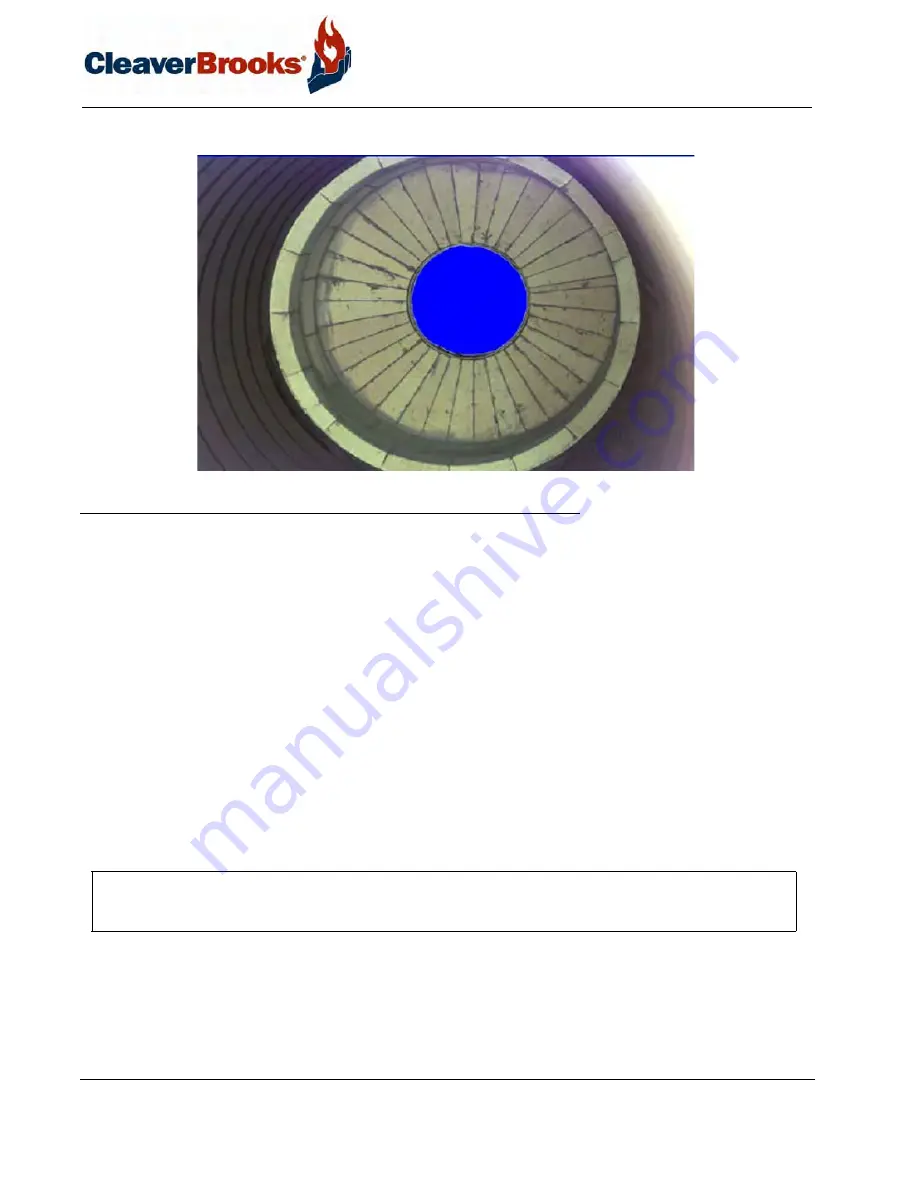
Inspection and Maintenance
8-26
750-91 (revised 2009)
Model CB-LE Packaged Boiler Manual
FIGURE 8-11.
Refractory Liner Tile
8.20.1 — Furnace Liner
Maintenance consists of occasional wash coating of the entire liner. Face all joints or cracks by applying high tem-
perature bonding mortar with a trowel or fingertips. Wash coating should be done as soon as cracks are detected.
Should segments of the liner burn away or fall out, replace the entire refractory. Any refractory that may break out
should be removed as soon as detected so that it will not fuse to the bottom of the furnace and obstruct the flame.
If replacement is necessary, refer to Chapter 9 and order proper replacement materials. Remove existing refractory.
Thoroughly clean the furnace to remove all old refractory cement or other foreign material to ensure the new liner
seats firmly against the steel. Inspect the furnace metal.
Depending upon the design pressure of the boiler, the furnace may be of the corrugated type. It is necessary to fill
in the corrugation valleys under the furnace liner tile from 4 o’clock to 8 o’clock with insulating cement. The liner
tile should be fitted tightly against the crown of the corrugation.
NOTE:
The area between the burner housing and the throat tile requires a good seal. An improper or poor seal allows
air leaks that can cause overheating and burning of the burner housing metal. The area should be inspected semi-annu-
ally. Contact your local Cleaver-Brooks representative for information and service.
Содержание CBLE
Страница 14: ...xiv 750 91 revised 2009 Model CB LE Packaged Boiler Manual...
Страница 48: ...Burner Operation and Control 2 22 750 91 revised 2009 Model CB LE Packaged Boiler Manual...
Страница 64: ...Waterside Care and Requirements 3 16 750 91 revised 2009 Model CB LE Packaged Boiler Manual...
Страница 72: ...Sequence of Operation 4 8 750 91 revised 2009 Model CB LE Packaged Boiler Manual...
Страница 133: ...750 91 revised 2009 Model CB LE Packaged Boiler Manual 8 13 8 12 Forced Draft Fan FIGURE 8 3 Forced Draft Fan Mounting...
Страница 158: ...Inspection and Maintenance 8 38 750 91 revised 2009 Model CB LE Packaged Boiler Manual...
Страница 165: ...750 91 revised 2009 Model CB LE Packaged Boiler Manual 9 7 9 2 Parts Lists and Drawings 9 2 5 Control Panel...
Страница 166: ...Parts 9 8 750 91 revised 2009 Model CB LE Packaged Boiler Manual Control Panel...
Страница 167: ...750 91 revised 2009 Model CB LE Packaged Boiler Manual 9 9 9 2 Parts Lists and Drawings 9 2 6 Entrance Box...
Страница 168: ...Parts 9 10 750 91 revised 2009 Model CB LE Packaged Boiler Manual 9 2 7 Front Head Electrical...
Страница 169: ...750 91 revised 2009 Model CB LE Packaged Boiler Manual 9 11 9 2 Parts Lists and Drawings 9 2 8 Front Davit...
Страница 170: ...Parts 9 12 750 91 revised 2009 Model CB LE Packaged Boiler Manual 9 2 9 Front Head Insulation...
Страница 171: ...750 91 revised 2009 Model CB LE Packaged Boiler Manual 9 13 9 2 Parts Lists and Drawings 9 2 10 Front Head Linkage...
Страница 174: ...Parts 9 16 750 91 revised 2009 Model CB LE Packaged Boiler Manual 9 2 12 Light Oil Air Piping...
Страница 175: ...750 91 revised 2009 Model CB LE Packaged Boiler Manual 9 17 9 2 Parts Lists and Drawings Light Oil Air Piping...
Страница 176: ...Parts 9 18 750 91 revised 2009 Model CB LE Packaged Boiler Manual 9 2 13 Heavy Oil Air Piping...
Страница 177: ...750 91 revised 2009 Model CB LE Packaged Boiler Manual 9 19 9 2 Parts Lists and Drawings Heavy Oil Air Piping...
Страница 178: ...Parts 9 20 750 91 revised 2009 Model CB LE Packaged Boiler Manual 9 2 14 Heavy OIl Alstrom Heater...
Страница 179: ...750 91 revised 2009 Model CB LE Packaged Boiler Manual 9 21 9 2 Parts Lists and Drawings Heavy OIl Alstrom Heater...
Страница 182: ...Parts 9 24 750 91 revised 2009 Model CB LE Packaged Boiler Manual 9 2 16 IFGR Impeller...
Страница 183: ...750 91 revised 2009 Model CB LE Packaged Boiler Manual 9 25 9 2 Parts Lists and Drawings 9 2 17 Pressure Controls...
Страница 184: ...Parts 9 26 750 91 revised 2009 Model CB LE Packaged Boiler Manual 9 2 18 Temperature Controls...
Страница 185: ...750 91 revised 2009 Model CB LE Packaged Boiler Manual 9 27 9 2 Parts Lists and Drawings 9 2 19 W C Main Aux...
Страница 186: ...Parts 9 28 750 91 revised 2009 Model CB LE Packaged Boiler Manual W C Main Aux...
Страница 188: ...Parts 9 30 750 91 revised 2009 Model CB LE Packaged Boiler Manual 9 2 21 Rear Head Sealing Davit...
Страница 193: ......
Страница 194: ...e mail info cleaverbrooks com Web Address http www cleaverbrooks com...