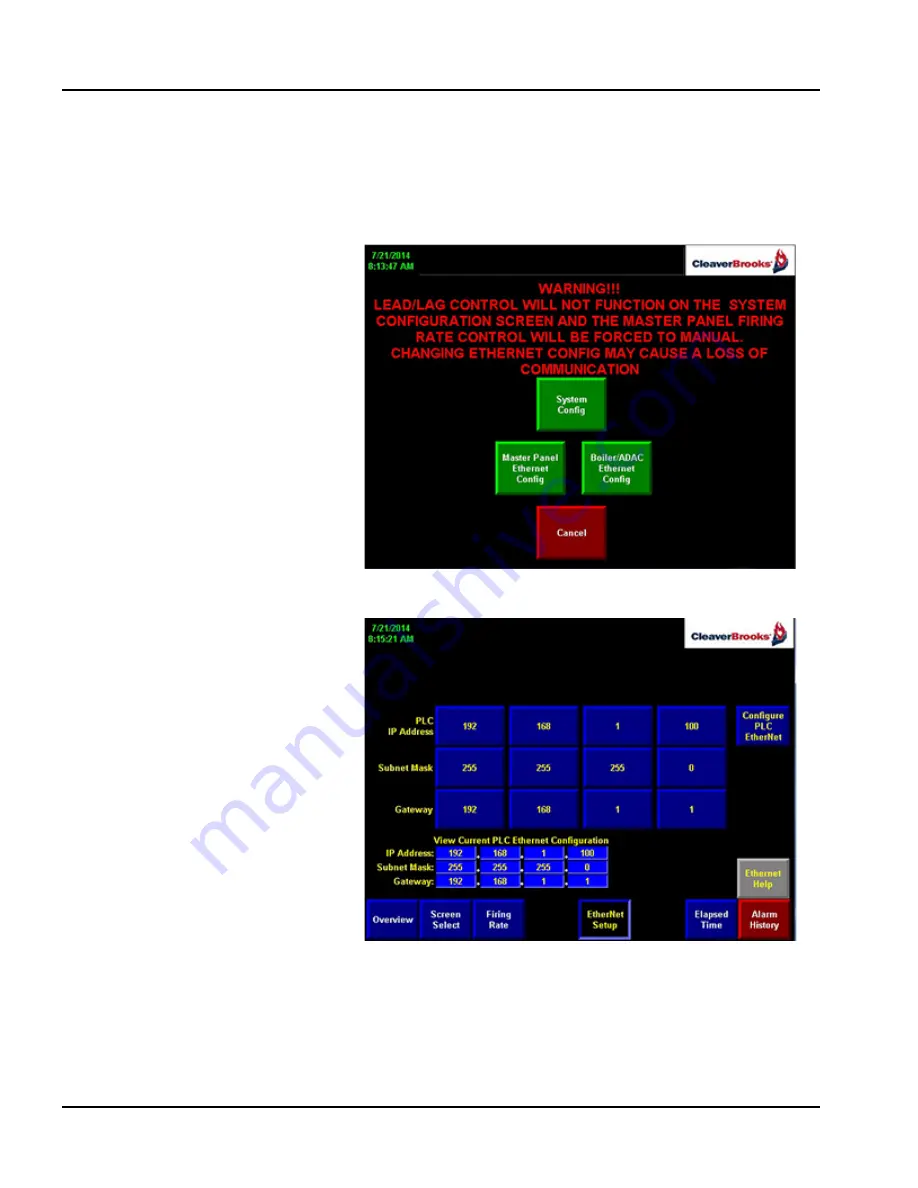
Section 3 — Commissioning
Master Panel 8
3-4
Part No. 750-375
C. I/P ADDRESSING (MASTER PANEL)
To set the Master Panel Ethernet configuration, first go to System
Configuration. Observe the screen warning: Lead/Lag control will not
function while in system configuration and the master panel firing
rate control will be forced to manual. Changing Ethernet settings may
cause a loss of communication.
Press <Master Panel Ethernet Config> for the following screen:
On this screen the IP Address, Subnet Mask, and Gateway are set for
the Master Panel PLC. A help screen is available. When settings are
complete, press <Configure PLC Ethernet> to confirm. This will
bring up the following window:
Содержание Master Panel 8
Страница 1: ...750 375 10 16 Master Panel 8 Eight Boiler Lead Lag Control Operation Manual...
Страница 4: ......
Страница 6: ......
Страница 7: ...www cleaverbrooks com Section 1 Overview A Features 1 2 B Components 1 2 C Specifications 1 4...
Страница 55: ...www cleaverbrooks com Section 5 Parts Master Panel 8 Parts List 5 3...
Страница 56: ...Section 5 Parts Master Panel 8 5 2 Part No 750 375...
Страница 58: ...Section 5 Parts Master Panel 8 5 4 Part No 750 375...
Страница 60: ...e mail info cleaverbrooks com Web Address http www cleaverbrooks com...