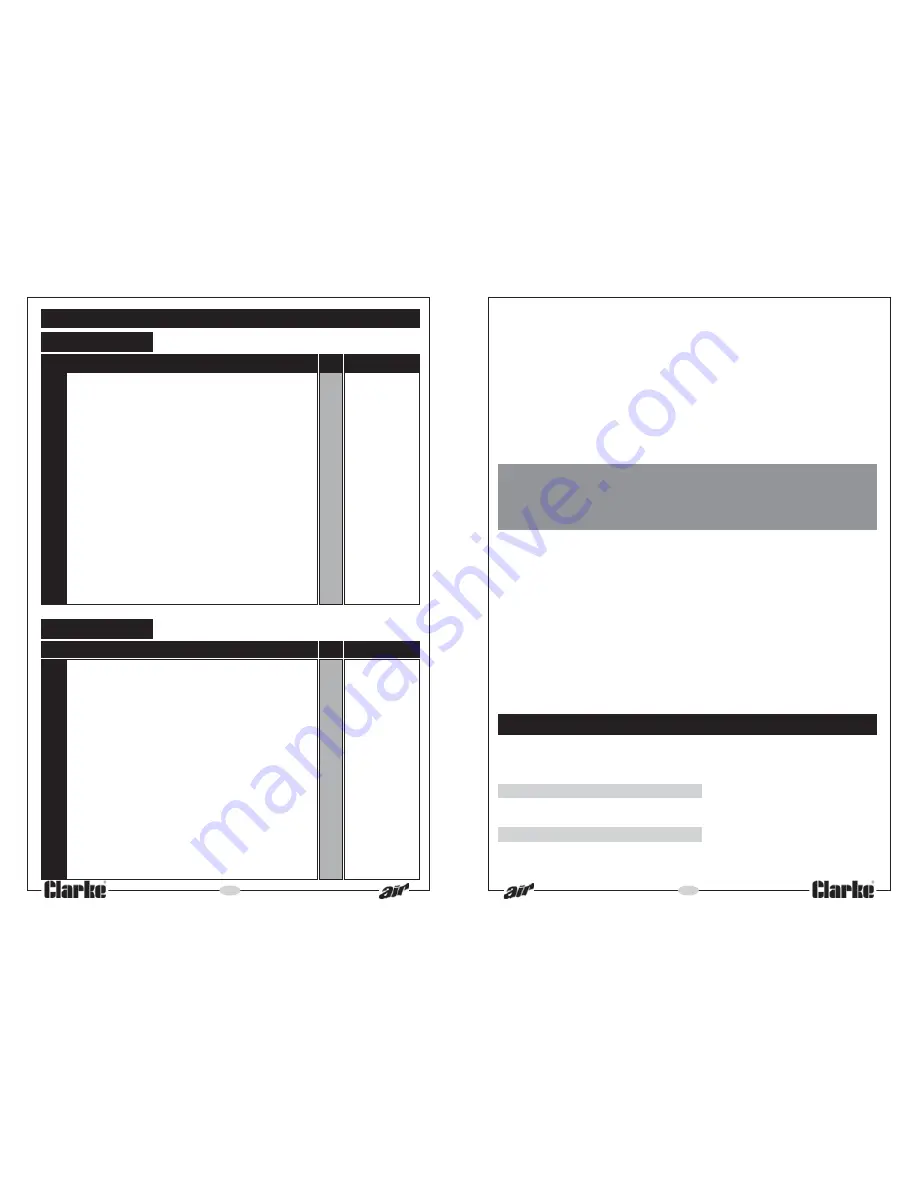
If this is not the case, it is possible that the overload cutout has intervened. This is a safety
device to prevent the motor from overheating. The device will reset when the temperature
falls to a predetermined level. In this event, switch OFF the machine and wait for 5 -10
minutes, before pressing the RESET button , mounted on the top cover, and clearly marked,
and is shown in Fig.2..
Switch ON the machine and try again. If the motor fails to start, after several
attempts, consult your Clarke dealer.
Once the machine has started, turn ON the air supply to your air tool by opening the tap
(F), and turn the pressure regulator (G) clockwise so that your chosen setting, shown on
the label on top of the regulator knob, is in line with the inverted vee mark on the underside
side of the casting. Note that the pressure gauge registers the pressure in the receiver
only.
IMPORTANT:
As no outlet pressure gauge is fitted to this model, the marks on the
Pressure Regulator provide an indication ONLY of the output pressure. If
you are using pressure sensitive tools or equipment, you should insert a
pressure gauge in the airline.
Check to ensure that there are no air leaks at any of the couplings or in other
parts of the system before operating the spray gun or air tool in the normal way.
When the compressor reaches its maximum working pressure, the motor will
automatically cut out, and will restart when the pressure has fallen by
approximately 20 psi. This automatic STOP/START process will continue, as
necessary, to maintain pressure in the receiver.
When you have finished the job in hand
ALWAYS
switch OFF at the ON/OFF switch,
NOT the mains supply, and release any pressure remaining in the system by opening
the drain valve until all air is expelled.
ALWAYS
operate the air tool to further ensure that there is no pressure in the system
BEFORE
disconnecting the tool. Finally, reset the pressure regulator to zero by turning
the regulator knob fully anticlockwise.
- 7 -
ROUTINE MAINTENANCE
IMPORTANT: Before carrying out any maintenance, always disconnect the machine
from the mains supply, drain the air receiver and, if necessary, allow the machine
to cool down before starting work.
Daily
Before use, always open the drain valve and tip the machine on to its end. Hold in that
position until all condensate has drained off.
Do not rest machine on the drain valve
.
Monthly
It is important to keep the compressor clean, with the help of a small soft brush and
vacuum cleaner. In particular, the air intake filter should be inspected at least
MONTHLY
, and more often in dusty conditions, so that it is always kept free of any dirt
- 14 -
1
Drain cock 3/8
1
FN022020000
2
Vibration damper support
1
FN020201000
3
Screw M5x15
2
FN014013042
4
Tank 6 lt.
1
FN126HU0011V
5
Delivery tube
1
FN129HU0011
6
Rilsan tube
1
FN046001000
7
Seal
1
n/a
8
Spring
1
n/a
9
Gasket
1
n/a
10
Non-Return Valve
1
FN347060000
11
Vibration damper support
2
FN020202000
12
Nipple 1/4"
2
FN011017000
13
Pressure switch
1
FN321028000
14
Pressure gauge Ø40
1
FN330006000
15
Safety valve
1
FN347022000
16
Power cable with BSI plug
1
FN101GA0200
17
Pressure reducer with line cock
1
FN319044000
18
OL185 Compressor complete
1
FN516HP01604
B. SPYDER 7
No. Description
Qty
Part No.
n/a - not available
1
Drain cock 3/8
1
FN022020000
2
Vibration damper support
1
FN020201000
3
Screw M5x15
2
FN014013042
4
Tank 2 lt.
1
FN126HU0010V
5
Delivery tube
1
FN129HU0010
6
Rilsan tube
1
FN046001000
7
Safety valve
1
FN347022000
8
Elbow R1/4"
1
FN011002000
9
Pressure gauge Ø40
1
FN330006000
10
Nipple 1/4"
1
FN011017000
11
Pressure reducer with line cock
1
FN319044000
12
Pressure switch
1
FN321028000
13
Power cable with BSI plug
1
FN101GA0200
14
Straight adapter
1
FN199626000
15
Seal
1
n/a
16
Spring
1
n/a
17
Gasket
1
n/a
18
Non-Return Valve
1
FN347060000
19
Vibration damper support
1
FN020202000
20
OL185 Compressor complete
1
FN516HP01604
PARTS LIST - RECEIVER AND COMPONENTS
A. SPYDER 3
No. Description
Qty
Part No.