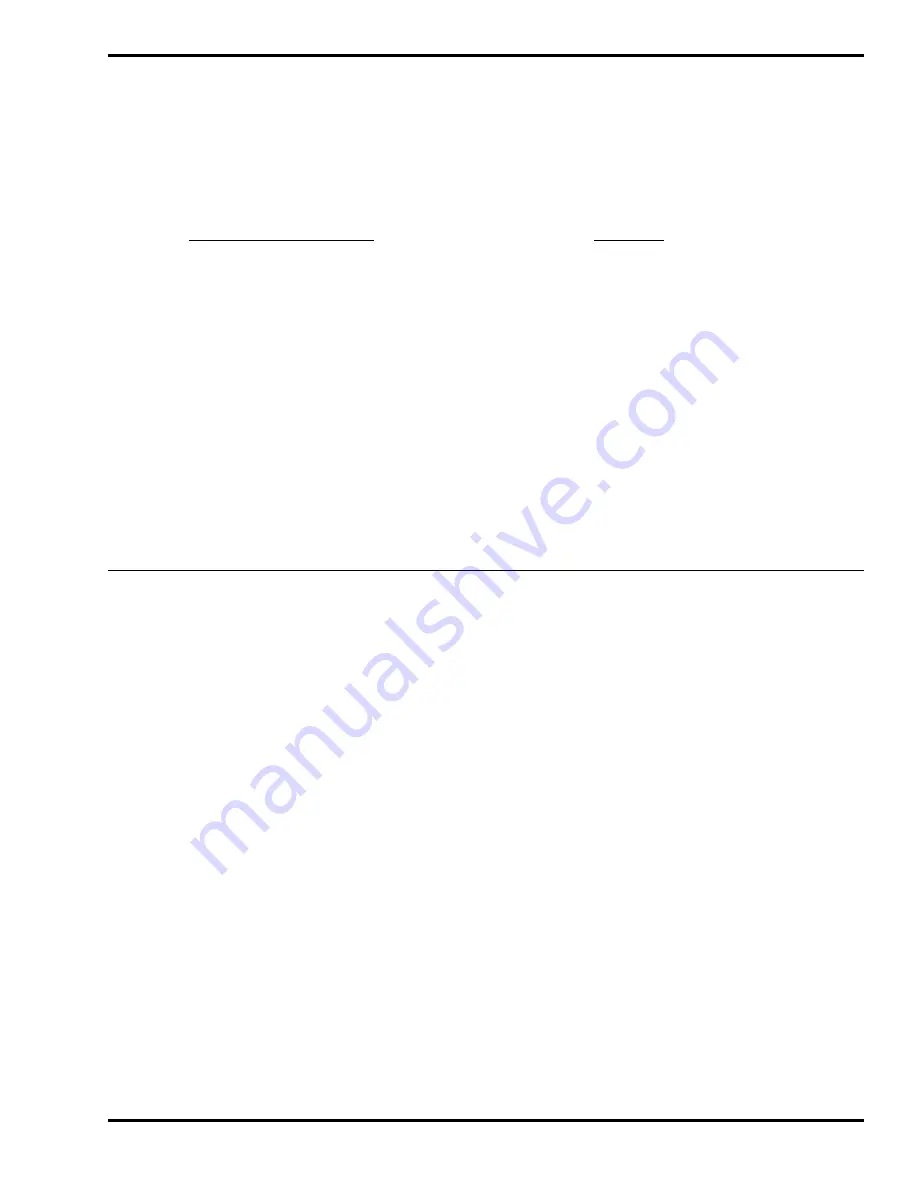
Operator's Manual: Models CB-1750, CB-2500 & CB-3250
4-17
Installing the Pressure Oil Line Components
Installing the Compressed Air Line
NOTE:
Your air compressor system must supply air pressure to the furnace with the following
minimum requirements:
50 psi
and
water trap or dryer.
If you do not have shop air, an optional air
compressor is available. Contact your local Clean Burn dealer for more information.
1.
Run a compressed air line from your shop air to the connector block on the furnace. Use
minimum 1/4" O.D. copper tubing or equivalent for the compressed air line.
2.
Install an easily accessible shut-off valve in the air line so the burner can be serviced without
shutting off the shop air in your service area.
3.
If necessary, install a pressure regulator (additional to the burner air regulator) in the air line, and
set it at 50 psi.
ATTENTION:
DO NOT feed full shop air pressure to the burner or damage to burner
components may occur.
4.
Install a water trap or extractor/dryer in the air line with an automatic drain so compressed air
(rather than water) is supplied to the burner.
ATTENTION:
Water must not be fed to the burner, or the flame will be extinguished and the
burner will shut down. Be sure to drain water from your compressor tank on a regular basis to
keep water out of the air line.
ATTENTION:
It is critical that you adhere to the following specifications for pressure oil line
installation (oil line from the pump to the furnace); if these specifications are not met, the metering
pump will not function correctly and the burner will shut down on reset.
• The parameters for pressure oil line installation are:
Length of Pressure Line
Line Size
Up to 100 feet
3/8" O.D. copper tubing
(Please note that some installations will allow for a greater pressure line length. Contact
your Authorized Clean Burn Distributor for more information.)
•
The pressure oil line must slant up to the burner
with no loops or high points to trap air.
• Local codes may require the installation of an in-line
"Fire-O-Matic" safety valve
.
Be sure to check all appropriate codes to ensure compliance.
1.
Refer to Figures 4H, 4J, and 4K.
2.
Make sure you have purchased all the necessary fittings to complete the installation correctly.
3.
Install the fittings and components as shown in the related illustrations. Be sure to use Permatex
#2 non-hardening gasket sealer to seal every threaded fitting. DO NOT use teflon tape or teflon
pipe dope compounds.
Содержание CB 140
Страница 2: ......
Страница 8: ...TABLE OF CONTENTS APPENDIX C Furnace Service Record C 1 ...
Страница 40: ...Operator s Manual Models CB 1750 CB 2500 CB 3250 3 20 ...
Страница 72: ...Operator s Manual Models CB 1750 CB 2500 CB 3250 5 6 ...
Страница 80: ...Operator s Manual Models CB 1750 CB 2500 CB 3250 7 4 ...
Страница 96: ...Operator s Manual Models CB 1750 CB 2500 CB 3250 9 10 ...
Страница 104: ...Operator s Manual Models CB 1750 CB 2500 CB 3250 10 8 ...
Страница 116: ...Operator s Manual Models CB 1750 CB 2500 CB 3250 A 12 BLOWER ASSEMBLY CB 1750 2 4 5 6 7 2 8 9 10 1 11 12 1 3 I88954 ...
Страница 128: ...Operator s Manual Models CB 1750 CB 2500 CB 3250 A 24 ...
Страница 142: ...Operator s Manual Models CB 1750 CB 2500 CB 3250 C 2 ...