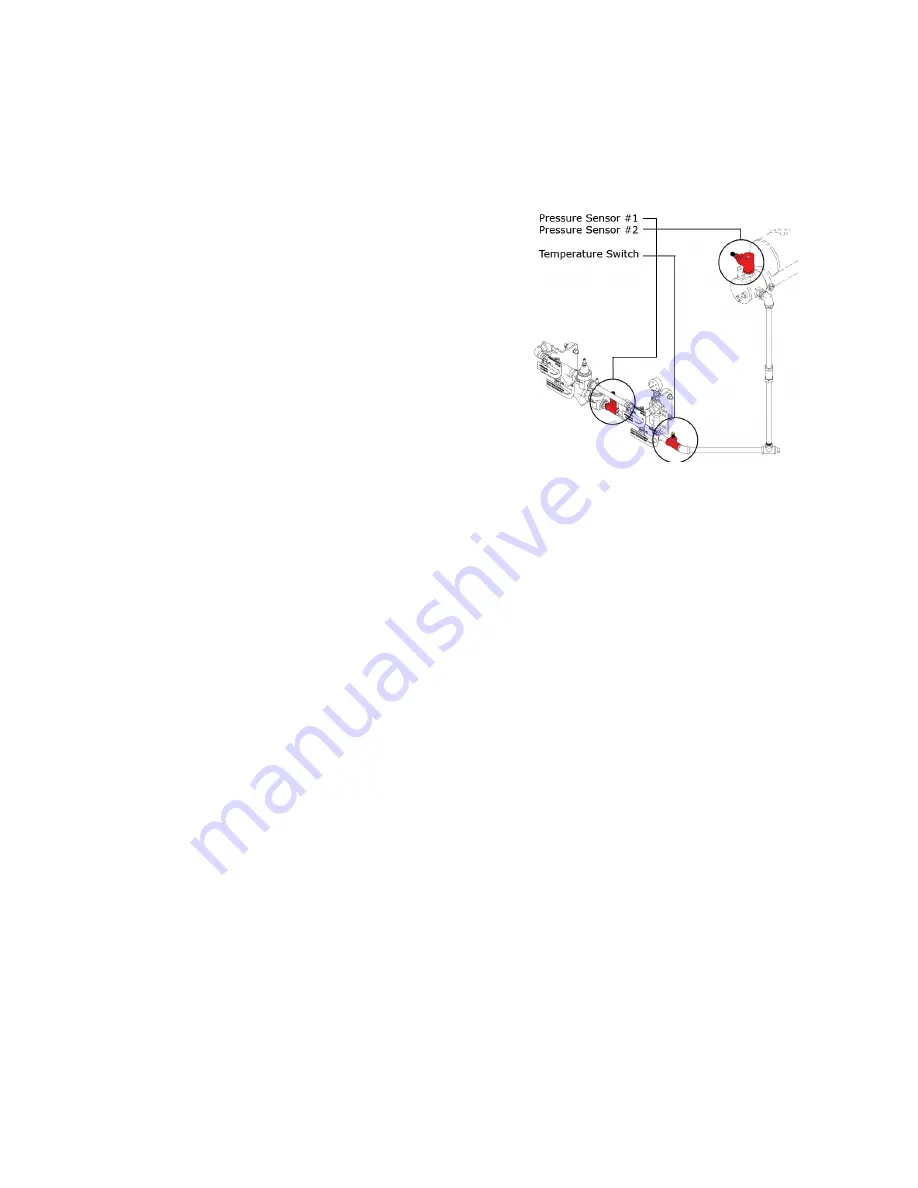
Page 32 of 49
1)
A visual flow indicator and temperature
indicator are installed in the discharge (waste
outlet) piping.
2)
When waste outlet piping is longer than 15ft
(4.6m) and / or the outlet discharges are more
than 4ft (1.2M) higher than the heat
exchanger, the pipe size increased by at least
one size.
3)
Verify that when the correct flow rate is
achieved that the inlet pressure to the heat
exchanger (or CAC) does not exceed 60psi
(4bar)
If you have such an installation, it is recommended
that you run the engine for a period of time at
firepump 150% flow and confirm the visual flow
indicator is showing water flow, the temperature rise
is not excessive (usually no more than 40F (4.5C)
over ambient raw water temperature) and the engine
is showing no signs of overheating.
3.4.7.5 Raw Water Quality, Strainers and
Deterioration of Heat Exchanger (or CAC)
Over time, as the heat exchanger (or CAC) begins to
plug and foul, this pressure will rise and the flow will
diminish which could mean that the heat exchanger
(or CAC) may have to be replaced.
It can be not stressed enough how important it is to
keep the wye strainers within the cooling loop clean:
Most engine failures occur due to plugged cooling
loop strainers!
If the raw water supply has debris in
it (leaves, stones, etc) as the strainer accumulates
more debris (that will not pass thru it), the flowrate
will continue to diminish which will eventually starve
the engine of adequate cooling water flow which will
lead to engine overheat and catastrophic engine
failure.
When this occurs you have no fire
protection!
Clarke recommends that after the initial
engine commissioning and also prior to each weekly
exercise of the engine / fire pump set, both strainers
be removed and cleaned and then re-installed before
starting the engine.
Clarke engines are equipped with an alarm that is
meant to signal diminished raw water flow rate
(terminal 311), possibly due to clogged raw water
strainers in the cooling loop. Refer to Figures 26 and
26A1 for location of sensors. A circuit board located
near the front of the cooling loop monitors
differential pressure between the two sensors and will
send an alarm to the controller if a low water flow
condition exists.
Additionally, a raw water temperature switch will
send an alarm (terminal 310) when temperature of the
water exceeds 105°F (41° C). Refer to Figures 26
and 26A1 for location of switch. If either of these
alarms are active, it indicates that the cooling
system’s capability may be compromised.
Figure #26A1
3.4.7.6 Backflow Preventers
NFPA20 allows for the use of backflow preventers in
the Automatic and Manual flow line of the cooling
loop as required by local code. For specific
application information contact factory.
3.4.7.7 Raw Water Outlet Temperature
Certain local codes may not allow you to discharge
the waste water outlet from the engine heat
exchanger either due to its temperature or it now
being considered hazardous waste. It is
recommended you always check local codes
regarding waste water discharge.
3.4.8 Flow Paths of Engine Cooling System
The engine coolant flows through the shell side of the
heat exchanger (or radiator), engine coolant pump, oil
cooler, engine block and cylinder head, jacket water
heater, thermostat, and expansion tank. On DT2H
engine models the flow also cools the turbocharger
and the exhaust manifolds.
On heat exchanger equipped engines raw cooling
water flows through the tube side of the charge air
cooler, if equipped, and the tube side of the heat
exchanger.