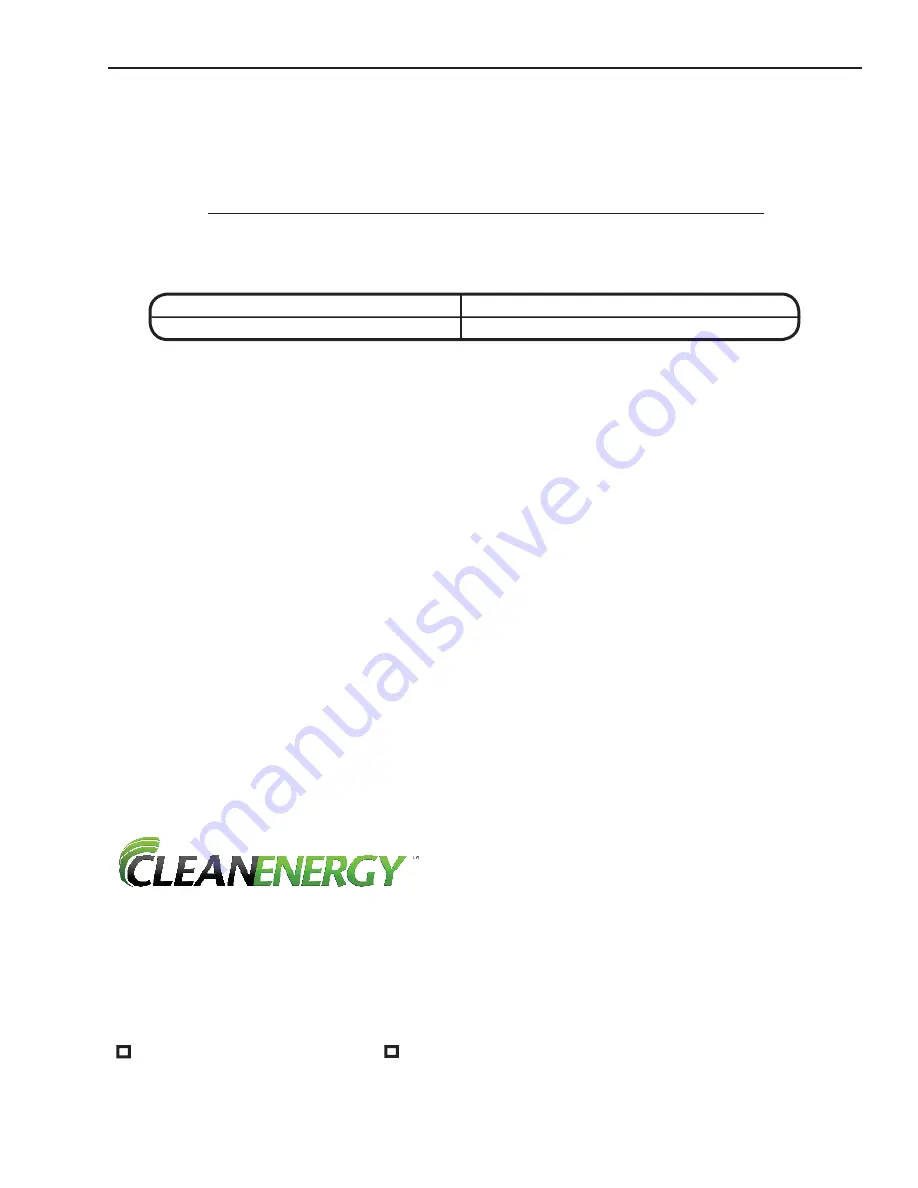
CLEAN ENERGY HEATING SYSTEMS LLC
MODELS: CE-340
Ten Year Combustion Chamber/Heat Exchanger Warranty ONE YEAR Parts Warranty
Clean Energy Heating Systems LLC, MANUFACTURER, hereby warrants the MANUFACTURER’S product to be
free from defects in material and workmanship under normal use and conditions as set forth in the provisions and
limitations below. The warranty extends to the original owner whose name appears on the Warranty Registration
Card returned to MANUFACTURER.
TEN YEAR COMBUSTION CHAMBER / HEAT EXCHANGER WARRANTY
The ten year warranty on the combustion chamber / heat exchanger shall be from the date of purchase
by the original purchaser and shall be subject to the prorated schedule of years listed in the table below
0 to 5 years
Repair or replace FREE of charge
6 to 10 years
Repair or replace shared cost 50/50
All labor and transportation costs are the responsibility of the owner. Repair or replacement shall be
determined by MANUFACTURER. Photos or returned goods at owner’s expense may be required for
warranty determination.
ONE YEAR PARTS WARRANTY
All component parts are covered under warranty for a period of ONE YEAR from the date of purchase.
Owner is responsible for all labor and transportation costs associated with warranty claims.
CONDITIONS AND LIMITATIONS:
A. The owner must complete and return the Warranty Registration Card within thirty (30) days of
purchase to activate Warranty Coverage.
B. The equipment must be fired at rated capacity only with fuels listed on data label.
C. The equipment must be installed, operated, and maintained in accordance with Federal, State, and
Local regulations as well as with all MANUFACTURER’S installation and operating instructions.
D. The equipment must not be installed in any corrosive atmosphere environment.
E. No parts or controls may be modified, altered, or by-passed.
F. MANUFACTURER shall not be responsible for any failure due to an Act of God.
G. MANUFACTURER is not responsible for additions or changes made by a dealer or distributor that
goes beyond the terms of this Limited Warranty.
Clean Energy Heating Systems, LLC assumes no liability for consequent damage of any kind, and by
acceptance of this equipment the purchaser assumes all liability for the consequence of its use or
misuse by the purchaser or others.
-----------------------------------------------------------------------------------------------------------------------------------------
CLEAN
ENERGY
HEATING
SYSTEMS,
LLC
WARRANTY
CARD
(PLEASE PRINT CLEARLY)
FIRST NAME ___________________________ LAST NAME _______________________________
COMPANY NAME ___________________________________________________________________
STREET ____________________ CITY __________________ STATE ______ ZIP CODE ________
TELEPHONE ______________ EMAIL ___________________ DATE OF PURCHASE: __________
BOILER MODEL:
BURNER MODEL:
CE-340
CE-4
BURNER SERIAL NO. ________________
BOILER
SERIAL
NO.
_______________
WITHIN 30 DAYS OF PURCHASE RETURN WARRANTY CARD TO:
CLEAN ENERGY HEATING SYSTEMS LLC
540 MAPLE STREET
HONEY BROOK PA USA 19344
Содержание CE-340
Страница 2: ...7 3 13 Part 70006 Underwriters Laboratories File MH48829 ...
Страница 35: ...BOILER DIMENSIONS 35 57 5 42 5 67 with Burner 34 0 CE70077 50 ...
Страница 40: ...40 1 4 12 6 15 9 10 14 3 2 11 5 13 8 7 Nozzle Adapter Heater Block Assembly ...
Страница 42: ...42 2 5 7 6 4 5 3 12 11 9 8 10 1 CE70058 CE 4 Manifold Block Assembly ...
Страница 44: ...44 26 14 9 23 2 8 7 6 12 20 13 21 19 18 17 16 15 1 5 3 4 10 22 25 11 24 CE70050 Metering Pump Assembly ...
Страница 46: ...46 CE 340 Boiler 25 27 26 28 24 21 22 23 20 14 13 12 11 10 9 8 7 6 5 4 1 2 3 15 16 17 18 CE70101 19 ALT ALT ...